SPECIFICATIONS
by Chris Bennett, CSI, and Keith Robinson, RSW, FCSC, FCSI
Designers specify polished concrete floors because they are durable and easy to maintain. They also reduce material use because existing slabs, or purpose-made slabs, can be employed to create a final floor finish. Additionally, polished concrete has a broad aesthetic range. Color can be selected through the use of pigments, dyes, acid stains, or even sand and aggregate choice. Aggregates can be exposed to different levels. Special aggregates such as marble chips and colored glass could also be added. The reflective characteristics of a polished concrete floor can be expressed from low-sheen matte to high-gloss, mirror-like reflective finishes. It is also straightforward to specify slip resistance using quantifiable coefficient of friction (COF) values and testing procedures. Unfortunately, many of the benchmarks used to specify and build polished concrete floors focus on aesthetics alone, leaving durability, sustainability, and COF unanswered.
Polished concrete’s popularity has increased in the last 15 years. Despite this growing demand, the industry has not been able to standardize the language to describe durable, safe, and attractive concrete floors. During polished concrete’s infancy, specifiers, designers, and owners turned to contractor terms like grit to help them establish a baseline without fully appreciating the variety of solutions this word represents, and opened themselves up to undefinable benchmarks.
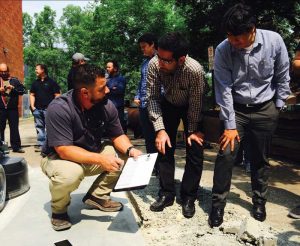
Use of contractor terms
Grit describes the abrasive size of industrial diamonds in the matrix of grinding and polishing pads used to polish concrete. It helps craftspersons select tooling choice for the refinement steps they are working on, and navigate the execution of a polished concrete floor. However, it does not communicate the design outcome by using a qualitative approach. Though grit sizes are fairly universal, abrasive grains can vary from metal chaff to industrial diamond and other materials. There can be pure mixtures of abrasive grains of only one size or the matrix of the polishing puck (often called a diamond tool) can contain variable dimensions to create an average size. The size and shape of the polishing puck also affects outcomes on
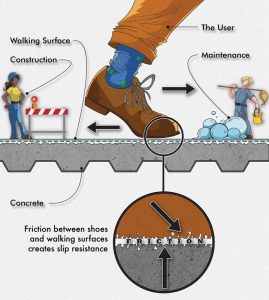
Image © A New Concrete Glossary, created by Mike Smith and Kathryn Marek
the floor, delivering different scratch patterns and refinement levels. As concrete varies in hardness, so do the diamond polishing pucks. An individual manufacturer can produce a variety of abrasive tools within a specific grit category. In other words, a company could offer multiple types of abrasive tools varying in size, shape, and matrix material (all with different scratch patterns), and yet designate them with an identical grit number. Unless one is truly skilled in the trade and understands the thousands of differences that the word grit could represent, the specifier is in unfamiliar territory that will quickly land him/her in a means and methods quagmire.
There are other problems with using the word grit that may not be readily considered. Grit also describes the size of abrasive grains on janitorial buffing and burnishing pads, opening up even more variables to this word. These types of pads can be used with topical solutions that can become shiny through burnishing. Instead of a polished concrete floor, a client can unknowingly be handed a coated shiny doppelgänger lacking durability and quantifiable COF. Further, some styles of epoxy resin coatings are sold in solid form as diamond tools containing abrasive grains. These, therefore, carry a grit designation (i.e. 400, 800, etc.) However, what actually happens with these types of products is that they are super-heated under the weight of commercial grinders. The high-speed revolutions of the grinding cause the epoxy to melt and become smeared across the concrete and leave the floors with a shiny coat through resin transfer.
In addition to the sheen and the level of grinding for a polished concrete, what is the language that should be included on the specifications about the staining proof and COF? are there any ASTMs to address this?
Thank you
Luis,
A good place to start is with ANSI B101.3 for dynamic coefficient of friction as well as ASME B46.1-2009. Feel free to contact directly for more information.
Check with Concrete Polishing Council of the American Society of Concrete Contractors, they are the recognized experts on Polished Concrete today.
Deke,
Thanks for comment. However, I do not know if I would personally agree that they are the recognized experts.