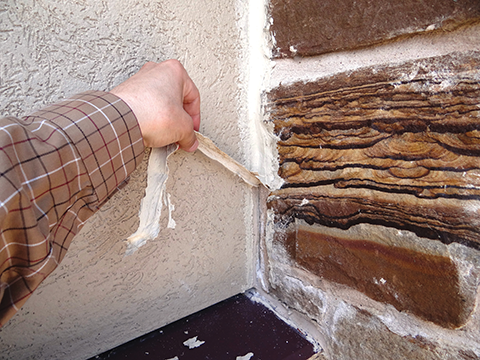
by David H. Nicastro, PE, and Beth Anne Feero, EIT
Sealant is used in the exterior joints of every modern building, but usually incorrectly. Owners have high expectations for performance and durability, but premature sealant failure is common, resulting in air and water infiltration, property damage, and expensive repair work. Design details and installation practices contribute to the service life, but there is a bigger problem in the industry—many sealant products cannot resist movement and weathering, which are their core functions.
It is nearly universal for architectural specifications to demand sealant products to comply with ASTM C920, Standard Specification for Elastomeric Joint Sealants. What most specifiers do not realize is this standard requires only 250 hours of testing in an accelerated weathering machine. For most of the United States, this amount of radiation represents less than two months of outdoor sunlight exposure—and with no simultaneous extension or compression of the sealant specimens.
There is shockingly little data available to demonstrate which products can handle long-term weathering, especially in combination with cyclic movement. The authors’ testing of more than 180 sealant specimens is discussed in this article, with the hope more designers will demand this type of testing from manufacturers.
Sealant durability
Elastomeric sealant joints should be able to last for 20 or more years, but rarely do (Figure 1). For exterior cladding joints in commercial construction, high-performance sealants are needed—those that can accommodate movement of at least ±25 percent of the nominal joint width, adhere to multiple substrates, and withstand long-term weather exposure. Since ASTM C920 has such modest requirements, there are countless products that meet it, with no correlation to durability. Therefore, this manufacturing specification does not provide sufficient guidance to a designer for product selection (Figure 2).
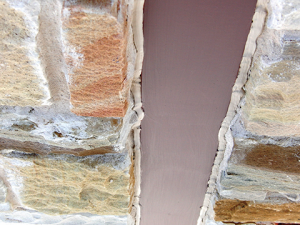
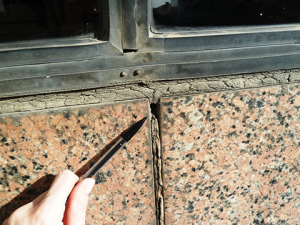
A better predictor of durability is specifying products that have earned certificates from the Product Validation Program created by the Sealant, Waterproofing, and Restoration Institute (SWR Institute). The program validates products by independently verifying they comply with the manufacturers’ claimed movement performance in accordance with ASTM C719, Adhesion and Cohesion of Elastomeric Joint Sealants Under Cyclic Movement (Hockman Cycle), which compresses and extends sealants repeatedly at hot and cold temperatures. While this can add assurance about a sealant’s ability to accommodate joint movement as advertised, it is unfortunate the Product Validation Program does not include any weathering (Figure 3).
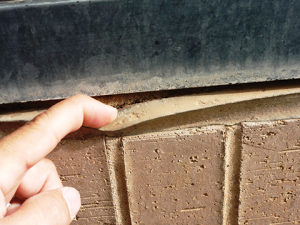
Like the three legs of a stool, durable sealant joints also require support from the project participants.
Designer
The specifier must provide proper joint dimensions and locations, and select appropriate products for the expected movement, environmental exposure, and substrates. As sealant joints will eventually fail, they should not be critical to façade performance—good designs include backup systems so air and water infiltration do not occur simply because of intermittent sealant failures. Excellent design guidance is available in ASTM C1193, Standard Guide for Use of Joint Sealants.
Manufacturer
Silicone sealants have an advantage for weather resistance because of their inorganic chemistry, but formulation is at least as important as the polymer type for achieving long-lasting sealant products. As discussed later in this article, primers are crucial for sealant durability, yet are rarely recommended. Manufacturers should be held accountable for the information they provide, and not just the sealant in the tube.
