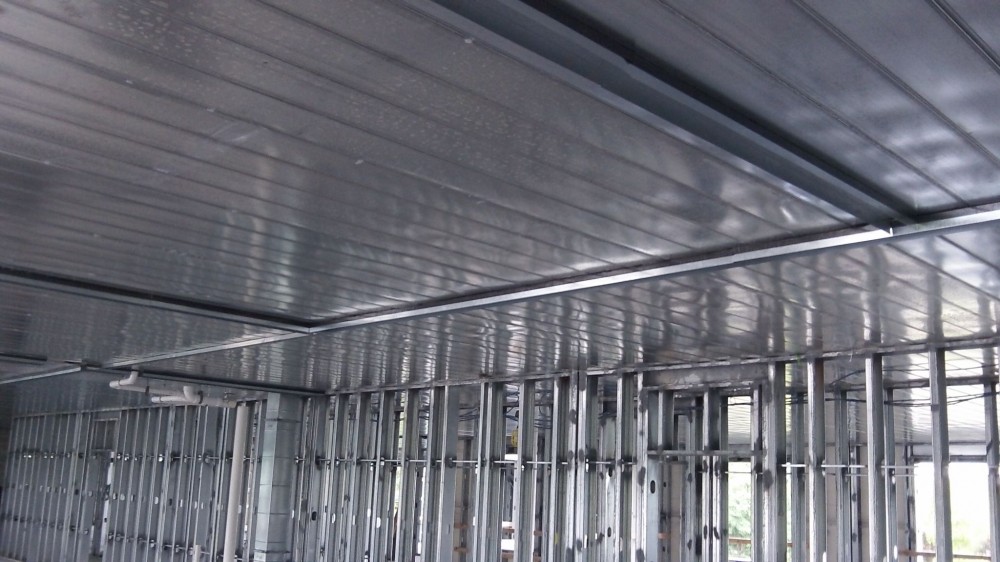
by Gregg Stahl
Integral to commercial building design, passive fire protection is a method for containing a blaze at its source, preventing the spread of flames and smoke throughout a building for a specified time so occupants can evacuate the structure.
Unlike active fire protection devices, such as sprinkler systems, fire alarms, and fire extinguishers, these passive fire protection systems utilize fire-resistant materials embedded in interior building assemblies, lying dormant and hidden from public view until a fire ‘calls’ them into action.
One of the most important areas of concentration for these passive fire protection design strategies is the wall assembly. To ensure optimal fire protection, the building codes require these assemblies to be evaluated by industry standards to determine their fire performance. This article provides examples of fire-rated wall assemblies and passive firestop systems. It also describes the testing they must go through to achieve their fire ratings while covering best practices for their specification and installation.
Fire-rated wall assemblies
Total passive fire protection cannot be achieved through the use of one product—it requires an assembly of several different fire-resistant materials that work together systematically to slow the passage of flames, smoke, and toxic gases. For example, most exterior and interior commercial wall assemblies feature light-gauge steel studs, fiberglass insulation, and gypsum wallboard, which are all materials possessing naturally high fire resistance. The three materials perform well together in wall assemblies and are used in various combinations of thickness and numbers of layers to increase fire resistance.
The fire resistance of wall assemblies is evaluated by two industry standards—ASTM E603, Standard Guide for Room Fire Experiments, and ASTM E119, Fire Tests of Building Construction and Materials. These standards rate the assemblies based on how many hours they prevent the passage of fire, heat, smoke, and gases.
