Cement and concrete, still outperforming in the sustainability era
by Michael Stanzel and Natalee Sembrick
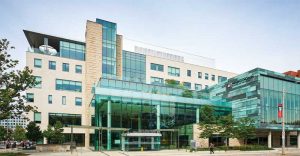
Sustainable design in construction is motivating designers and builders to re-evaluate the materials, methods, and metrics used in creating greener communities. Sustainable structures must balance the environmental footprint, service life, social aspects, and economic factors. As modern society shifts to a circular, carbon-neutral built environment, concrete continues to deliver ‘best-in-class’ performance as a building material.
One of the most important challenges facing the world today is meeting the habitation and food needs of a growing world population, while mitigating climate change. With the construction, operation, and decommissioning of structures and infrastructure accounting for approximately 40 percent of all man-made greenhouse gas (GHG) emissions, it is self-evident construction practices need to change and buildings must become low-carbon and more resilient to the changing climate.
Over the past few years, there has been considerable discussion about concrete construction and its impact on global warming. Concrete is the most widely used manufactured material in the world. Each year, more than 20 billion tonnes of concrete are produced globally. The environmental impact of concrete is due primarily to its widespread utilization as a building material. Concrete is, in the authors’ opinions, a relatively low-impact material, not only due to its durability, long service life, and recyclability, but also because of increasing investments in sustainable manufacturing technologies. It is locally available, and a good material for most applications, such as building foundations and structural or architectural elements, dams and bridges, schools and hospitals, pipe and water treatment facilities, residential homes, curb and sidewalk, pavement, etc.
Importance of life-cycle assessment
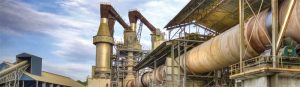
Image courtesy Lehigh Hanson
To build greener communities, a growing number of designers are relying on life-cycle assessments (LCAs) to measure the environmental impacts of construction projects at all stages, from raw material extraction and processing, transportation, and installation to use in service, and, if necessary, disposal.
“Emission Omissions: Carbon accounting gaps in the built environment,” a landmark study by the International Institute for Sustainable Development (IISD) argues LCA is the best approach to measure carbon emissions in buildings, but that more data, transparency, and robust standards are needed (Figure 1). All sources of carbon must be considered to ensure a big picture approach in prioritizing material and energy efficiencies and long service life in designs.
The study identified the omissions of emissions related to concrete, wood, and steel building products. It also identified forestry products as the material with the greatest carbon accounting uncertainties, with up to 72 percent of carbon emissions unaccounted for in current LCAs (Figure 2). When these emissions are included, concrete’s carbon footprint could be up to six percent less intensive than that of wood products, giving designers and policy-makers reason for pause when making decisions about building materials.
P. Purnell, a professor at the University of Leeds, United Kingdom, argues many of the analyses on the embodied carbon of structures are simplistic and do not take into account the utility of each material and the structural purpose of the element. Purnell recommends defining a ‘functional unit’ that allows comparisons of like with like. As an example, a column designed to resist a particular compressive load at a specific height should evaluate the mass of carbon dioxide (CO2) per unit load capacity per unit height. For many structural member dimensions, reinforced concrete provides a competitive carbon footprint compared to other materials.
Studies from the Massachusetts Institute of Technology (MIT) demonstrate the passive energy efficiency of concrete’s thermal mass combined with smart design and the long service life of these structures results in the lowest annual operating costs and global warming potential (GWP). In some cases, particularly with insulated concrete forms (ICFs), the total life cycle GWP can be as much as eight percent lower than alternative designs and materials and could potentially be less than 14 percent with the increased use of low-carbon cementitious products.