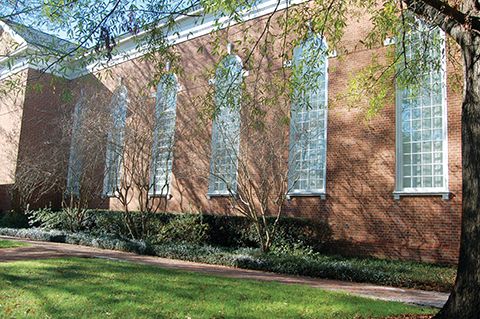
by Laura Ladd
When it comes to historic preservation projects, architects and installers can find themselves at a loss. Wood is the most traditional material, but also notoriously unstable. It has a tendency to warp and becomes vulnerable to rot, decay, and insects. Some replacement products are more durable, but far from historically accurate, such as aluminum-framed windows. However, a growing number of design/construction professionals are discovering a material that allows them to be historically accurate without compromising on durability—acetylated wood.
Though only recently made commercially available, acetylation has been studied for almost a century. A proprietary process modifies wood at its molecular level by increasing the natural compounds already found there—in other words, nothing is added to the material that is not naturally present. The result is a more durable and dimensionally stable solid wood.
More specifically, acetylation targets free hydroxyls, an abundance of chemical groups contained within the wood. Free hydroxyl groups readily absorb and release water according to changes in the climatic conditions to which the wood is exposed, which is the main reason why wood swells and shrinks.
The acetylation process modifies the wood to its core. Therefore, unlike pressure-treated wood, it can be cut or profiled without exposing unprotected surfaces. Further, since acetylation is non-reversible, there is no risk of leaching or loss. Due to these characteristics, acetylated wood is appropriate for a number of exterior applications, including:
- decking;
- cladding;
- windows;
- outdoor furnishings; and
- structural projects, such as bridges.
The technology behind the acetylation process is different for each species; it is currently being used for radiata pine.
Better wood through chemistry
The acetylation process alters the wood’s reaction with water by permanently replacing those free hydroxyls with stable acetyl groups that will not bond with water. With a higher level of acetyl molecules, the shrink/swell cycle is improved by 70 percent or more.
This can make it ideal for manufacturing historically accurate wood replacements, says Brooks Gentleman, owner of Re-View, a window replacement manufacturer.
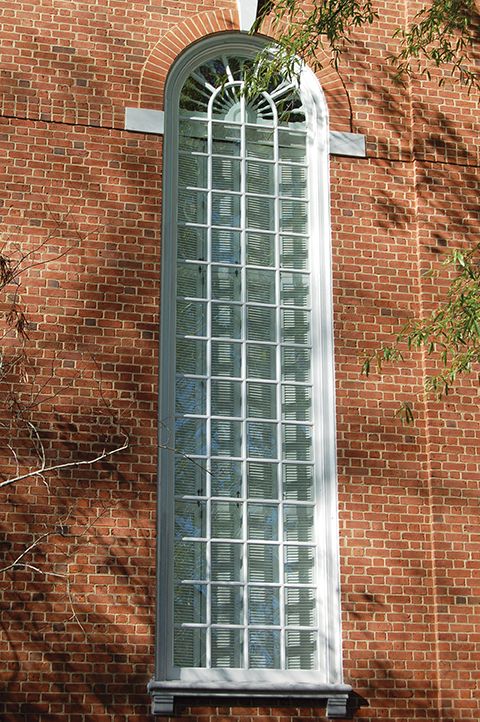
“One thing we really enjoy about acetylated wood is that it’s very dimensionally stable, meaning it doesn’t warp and bend to the changes of humidity,” he explains. “So when we’re manufacturing windows, we don’t have to worry about boards that are bent and warped or unsuitable for use.”
He adds the ‘waste factor’ found with other woods such as mahogany is absent, which saves additional money.
The acetylation process also results in a product unrecognizable to insects, and proven to be an effective barrier to rot and decay. This is particularly important to those who work in climates where termites and other wood-boring pests are a constant threat.
“Termites don’t see it as a food product so you don’t have any additional concerns there,” says Hastings Read, vice president of Oakleigh Custom Woodworks (Mobile, Alabama). “When we specify acetylated wood we know the customer is not going to have any problems. [Also,] you’re not departing from the basic idea and authenticity of the original building. It lets the architect comply with historic standards.”
Acetylated wood acts as an effective barrier against a broad spectrum of fungi, including cellar, wet rot, dry rot, soft rot, white, brown, and pore fungi. It is verified by American Wood Protection Association (AWPA) E 10, Standard Method of Testing Wood Preservatives by Laboratory Soil-block Cultures.
The wood carries a Class C fire rating under ASTM E84, Standard Test Method for Surface Burning Characteristics of Building Materials; it can be treated to meet higher requirements. Fire treatments have been found to bring it to Class A without compromising the material’s attributes after acetylation.