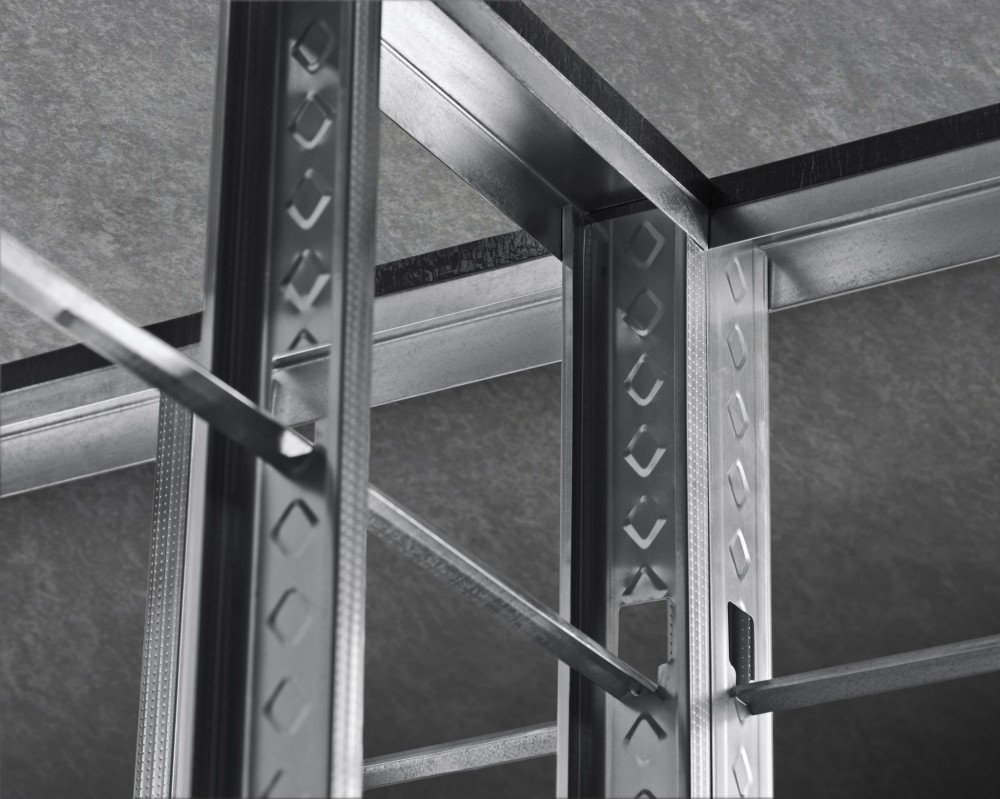
ASTM E603 measures temperatures, smoke generation, ignition to flashover time, combustion gas, and total energy release as a fire moves from one room to the next. Referred to as the ‘room corner test,’ it involves a corner of a room constructed in an accredited testing facility, using standard building materials. Materials to be tested are mounted on the walls and ceiling of the room corner. A fire source, usually a wood crib or a diffusion burner, is placed in the corner and ignited. The test mimics a wastebasket-sized fire that spreads to something nearby. To achieve a satisfactory performance rating, the tested assembly must not allow the spread of smoke and fire or generate excessive amounts of smoke.
ASTM E119, on the other hand, establishes a wall assembly’s effectiveness to act as a fire barrier. In this case, a wall is tested for structural integrity and the ability to contain a fire for a quantified period. The assembly is mounted to a specially constructed furnace and gas burners are lit as thermocouples record temperatures and the flames mimic heat from an adjacent fire. Observations are made through viewing windows in the furnace and with instrumentation. Temperatures and the length of time before the system fails are recorded.
This test method uses a furnace-heating schedule, or timed increase of temperature, which brings the furnace up to 538 C (1000 F) in five minutes, up to 927 C (1700 F) in one hour, and to 1010 C (1850 F) in two hours. Assemblies must survive these temperatures to be successfully fire-rated by the standard. A hose stream test follows to measure the assembly’s resistance to water pressure after the burn.
Fire-resistant wall assembly examples
Non-combustible, non-load-bearing wall assemblies must be constructed from fire-resistant materials. All combinations of assemblies are tested to establish hourly fire ratings. In the following paragraphs, this article examines three common variations of such assemblies.
Typical one-hour-rated assembly, UL Design V450—non-combustible, non-loadbearing1
One layer of 15.9-mm (5/8-in.) Type X gypsum board2 is applied horizontally or vertically to either side of minimum 92-mm (3 5/8-in.) steel drywall framing spaced on 600-mm (24-in.) centers. Gypsum board is fastened to the steel studs using 25-mm (1-in.) Type S bugle-head steel screws at 200 mm (8 in.) on center (oc) perimeter and field for horizontal applications, or 200 mm oc perimeter and 300 mm (12 in.) oc field for vertical applications. Joints must be offset. For extra fire resistance, thermal resistance and acoustic control, add 89 mm (3 1/2 in.) of fiberglass batt insulation to the wall cavity.
Typical two-hour rated assembly, UL Design V450—non-combustible, non-loadbearing
Two layers of 15.9-mm (5/8-in.) Type X gypsum board is applied horizontally or vertically in accordance to the fire assembly to either side of minimum 63.5-mm (2 1/2-in.) steel drywall framings spaced on 600-mm (24-in.) centers. The base layer of gypsum board is fastened to the steel studs using 25-mm (1-in.) Type S bugle-head steel screws spaced 400 mm (16 in.) oc perimeter and field.
