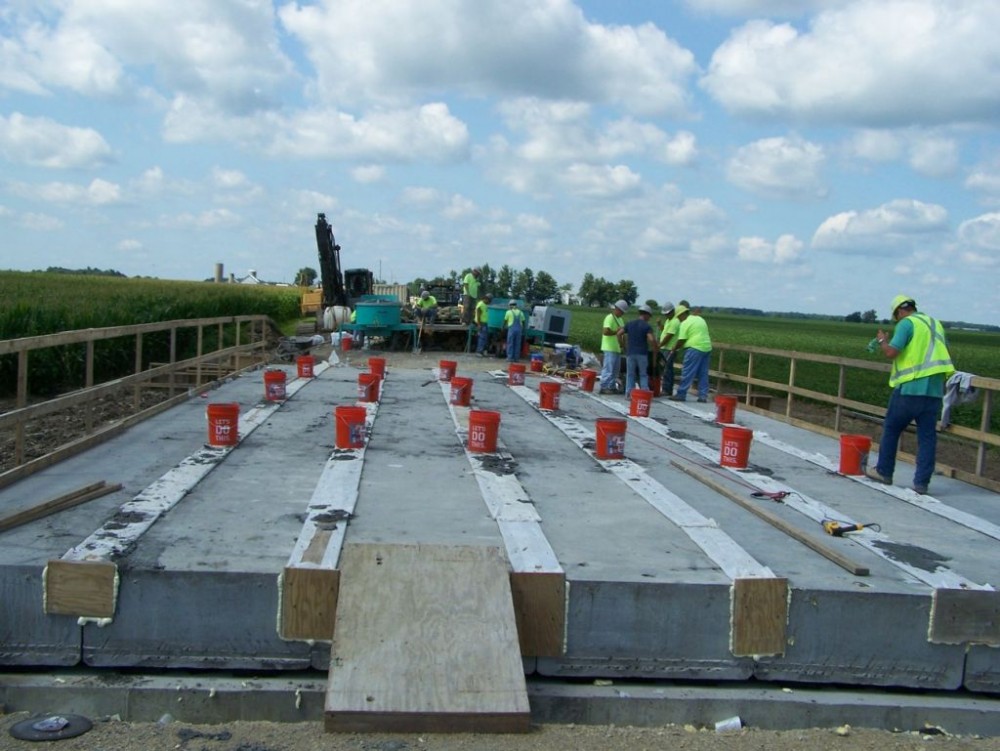
by Eric Steinberg, PhD, PE
Out of the many types of bridges used across the country, adjacent prestressed, concrete box-beams have become popular for short and medium spans. Since these bridges are cost-effective, fast to construct, and easy to design, they are preferred by many state and local agencies. Currently used in about two-thirds of the country, many of these bridges are now approaching the end of their life span.
Despite the widespread use and preference of these box-beam bridges, there are still some disadvantages associated with durability and effectiveness. As part of a recent project with a team of students and colleagues, this author tested a box-beam bridge to failure in order to gauge behavior and overall capacity.
This project prompted a major understanding in the way box-beam bridges perform. It showed the bridges perform well under stress, but the longitudinal bridge joints are susceptible to cracking and leakage, leading to accelerated corrosion, and reduced load transfer. The research also demonstrated complex behavior in the box-beam bridges due to thermal cycles, craftsmanship, and loading.
While box-beam bridges have clear advantages, it is important to find ways to ensure they have a longer lifespan and handle the issues related to the longitudinal bridge joints. Right now, these bridges last about 30 years (depending on various factors), but if this time frame can be expanded, then owners will save on long-term infrastructure replacement costs. One solution this author is currently examining at Ohio University’s Russ College of Engineering and Technology is a new use of ultra-high-performance concrete (UHPC) in box-beam bridge design and construction.
UHPC is an effective concrete material with superior properties to typical concretes and grouts, because it has a compressive strength greater than 150 kPa (22 psi) and a tensile strength in the range of 7 MPa (1 ksi). Also, the steel fibers allow for ductile behavior. According to the Federal Highway Administration (FHA):
The mechanical and durability properties of UHPC make it an ideal candidate for use in developing new solutions to pressing concerns about highway infrastructure deterioration, repair, and replacement.
This author first became involved with the material in September 2002 during a research trip to Paris, France, where it had been developed and was being used. There are currently 28 UHPC bridges in the United States and 26 in Canada. UHPC is expected to be specified for more projects, and there are numerous signs of the material’s rising importance in civil engineering. In November 2015, for example, the 1st International Interactive Symposium on Ultra-high-performance Concrete will take place at the University of Connecticut. (This author is part of the organizing committee.)
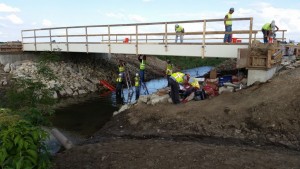
Overall, UHPC is an expensive material, and full bridges made out of this type of concrete will significantly increase construction and design costs. The breakdown is as follows:
- 712 kg/m3 (1200 lb/cy) of portland cement (28.5 percentage by weight);
- 1020 kg/m3 (1720 lb/cy) of fine sand (40.8 percent);
- 231 kg/m3 (390 lb/cy) of silica fume (9.3 percent);
- 211 kg/m3 (355 lb/cy) of ground quartz (8.4 percent);
- 30.7 kg/m3 (51.8 lb/cy) of high-range water-reducer (HRWR) (1.2 percent);
- 30 kg/m3 (50.5 lb/cy) of accelerator (1.2 percent);
- 156 kg/m3 (263 lb/cy) of steel fibers (6.2 percent); and
- 109 kg/m3 (184 lb/cy) of water (4.4 percent).
There is no large aggregate in the mix.
As UHPC can be costly, there is a search to find methods to supplement cost on concrete box-bridges while finding a way to avoid some of the cracking that leads to corrosion. The solution in which this author has been involved uses UHPC in the longitudinal bridge joints with dowel bars—a relatively new idea. After some analysis using finite element models, a box-beam bridge with UHPC in the longitudinal joints in Fayette County, Ohio, was built near Washington Courthouse.
By July 17, 2014, the beams and joints had been cast and set. The structure was monitored with instrumentation right after the joints were cast for approximately a week. Load testing was carried out on August 8 with a team of graduate students. Several loaded dump trucks were positioned on the bridge, as well as moving at various speeds over the bridge.
We know bridges are affected by the daily thermal cycles from day to night. Additionally, instrumentation was left on the bridge and will be monitored during the cooler season of late fall or early spring. The bridge was opened to traffic on August 13. Diagnostics are currently being run on the data obtained from the bridge—while those results are not yet in, the belief is using UHPC in the longitudinal bridge joint has the potential to save money and time on the long-term costs of infrastructure.
There is also potential in using this type of technology to update older bridges. At a recent conference, a few students from Virginia Tech approached this author, discussing their plans to use ultra-high-performance concrete for bridge repair. It seems the use of UHPC in new and creative ways is not far away.
Eric Steinberg, PhD, PE, is a professor in civil engineering at Ohio University. He served as assistant chair from 1997 to 2005 and is a registered engineer in the State of Ohio. A member of the American Concrete Institute (ACI), American Society of Civil Engineers (ASCE), and Precast/Prestressed Concrete Institute (PCI), he is a board member of Ohio’s Research Initiative for Locals, and has served as an expert witness in the field of structural engineering. Steinberg is an active member of PCI’s Student Education and Bridge Committees, and has been faculty advisor for student organizations of ASCE and Structural Engineers Association of Ohio (SEAO). He can be reached via e-mail at steinber@ohio.edu.