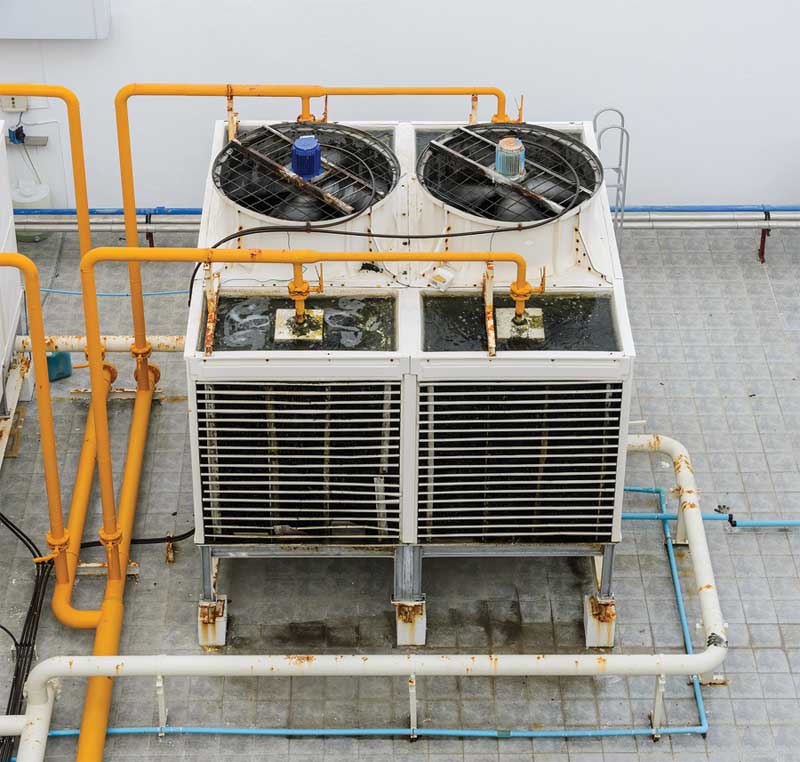
Advantages of PMAC motor
Standard induction motors are not particularly well suited for low-speed operation as their efficiency drops with the reduction in speed. They may also be unable to deliver sufficiently smooth torque across the lower speed range. This is normally overcome by employing a gearbox. Utilizing a PMAC motor with an external drive eliminates the need for a gearbox and saves space and installation costs, since the foundations just need to be prepared for a single piece of machinery. This also gives more freedom in the layout design. (Click here for additional details.)
The PMAC motor can deliver more power from a smaller unit. They are suitable for variable- or constant-torque applications. The drive and application parameters dictate to the motor how much torque to produce at any given speed. This flexibility makes PMACs suitable for variable-speed operation requiring ultra-high motor efficiency.
Currently, PMAC motors cannot be used in washdown places (e.g. food processing plants) or in an application requiring explosion-proof motors. Also, anything requiring more than 6000 revolutions per minute (RPM) will not work with a PMAC motor. Additionally, these motors always require an AC inverter to run, which adds to the cost.
A standard AC induction motor does not require an inverter unless the speed needs changing. For many customers, the technology of a PMAC motor is too new, costs more, and they do not see the payback as quickly as they would like. Also, if it is an original equipment manufacturer (OEM) application, the customer most likely has to recertify the equipment for Underwriters Laboratory (UL), Canadian Standards Association (CSA), or similar agencies.
Higher productivity
Advanced PMAC technology can improve system performance using a radial permanent magnetic design that minimizes any rotor loss, significantly reducing operating temperature and vibration. When a PMAC motor is matched with a variable-frequency drive (VFD), the combination helps optimize mechanical systems to achieve the maximum output and lowest total cost of operation.
PMAC motors provide:
- higher efficiencies achieved across a speed range;
- greater torque capabilities;
- greater power density; and
- more lightness than AC induction motors in a comparison within the same horsepower (HP) range.
PMAC motor speed is limited by back electromotive force (EMF)—voltage opposing the current that causes it—because the latter increases directly with the motor speed. The motor is connected to the electronic drive and its electronic components are designed for a maximum voltage above the rated drive voltage. Normally, the motor and controls are designed to operate well below the maximum voltage of the components. However, if motor speed exceeds the design speed range—either being powered from the control or being driven by the load—it is then possible to exceed the maximum voltage of the drive components and cause failures. VFDs are capable of limiting motor back EMF when operating properly. However, if the drive faults and loses control during speeding, it cannot protect itself.
Conclusion
Industrial brewing chillers are an efficient way of quickly cooling wort as well as maintaining the temperatures in brite and fermentation tanks. The process of heating and cooling the wort is critical to the success of craft beer. It is crucial the chiller operates quickly and efficiently to lower the wort back to the ideal temperature.
Today’s craft breweries are making great strides in reducing their energy consumption and costs, and in implementing the latest technologies and practices for efficiencies. This is achieved through the use of chiller systems equipped with high-efficiency PMAC motors. These motors, in comparison to the AC varieties, significantly reduce operating temperature and vibration, provide higher efficiencies achieved across a wider speed range, and offer greater torque capabilities as well as increased power density.
Cheryl Higgins is product marketing manager with Leeson Electric, a manufacturer of various electric motors, mechanical and electrical motion controls, and power generation products serving markets all around the world. She is responsible for new product development and training, and has more than 35 years of industry experience managing technical and applications teams. Higgins can be reached at cheryl.higgins@leeson.com.