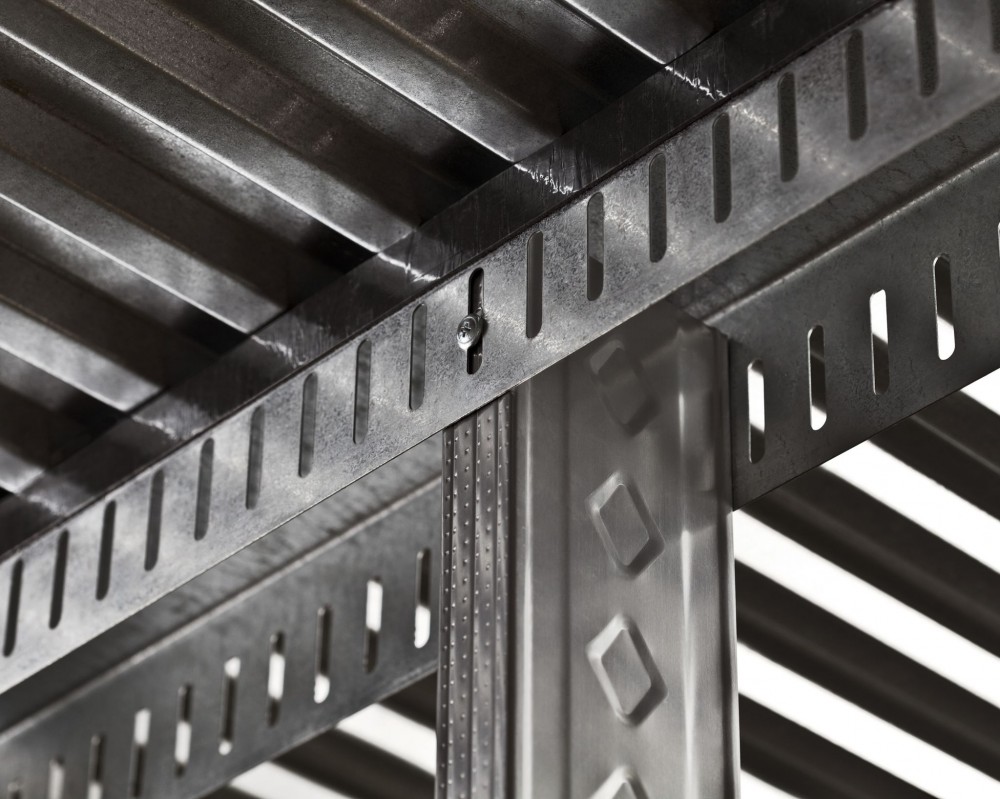
The same screw placement and use of a 130-mm (5 1/8-in.) screw apply to the face layer as well. Joints must be offset on the opposite sides of the wall and between layers. For extra fire resistance, thermal resistance, and acoustic control, 64 mm (2 1/2 in.) of fiberglass batt insulation can be added to the wall cavity.
Area separation firewalls
Another important assembly demanding fire resistance performance is the area separation firewall. These walls are required between adjacent apartments or townhouses, and in some cases, they are required in commercial and institutional buildings.3
The area separation wall is designed to allow for collapse of the construction on the fire-exposed side, without collapse of the entire wall. To do this, aluminum breakaway clips attach the separation wall to the adjacent framing. When one side of the separation wall is exposed to fire, the clips are designed to soften and break away. This allows the structure on the fire side of the separation wall to collapse, while the clips on the unexposed side of the separation wall continue to support the separation wall.
A typical area separation firewall assembly consists of two layers of 25 x 610-mm (1 x 24-in.) gypsum shaftliner panels inserted between floor and ceiling runners with steel H-studs installed between adjacent panels. A 19-mm (3/4-in.) air space must be maintained between steel components and adjacent framing. An 89-mm (3 1/2-in.) layer of fiberglass batt insulation in the wall cavity is also recommended.
Proper installation of a fire-rated assembly is important. Good construction practices—executed in accordance with manufacturers’ recommendations and the fire-rated assembly’s requirements—are needed to ensure the assembly built in the field is representative of the one tested. However, an additional passive firestop system is needed for these assemblies to seal off the passage of flames, smoke, and toxic gases through the joints and penetrations of a wall assembly.
