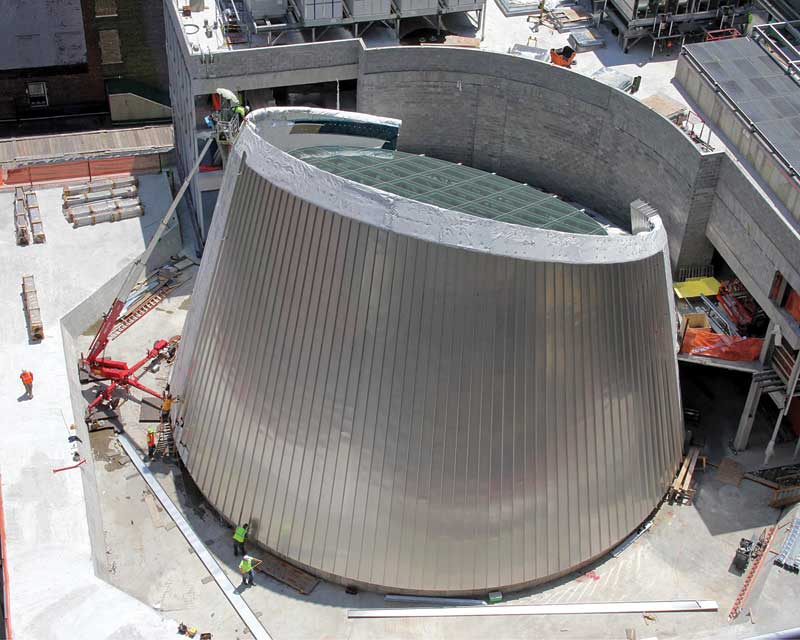
by Chuck Mears, FAIA
Over the past several decades, the confluence of value engineering and sustainable design has enabled construction of better, more efficient buildings. Both trends play crucial roles in realizing the quality, durability, and longevity of the built environment. Often, value engineering and sustainable design can identify the best material for the application and install it in the most efficient way possible. Such careful consideration of materials and processes generally results in less waste, accurate use of material, and efficient use of resources and manpower.
One material consistently meeting the criteria for both purposes is cold-formed steel (CFS). While the use of CFS in construction projects is not new, it is being used in innovative ways to provide environmentally responsible, cost-effective construction methods. This article explores the use of CFS as a new way to frame apertures and create support for shaped façades, as a lighter and more flexible replacement for structural steel, and as a more geometrically appropriate way to achieve curved surfaces.
CFS framing provides the highest strength-to-weight ratio of any building material. It is ideal for creating curves because of its ability to be flexed and retain its shape. From a sustainability standpoint, CFS is lighter than other framing materials, reducing shipping costs. It is completely recyclable and can save time onsite with ease of panelization offsite.
CFS will not rot or warp. It neither splits nor cracks and will not expand or contract with moisture content.
The material is produced in strict accordance with national standards, with no regional variations.
These standards include:
- American Iron and Steel Institute (AISI) S100, North American Specification for the Design of Cold-formed Steel Structural Members;
- AISI S210, North American Standard for Cold-Formed Steel Framing–Floor and Roof System Design;
- ASTM C955, Standard Specification for Load-bearing (Transverse and Axial) Steel Studs, Runners (Tracks), and Bracing or Bridging for Screw Application of Gypsum Panel Products and Metal Plaster Bases;
- ASTM C645, Standard Specification for Non-structural Steel Framing Members.
Especially in curved applications, these benefits make CFS a viable alternative to wood, red iron steel, and poured concrete. From a cost standpoint, CFS prices remain fairly stable, and the materials’ use often results in less waste than wood.
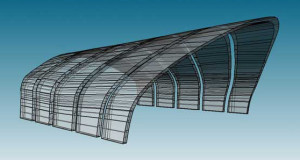
Unitized panels offer design innovation and cost efficiencies
Unitized CFS panels for interior and exterior surfaces have the ability to achieve special effects with curves. Fabricating the units offsite decreases installation time compared with stick framing on the jobsite, especially when both simple and complex curves are involved. The use of total station surveying technology—an electronic/optical instrument used to chart points in space—provides global positioning system (GPS) coordinates that enable installation teams to pinpoint precise locations and make complex installations easier.
Pre-curved unitized CFS framing solutions created in a controlled environment offsite are not impacted by weather. They offer uniform quality constructed to project tolerances, are designed with structurally engineered hoisting plates and connection points, and can be delivered to the jobsite sequentially ordered and ready to install.