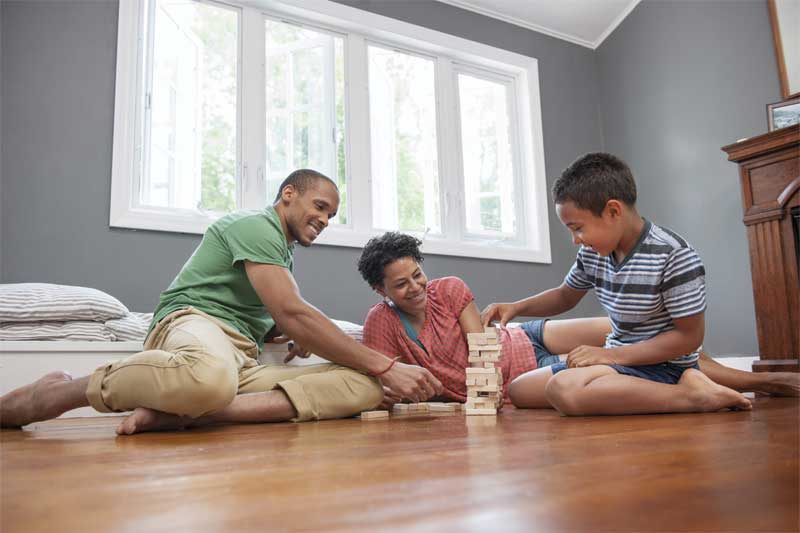
by Thomas D. Skaggs, PhD, PE
Wood is known for its natural ability to improve acoustic performance—to either dampen or expose sound to exacting requirements. In the music industry, wood forms the acoustical body of many instruments, such as pianos, violins, and guitars. Within the building industry, however, wood assemblies act as sound barriers, reducing noise pollution and reverberation. In walls, partitions, and floor-ceiling assemblies, designers and engineers use wood systems to meet acoustical rating requirements.
Floor assemblies used in multifamily and light commercial structures often include lightweight concrete or gypcrete toppings installed over engineered wood floor systems. This approach requires a separate subcontractor to apply the toppings as well as additional time for the toppings to set and also has the potential for topping failure. Such composite floor systems are typically constructed as fire-rated assemblies with code-compliant fire and acoustic performance.
The wood structural panel industry has developed all-wood floor systems that use single- or double-layer floor sheathing, meet both fire and acoustic performance requirements that without the use of concrete or gypcrete topping. This new and efficient approach reduces more than just sound by alleviating the need for additional subcontractors to apply toppings. This in turn reduces overall floor installation time and contributes to predictable performance with consistent, uniform products.
All-wood floor systems that are designed to meet sound transmission requirements employ thick subfloor sheathing, such as a single layer of 1 1⁄8 Performance Category panel or double layers of 19⁄32 Performance Category top layer placed over a 23⁄32 Performance Category base layer. Conventional light-frame floor construction is typically accomplished with a single layer of 23⁄32 Performance Category floor sheathing. In addition to eliminating delays, all-wood floor systems have the advantage of thicker sheathing, which increases the stiffness of the floors when compared to conventional light-frame varieties.
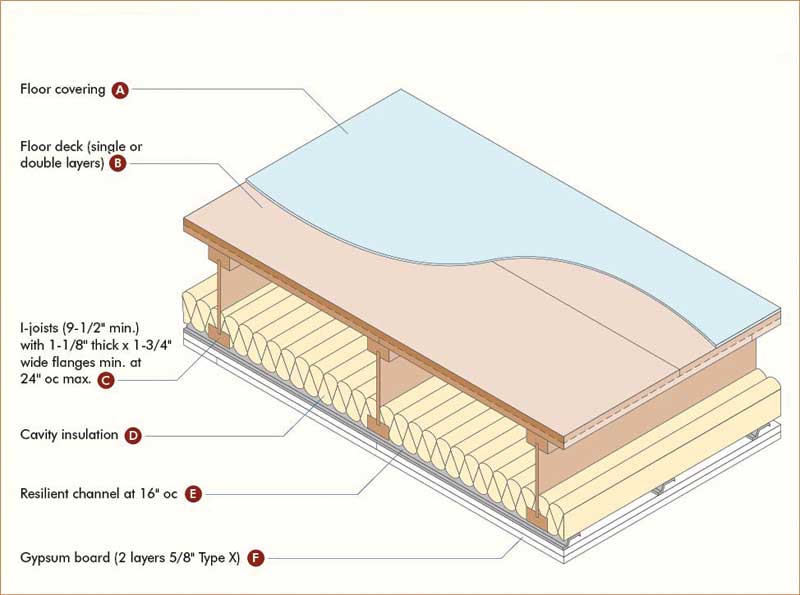
In supporting the development of all-wood floor systems without lightweight gypcrete or concrete topping, APA–The Engineered Wood Association conducted a series of acoustic tests for code compliance based on sound transmission class (STC) and impact insulation class (IIC) ratings. (A detailed description of STC and IIC ratings is provided on the APA website at www.apawood.org/noise-rated-systems.) The tests showed that a double-layer floor assembly (19⁄32 Performance Category top layer over 23⁄32 Performance Category base layer) provides similar acoustic performance to a single-layer (1 1⁄8 Performance Category) floor assembly.