Passive firestop systems
Penetrations are often made through fire-rated wall assemblies for switches, electrical boxes, power outlets, or the passage of pipes, cables, or HVAC ductwork. At these locations, as well as wherever there are wall perimeter joints, it is necessary to seal the openings off with firestop materials. There is no one universal product that will work for every firestop application. Traditionally, specified materials include:
- sealants;
- intumescent materials;
- sprays (i.e. spray-applied compounds, usually latex or silicone-based, that provide firestopping through penetrations, voids, and construction joints of the wall assembly, framing, and ductwork); and
- foam blocks or pillows (i.e. self-contained, intumescent firestop products for through-penetration, such as where ductwork or support beams pass through wall assemblies—on exposure to flames, they intumesce to form a hard char that tightly seals penetrations against flame spread, smoke, and toxic gases).
It is important to select products that have been appropriately tested to meet applicable fire safety standards.
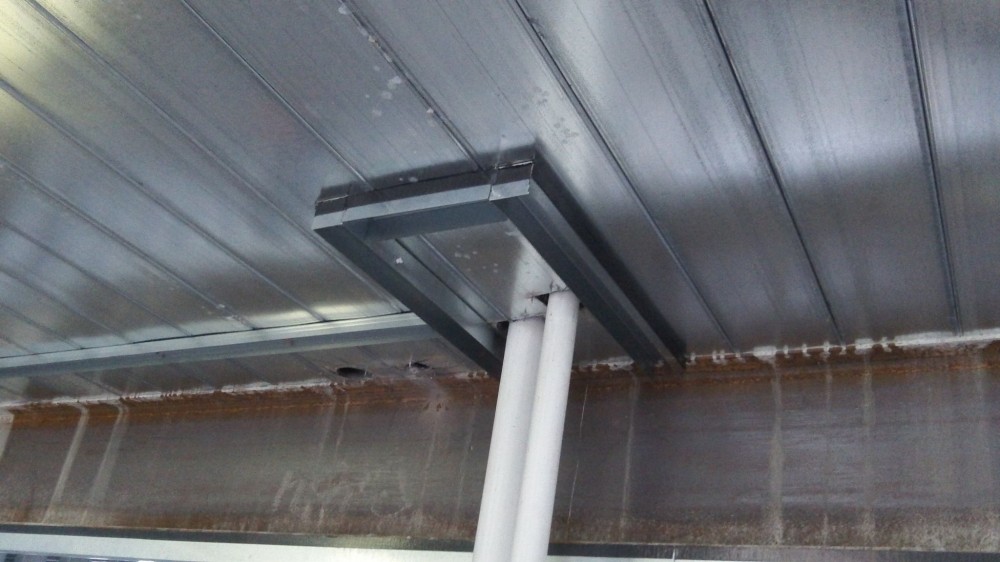
Sealants
Sealants are the most recognized group of firestop products due to their versatility, as caulk can have various uses on construction projects, such as sealing penetrations and construction joints. These products are available in various forms and chemical formulations. Firestop sealants in caulk, self-leveling, and spray grade are readily available in silicone, latex, and solvent-based products. They often require the addition of a backing material (e.g. polyethylene backer rod) in the system for support.
Often, the effectiveness of their application is governed by the ambient temperature. Consequently, in unheated spaces during construction, this may be an issue.4 Additionally, any overlapping work from other subcontractors—such as previously installed mechanical ductwork or piping—can interfere with the sealants’ application and inspection.
Intumescent materials
Intumescent materials are firestop products that expand in volume when exposed to heat or flames exceeding a specified temperature. They are one of the primary groups of products employed in applications where one of the assembly components deteriorates or burns away during fire exposure or where surfaces are uneven and a tight fit is impossible.
The expansion of the material closes the void that is created when the item melts or burns away, maintaining the fire-rated assembly’s integrity. Intumescent firestop materials come in various forms, from caulks to metallic collars with intumescent strip linings, with each product being designed for a specific purpose.
Integrated firestop systems
The integration of intumescent firestop materials onto steel framing members is one of the most recent high-performance firestop innovations. In many commercial and institutional projects, architects and specifiers are now using steel tracks manufactured with a factory-metered dosage of intumescent material applied in a controlled environment to the track flanges. These products help architects specify product and assembly solutions for both hidden and exposed aesthetic conditions where fire, smoke, and sound resistance ratings are required.
Single-source construction of wall assemblies and installation of joint protection can now be achieved by drywall contractors, eliminating any trade overlap issues common to installing traditional firestop materials. Track members having the intumescent material already integrated can provide up to 76 mm (3 in.) of total movement and up to three-hour fire-rated protection.
These integrated firestop products are easier to install than traditional firestop materials. Contractors simply install the track member, which includes the intumescent tape, at the top, bottom, or sides of the wall. This eliminates the need to return and install intumescent caulking at a later time, eliminating multiple labor and material operations.
