The growing concern with vapor intrusion
by Wesley Robb
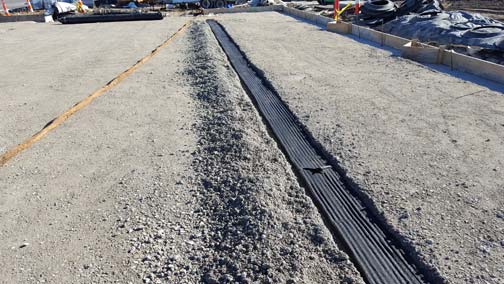
Photos courtesy Vapor Mitigation Strategies
In extreme cases, vapors may accumulate in dwellings or occupied buildings to levels that may pose near-term safety hazards (e.g. explosion) or acute health effects. This occurs when there is a migration of chemical-containing vapor from a subsurface source into an overlying building.
At various sites, manufactured chemicals such as petroleum hydrocarbons and chlorinated solvents can be present in the soil, groundwater, or soil vapor. These chemical vapors can make their way into a building’s habitable zone, having a severe negative impact on a space’s indoor air quality (IAQ). The issue of vapor intrusion has become a major consideration for both site-selectors choosing a location for development and architects designing a building.
The types of chemicals of particular concern are:
- volatile organic compounds (VOCs), such as trichloroethylene (TCE);
- semi-volatile organic compounds, such as naphthalene; and
- petroleum hydrocarbons, such as gasoline.
So what does this mean?
Properties being developed or currently occupied by buildings on contaminated soil, groundwater, or soil vapor, or are adjacent to properties similarly contaminated, require the evaluation of the vapor intrusion pathway. Typical businesses associated with the risk of vapor intrusion are dry cleaners, printers, manufacturers, automobile repair shops, and gasoline/service stations. Should an evaluation determine there is a risk for the migration of contaminated vapor into the indoor air of those existing or planned structures, it is necessary to consider how that can be mitigated. At this point, the architect must consider the inclusion of a vapor mitigation barrier.
As of late, the U.S. Environmental Protection Agency (EPA) has paid particularly close attention to TCE due to findings this industrial solvent poses potential human health hazards, including cancer. Of notable concern is the possibility fetal heart defects may result if pregnant women are exposed to TCE in their earliest stages of gestation. Mitigation systems have proven to be effective in proactively diverting dangerous vapors from entering a building.
Chemical vapor barriers are not to be confused with standard moisture barriers (often simply referred to as ‘vapor barriers’). The latter is designed to keep moisture out of a building in an attempt to reduce the potential for mold, which can also be a health risk, and water damage. Chemical vapor barriers, on the other hand, are designed to not degrade or allow penetration of vapor phase chemicals. The fact moisture barriers are often described as ‘vapor barriers’ in the industry can lead to confusion.
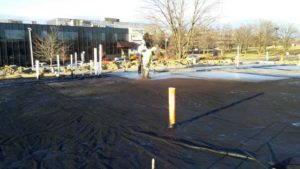
Generally, there are two approaches to the construction of a vapor mitigation system. One such option consists of the installation of a polyethylene or polyolefin tarp product. Another, more advanced construction product uses a spray-applied composite membrane in addition to specified tarp materials to provide the spray material a substrate on which to adhere. The polyethylene/polyolefin barrier materials are often recycled from post-consumer products that can make them less expensive. However, in the absence of a spray-applied composite membrane, these barriers are often difficult to seal around penetrating uprights and slab perimeters.
Those vapor mitigation systems employing a combination of specified tarp materials and a spray-applied composite membrane have the advantage of superior sealing at tarp seams, upright penetrations, and slab perimeters. Often, installation of these vapor mitigation systems is conducted only by manufacturer-trained installers. Additionally, these products can include a warranty that is only enforceable when the installation is inspected by a manufacturer-trained inspector, who certifies the thickness of the spray-applied composite material and confirms the effectiveness of the barrier as demonstrated by a smoke test. The choice between these two approaches will depend on the assessment of the risk for vapor intrusion and the acceptable risk level of the responsible party to potential litigation.
It is important for architects and their environmental consultants to perform their due diligence on a site before specifying a chemical vapor barrier. The lack of a vapor mitigation system where it is needed, or the installation of an inadequate one, can lead to unwanted litigation and may put the health of the building occupants at risk.
Wesley Robb is the director of technical strategies and applications at Vapor Mitigation Strategies, a Wellington Environmental Company. He has 23 years of environmental field and laboratory experience, including several years of soil vapor sampling and analyses. Since joining Wellington in 2004, Robb has managed onsite activities of various kinds, including underground storage tank removals, soil remediation, Phase I investigations, and vapor/soil/groundwater sampling. He can be reached at wes@vapormitigationstrategies.com.