All-wood floor assembly
An all-wood floor assembly (Figure 1) typically has the following components.
Floorcoverings
A variety of floorcovering materials are available. (See Figure 2, for STC and IIC ratings.) In regards to vinyl and quarry tiles, as well as hardwood flooring, a sound mat should be installed between the floorcovering and sheathing. Some floorcovering material options include:
- Cushioned vinyl: Vinyl sheet flooring featuring 3.7 mm (0.145 in.) in minimum thickness and 2.6 kg/m2 (0.53 psf) in minimum weight.
- Vinyl tile: Minimum thickness of 4.8 mm (0.19 in.) and 11 kg/m2 (2.21 psf) minimum weight over a 5-mm (0.198-in.) thick sound mat weighing 3.8 kg/m2 (0.78 psf).
- Quarry tile: Minimum thickness of 12.7 mm (0.5 in.) and 27.3 kg/m2 (5.6 psf) minimum weight attached to a 5-mm thick sound mat weighing 3.8 kg/m2 and using thin-set mortar.
- Hardwood flooring: Minimum thickness of 9.6 mm (0.38 in.) and 5.5 kg/m2 (1.12 psf) in minimum weight over a 5-mm thick sound mat weighing 3.8 kg/m2.
- Carpet and pad: A 1247-g (44-oz) carpet with 11 mm (0.438 in.) in minimum thickness and 2.7 kg/m2 (0.56 psf) in minimum weight over a foam rubber pad of 9.5 mm (0.375 in.) in thickness and 2.3 kg/m2 (0.48 psf) in weight.
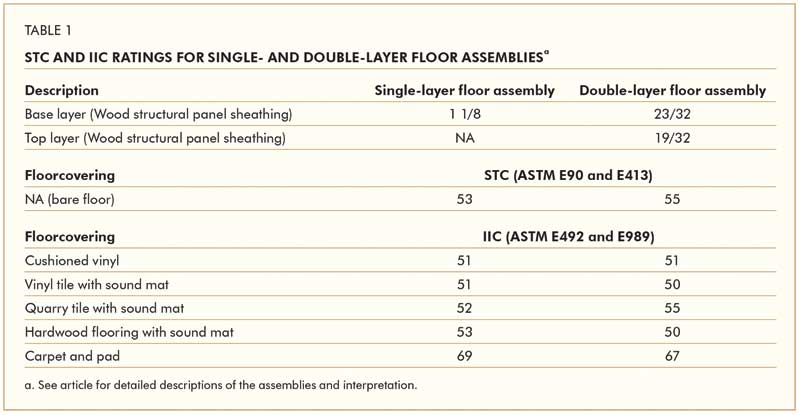
Floor deck
Wood structural panel floor sheathing meeting the code requirements should be installed perpendicular to the I-joist framing. Though it is not required, the designer may glue the floor sheathing to the I-joist framing for structural performance.
For the single-layer floor system, 1 1⁄8 Performance Category tongue-and-groove floor sheathing should be used with fasteners at 152 mm (6 in.) on center (o.c.) or less in the sheathing perimeter and 305 mm (12 in.) o.c. or less in the field.
For the double-layer floor system, the base layer of 23⁄32 Performance Category tongue-and-groove floor sheathing should be used with fasteners at 152 mm o.c. or less in the sheathing perimeter and 305 mm o.c. or less in the field. The face layer of 19⁄32 Performance Category sheathing may be square-edged, and should be laid over the base-layer sheathing (staggered in accordance with APA’s Engineered Wood Construction Guide, Form E30) with fasteners at 152 mm o.c. or less in the sheathing perimeter and 305 mm o.c. or less in the field.