Contractor
Good design and manufacturing cannot compensate for poor sealant installation. Skilled workers are needed to install sealant meticulously in accordance with industry standards and manufacturer’s requirements, along with the project specifications.
Conventional test data
When designers select a sealant product, they typically expect it to be able to withstand weathering (e.g. ultraviolet [UV] light, rain, heat, and cold) and movement (e.g. joint expansion and contraction). These parameters are addressed by two separate test methods included in the manufacturing specification ASTM C920.
Movement ability
Movement ability is addressed by the previously mentioned ASTM C719. At least for SWR Institute-validated products, a product data sheet should be a reliable indicator of movement ability.
Weathering
For weathering, ASTM C793, Standard Test Method for Effects of Laboratory-accelerated Weathering on Elastomeric Joint Sealants, exposes sealant specimens to 250 hours of radiation exposure (i.e. fluorescent UV, xenon arc, or open-flame carbon arc) as the material is visually assessed before and after it is bent around a mandrel at a cold temperature. This is considered ‘accelerated weathering’ because the machine has more intense radiation than sunlight.
However, the acceleration factor ranges from about 4:1 to 8:1, depending on the amount of natural sunlight being compared regionally. Therefore, this test exposure is really only comparable to about two months outside. Obviously, this is inadequate to predict long-term durability.
Combined testing
Although not performed by manufacturers (or at least not yet reported), there is a test method that provides more realistic weathering: ASTM C1589, Standard Practice for Outdoor Weathering of Construction Seals and Sealants. The standard includes several alternative procedures, each also requiring extension and compression of the sealant specimens in conjunction with weather exposure (Figure 4).

ASTM C1589’s Procedure C is a ‘user-friendly’ method developed so anyone can obtain his or her own data, combining outdoor weathering and cyclic movement. It is becoming widely adopted by consultants and contractors who wish to determine for themselves how sealant performs, rather than relying on manufacturers’ data sheets. One should make no mistake—this is a severe test that quickly weeds out inferior products, but it can take years to obtain long-term data comparing better products.
Using Procedure C, the authors tested 29 different sealant products in an outdoor exposure site in Austin, Texas, with periodic movement. This long-term study is ongoing, but it has already yielded important observations.
Product selection
Products were chosen for testing that comprise the largest market share of high-performance sealants. Most of the products are silicones and urethanes, but several hybrids were included. The selected products are all recommended for use on concrete and aluminum substrates, which are common in façades (both were included in the test specimens).
All the tested products claim to be able to pass C719 testing (as required by C920) with movement of at least ±25 percent; some have SWR Institute validation certificates for ±50 percent movement or more. Most of the sealants are one-part products (i.e. available in common caulk tubes) that cure on exposure to atmospheric moisture. A few two-part products were also included, which require mixing in a separate catalyst.
Specimens
Seven specimens were made for each of the 24 primary sealant products, and three specimens each for an additional five secondary products that were not expected to perform well (Figure 5). The color of each sealant was white to eliminate variability in weather resistance that comes from pigments. (Testing each standard color of each product would exponentially increase the cost, but would certainly be interesting.)
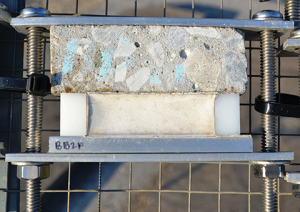
For the primary products, four specimens were primed, and three were unprimed. One of the primed specimens is a ‘file specimen’ (so named because it is kept in a file drawer and not exposed to weathering, but it is tested for movement). Those products with only three specimens were all primed.
The authors believe primer is imperative for long-term durability based on observations of previous testing—this should become more apparent as the current testing continues, with longer exposure and more movement cycles. Primers improve adhesion through a number of mechanisms, depending on the chemistry of the sealant and primer and the type of substrate. They act as surface conditioners, emulsify laitance, and can serve as an extra cleaning step, since they typically contain mostly solvent.
Primer is always required for joints that will be immersed in water, but manufacturers are reluctant to recommend primers for other installations. There is a perceived disadvantage competing with products that claim ‘primerless adhesion’ (despite the fact those products typically use primer on their SWR Institute validation testing).