Passive firestop system evaluation
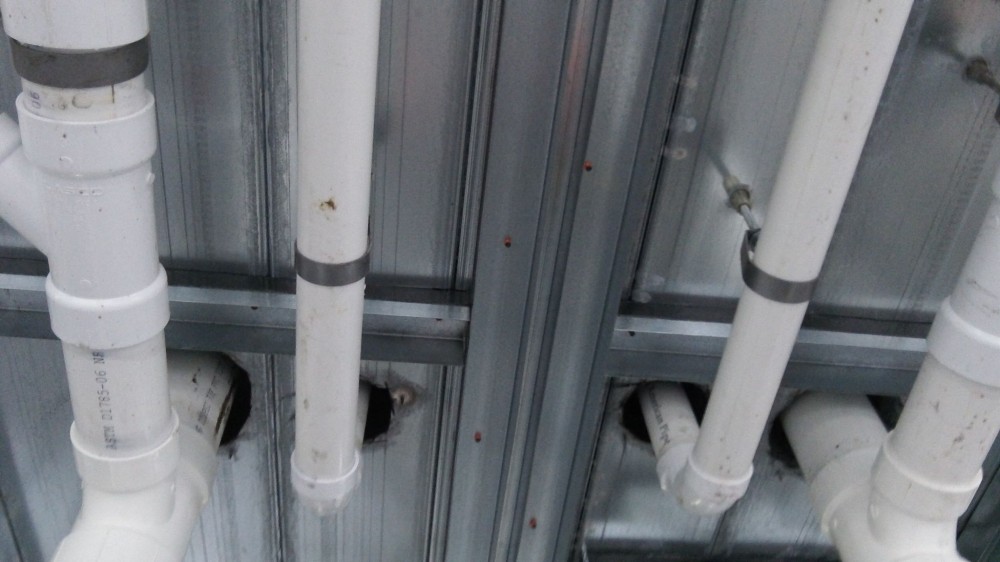
Like wall assemblies, the fire performance of passive firestop systems must also be evaluated by various industry standards. ASTM E1966, Standard Test Method for Fire-resistive Joint Systems, is one standard that covers sealants, coatings, and materials used in joints. ASTM E814, Fire Tests of Through Penetration Firestops, is the complementary test to ASTM E119 that evaluates penetrations through a tested, fire-resistive (i.e. ASTM E 119-tested) wall or floor assembly.
The test involves a standard time-temperature curve and a hose stream test; it assigns ratings based on ‘T’ (temperature rise) and ‘F’ (flame occurrence through the firestop/penetration). The objective of specifying this type of system is to return the floor or wall to the compartment’s original fire rating. An ‘L’ (air leakage) rating can also be assigned. Air leakage simulates smoke movement through a penetration, measured in cubic feet per minute.
Conclusion
Fire-rated wall assemblies and passive firestop systems are crucial elements in the design of all commercial buildings. They help increase occupant safety and allow project teams to meet building code requirements.
By following the guidelines for fire-rated wall assemblies and passive firestop systems, building and design professionals can produce interior walls that will help protect building occupants against flames and smoke for a specified time. Combined with active fire protection methods and occupant education, these passive fire protection techniques provide a safer, more balanced strategy for protecting a building and those inside.
Notes
1 Underwriters Laboratories refers to this design as BXUV.V450. For more, visit bit.ly/1e5sKvR. (back to top)
2 Type X is standard fire-resistant gypsum board. Type C offers stronger resistance. (back to top)
3 In general, the purpose of area separation walls is to provide extra fire resistance between adjoining residential or commercial building units. They impede sound transmission, as well as the spread of fire from one unit to the next. Not all commercial or institutional buildings are going to have multiple tenants. (back to top)
4 In the cooler seasons, installers may have to employ the use of temporary, portable heaters to reach the proper temperature to ensure sealant adhesion. However, contractors should be keenly aware of the safety concerns when using these instruments in the work environment. (back to top)
Gregg Stahl is the director of product development at ClarkDietrich Building Systems, a manufacturer of steel framing and finishing products for the commercial construction industry. With more than 25 years of industry experience, he has served in multiple capacities at ClarkDietrich, including vice president of its subsidiary Vinyl Corp. Stahl has also held various roles within sales and product management. He can be reached at gregg.stahl@clarkdietrich.com.
I am looking for a fire/barrier with 1 hr rated specification to be placed in front of existing impact window which my counties permitting requires. I have 7 panels 59″ wide and need 24″ high for to patio enclosures.