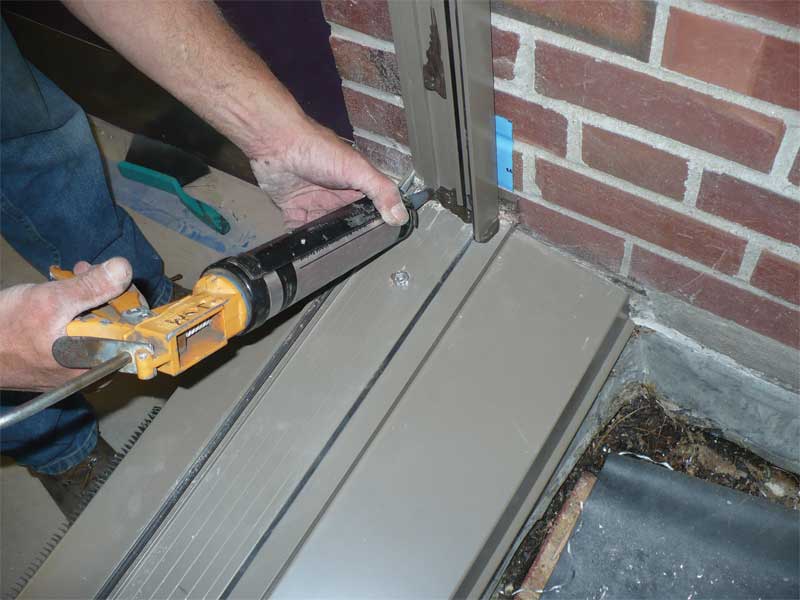
Joint plugs
Joint plugs are rubber or plastic components filling the gap between horizontal and vertical mullions in a curtain wall or storefront system. Not all curtain walls and storefronts have joint plugs, but some of these systems are designed to allow water to move vertically within the vertical mullions and drain out at the bottom of the system. Where joint plugs are used, they are an essential component in the water management capabilities of the higher-performing glazing systems. Omitting joint plugs can seem like a benign offense, but the joint plugs serve three critically important roles.
1. The joint plug helps compartmentalize drainage channels so incidental leakage can be promptly directed back out of the glazing system.
2. Joint plugs stop water from draining onto the tops of insulated glazing units (IGUs) below. Glazing systems that do not include joint plugs in their design deal with this issue with an accessory called a deflector—this allows water at a horizontal mullion to drain down the vertical mullions without tracking back to the top of the IGU below. Water allowed to collect on the seals of IGUs will deteriorate them, causing premature failure or fogging of the glass.
3. Joint plugs help seal the gap between the horizontal and vertical mullions.
Inspecting joint plugs is an important task whether performed in the field or at the fabrication shop. Inspection can be messy as the joint plugs should be covered with sealant at all contact surfaces with the horizontal and vertical mullions, but also built up with sealant along the top of the plug to form a shed to move water toward the weep holes on the horizontal mullion.
Using a dulled dental instrument, the interface of the joint plug with the horizontal mullion can be probed to verify the sealing continuity; one should also see sealant filling the raceway for the pressure bar fasteners and extending 25 mm (1 in.) or more away from the joint plug.
The sloped sealant bed atop the joint plug should not contact the edges of the IGU as this will prevent the free flow of water to the weep holes around the edges of the glass.
Anti-walk blocks
Anti-walk blocks keep a glazing unit from shifting or walking from either side in the glazing pocket. These rubber blocks are slid in at the sides of the glazing pocket next to the glass and they help to prevent glass-to-metal contact, which can cause glass breakage.
We rarely see anti-walk blocks being installed, but these components are nonetheless beneficial in all glazing systems. Anti-walk blocks are essential in glazing systems with unequal glazing pocket depths as may occur in pocket glazed storefront assemblies. We have seen glass move into the deep pocket side of a pocket glazed glazing system (caused by wind vibration) to the point where several IGUs lost their complete bite along one side of the unit. Anti-walk blocks are an inexpensive component of a glazing system that can prevent these costly issues.
Conclusion
Although the shop drawing and submittal phase is intended to serve as a means for establishing a plan for quality control, they cannot depict all of the nuances outlined in this article. Being onsite during the initial installation is truly paramount to the end performance of the glazing system, as it can help to set the stage for workmanship expectations that are not captured in the shop drawings or the manufacturer’s fabrication and installation instructions.
As mentioned, the person preparing the shop drawings is typically not the same person who installs the glazing system—more often than not, pertinent details get overlooked or misinterpreted. An honest mistake or seemingly small oversight can become a costly regret. In addition to the cost of addressing these issues, fixing them can—and often will—have an impact on the schedule and someone’s pocketbook.
Cynthia L. Staats, PE, LEED AP, is senior staff II in Simpson Gumpertz & Heger’s (SGH’s) Building Technology group, where she has worked for 10 years. Staats works on projects involving waterproofing investigation and design of building enclosure systems, including plazas, exterior wall systems, windows, roofing, foundations waterproofing, and stone cleaning. She is a member of the ASTM D18 Committee on Soil and Rock. Staats can be reached via e-mail at cstaats@sgh.com.
Michael J. Louis, PE, is a senior principal with SGH, specializing in the design, construction, and performance of building enclosure systems. He focuses on glass-and-metal fenestration systems, but also has extensive experience with below-grade and terrace waterproofing, exterior walls, and flat, steep, and low-slope roofing. Louis brings a solid understanding of materials, interaction among these materials and with other building systems, and the integration of waterproofing, structural, and energy systems to achieve optimal building performance. He is a member of ASTM C24 Committee on Building Seals and Sealants, American Architectural Manufacturers Association (AAMA), Building Enclosure Council (BEC), and American Society of Civil Engineers (ASCE). Louis can be reached via e-mail at mjlouis@sgh.com.