The specimens were constructed as specified in ASTM C1589, which requires the ASTM C719 standard dimensions of 12.7 x 12.7 x 50.8 mm (½ x ½ x 2 in.). This square cross-section does not match the hour-glass shape that should be used in actual building joints to optimize performance; however, the square shape has been used in movement testing for decades because it provides more reproducible data. Using the same square shape will also allow the data from the current testing to be compared to manufacturers’ published data for movement ability.
The sealant was cured for at least 28 days before testing, which is longer than referenced in ASTM C1589. However, observations of previous testing indicated some products cure so slowly they should not be tested sooner.
Rack
The racks to hold the specimens during their exposure were constructed as shown in ASTM C1589, except metal bars had to be added behind the mesh to which the specimens were attached to reduce deflection (sag under the weight of the specimens was changing their angle of solar exposure). Guy wires were also added to reinforce the racks and to reduce sway from high winds.
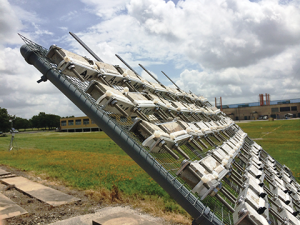
The racks were positioned facing the equator (solar south) and at an azimuth angle of 45 degrees from horizontal (Figure 6). The latitude at the exposure site is 30 degrees north, so a lower rack angle could have been used to increase the radiation by 33 percent for faster weathering; however, 45 degrees is specified in the standard for consistency. A weather station is installed at the site to record the actual solar radiation experienced by the specimens.
Cycle and measurements
The specimens are being tested at ±25 percent movement—a reasonable amount of movement for a specifier to expect a high-performance sealant to achieve. All specimens (except the file specimens) were installed on the racks shortly after the spring equinox at a compressed width of 9.5 mm (3/8 in.), which represents 25 percent compression from their fabricated neutral width. They were extended to 15.9 mm (5/8 in.) after the fall equinox (six months later), which represents 25 percent extension from their neutral width.
Those specimens surviving the first testing were placed back onto the rack in the extended position, and will be moved again into compression when the spring equinox arrives. This simulates the typical annual cycle of building joints closing in the summer as the substrates heat up, and opening in colder winter weather (Figure 7).
Observations of previous testing indicate compression is more damaging than extension for most products. Therefore, starting the testing in compression was harsh, but reasonable to eliminate inferior products quickly. Almost a third of the specimens failed during the first extension—including some products claiming ±50 percent movement ability—as shown in Figure 8.
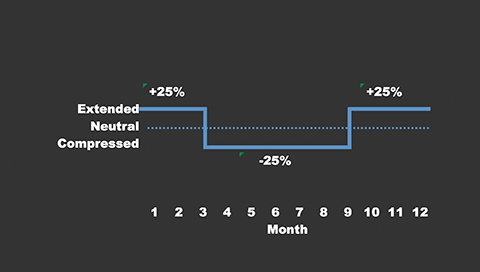
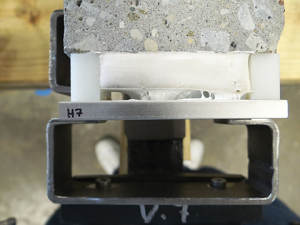
Most products take a ‘compression set’ after being compressed on the rack for six months—in fact, many stayed near their fully compressed width of 9.5 mm after being removed from their specimen holders (Figure 9). However, the amount of compression set did not correlate with failure, demonstrating the mechanism that causes failure during the compression cycle is more complex.
It is likely compression causes stress along the bonding surface, which later becomes visible as adhesion failure once the specimen is pulled into extension. This can also occur in building joints, where adhesion damage during an early compression cycle appears later to be a tension failure, with a gap between the failed sealant and the joint substrate (Figure 10).
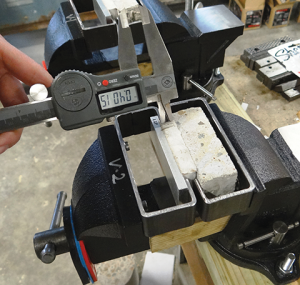
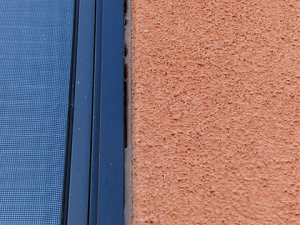
Testing methodology
On removal from the outdoor exposure rack and its individual metal clamping device, each specimen was extended with a hand-crank vise. The vise jaws were fitted with C-shaped clamps to fit around the specimens. The specimens were slowly extended to their final state of 15.9 mm (5/8 in.), or less if failure occurred.
A specimen was considered to ‘pass’ when there was no visible distress during the extension. ‘Distress’ was recorded when there was visible adhesion loss or tearing at any point during the testing, but the specimen was still able to be placed back outside for further weathering. ‘Fail’ was defined when the sealant substantially separated from one of the substrates. Three weeks after extending, the sealants were observed on the racks to obtain the final data reported here; as expected, additional failures had occurred since the initial observations during extension.
Results
After the first round of testing, only 33 of the 184 specimens had no observable distress—however, some of that distress is minor and may not lead to failure. More importantly, 29 percent of the specimens failed already. Figure 11 shows the percentage of failures for each sealant type, and primed versus unprimed behavior (except the hybrid data is combined because there were only a total of 11 specimens).
Figure 11
Specimen description | Number of specimens | Number of failures | Failure | |
Silicone | Primed | 51 | 8 | 16 percent |
Unprimed | 45 | 15 | 33 percent | |
File specimens | 15 | 1 | 7 percent | |
Total | 111 | 24 | 22 percent | |
Urethane | Primed | 30 | 9 | 30 percent |
Unprimed | 24 | 13 | 54 percent | |
File specimens | 8 | 2 | 25 percent | |
Total | 62 | 24 | 39 percent | |
Hybrid | Total | 11 | 6 | 55 percent |
SWRI-validated products | 117 | 20 | 17 percent | |
Non-validated products | 42 | 23 | 55 percent | |
All specimens | 184 | 54 | 29 percent |
In general, the silicone sealants behaved significantly better than the urethanes. Both behaved better than the hybrids, but there were too few hybrid products to be certain of this trend. Primer improved the performance of every sealant product tested but one. In fact, unprimed specimens were twice as likely to fail as primed specimens—this trend is expected to become more pronounced as the surviving specimens continue to weather. The SWR Institute validation was also a remarkable predictor of success; non-validated products were more than three times as likely to fail the first extension as the validated products.
Conclusion
Sealant durability depends on manufacturing, design, and construction. Premature failure can result from any of these, so a designer may not be able to control all the variables. However, specifiers can adopt strategies to optimize service life:
- Specify sealant products that have been validated by the SWR Institute.
- Where possible, use silicone sealant to take advantage of its inorganic polymer that does not deteriorate in sunlight (there are some cases where other chemistry is desirable, which is beyond the scope of this article).
- Use primer on all substrates. Ask the manufacturer’s technical representative to advise on which primers to use and how to apply them, but insist priming be incorporated in the project testing, contractor’s ‘buy-out’ process, and final construction.
- Design joints so sealants are strained less than half their rated movement (e.g. use larger joint widths).
The research presented here shows simply specifying sealant products must comply with ASTM C920 is not sufficient. All the tested products claim to meet C920, but there were vast differences in behavior. Most importantly, C920 requires so little weathering it is misleading for specifiers to rely on it. More robust testing is needed to determine a sealant’s ability to perform with both weathering and movement—this is the purpose of ASTM C1589, as used in the testing reported here.
David H. Nicastro, PE, is the founder of Building Diagnostics Inc., specializing in the investigation of problems with existing buildings, designing remedies for those problems, and resolving disputes which arise from them. He is a licensed professional engineer, and leads the research being performed at The Durability Lab, a testing center at the University of Texas at Austin. He can be reached by e-mail at dnicastro@buildingdx.com.
Beth Anne Feero, EIT, is a graduate student who is studying architectural engineering at the University of Texas at Austin. She serves as the graduate research assistant for The Durability Lab, which researches and tests the durability of building components, identifying factors causing premature failure. She can be reached via e-mail at bfeero@buildingdx.com.
I had no idea that sealants could be used in the joints of buildings. That goes to show how little I know about sealants and things like that. Maybe I should find somebody in my area that can teach me more about this kind of thing. I would love to be more knowledgeable about it.