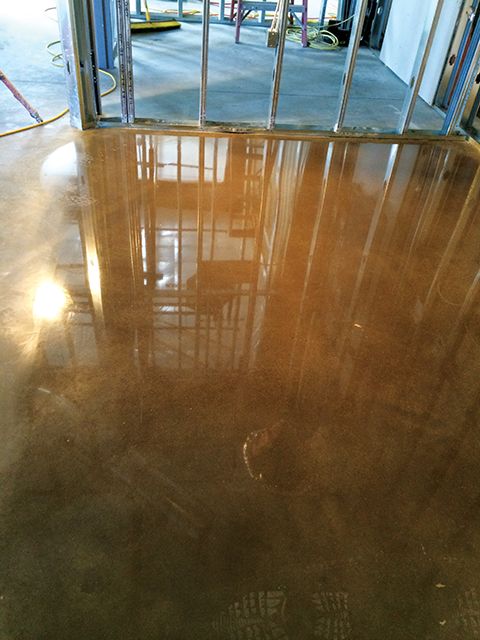
By Andy Bowman
The continued rise in popularity of polished concrete floors, combined with a spate of new ‘polishing’ products, has created a perfect storm for construction specifiers. The industry has responded by releasing a new standard to measure and evaluate these surfaces.
Polished concrete has become a popular flooring choice in contemporary design. It is economical and durable—making it a good fit for warehouse and retail applications. However, economy alone cannot account for the material’s popularity. Polished concrete’s allure stems from its artisanal properties as rustic, yet refined. The combination of earthy material with industrial aesthetic has caused polished concrete floors to appear everywhere from upscale commercial environments to residential design.
The rapid increase in polished concrete installations has made it difficult for scientific methods and standards to keep pace. Today’s concrete polishing industry uses a wide range of systems and equipment, and various specially formulated chemicals and abrasives. This means the specification of a polished floor can result in a myriad of actual finished surfaces.
In particular, many coatings are now being marketed to accomplish the sealing of concrete floors. However, the origin of the gloss and shine has become obscured. In traditional polishing operations, the concrete itself creates the characteristic glossiness and shine. A polished concrete surface is achieved when abrasive tools, with progressively finer grit, have been used to refine the concrete material.
While small-scale pits or imperfections refract light, highly polished concrete reflects it. Ideally, polished concrete should be scratch-free and have a surface texture without abrasion points. Therefore, these properly polished floors would not rely upon a sealant to produce its gloss.
Historically, the gloss meter has been used to provide a quantitative standard for finished concrete surfaces. While this tool records the light reflected from a surface, it does not measure the surface texture. The use of a gloss meter alone to assess a surface can mask its imperfections by measuring the reflection produced by topical concrete polishing sealers that are actually covering flaws and scratches.
With sustainability and lifecycle issues coming increasingly to the fore, the polishing industry would benefit from deemphasizing the mere appearance of glossiness and taking a more holistic approach. To accomplish this, there must be a shift in focus toward performance-based standards and encouragement to use a good concrete mix in the initial pour. When this happens, gloss will become a natural byproduct of the polishing operation.
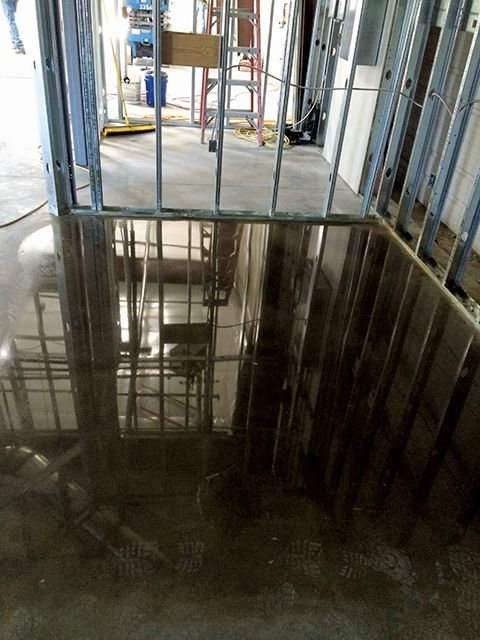
The ideal concrete finishing process ends up being a multidisciplinary activity resulting in tailored properties improving not only the appearance, but also the function and serviceability of a surface. Delivering a high-quality concrete surface will reduce maintenance costs currently borne by end users, as many are currently spending more than expected on maintenance to maintain their floor’s appearance.
Defining a more specific process
Concrete surface refinement involves a series of progressive steps that eliminate scratches and unevenness. Various finishing techniques and tools can mean a high-quality result. Therefore, it makes sense not to prescribe a narrow range of accepted procedures, but rather to adopt a measurement standard that sets a high bar for surface measurement and establishes specific objectives for small-scale refinement qualities.
In the fall of 2013, the Concrete Sawing and Drilling Association (CSDA)—a group representing North American contractors in those industries—adopted a new standard, known as Measuring Concrete Micro Surface Texture (ST115). The association says the document was produced in response to concerns on the part of architects and engineers regarding quality issues with polished concrete.
The standard has two main components. It identifies approved instrumentation for measuring surface texture, and provides a benchmark measurement procedure for contractors and specifiers to follow. It also includes directions for documenting the texture readings and contains a resource section with relevant code information and glossary terms.
I’m going to have to read this a few more times to make sure that I really, truly understand what you were saying here, but I gather that the answer to your leading question is no. I’m not in the construction business at all, but I am looking at getting polished floors, so my question for you is: do polished concrete floors need to be sealed at all? Or does the polishing take care of whatever need sealing fulfills? I want to make sure I hire a company that will use the right process and techniques for my floor, but before I go on I think I’m going to need to understand that. Thanks!
Yes, absolutely! Polished concrete needs to be sealed. It gives additional stain resistance against dirt or liquids. And yes, both floors should be maintained properly. Polished concrete will last longer than a sealed floor.
In trying to find out if sealed and polished concrete were synonymous I followed this link to called “are sealed and polished synonymous”. The meaning of “sealed” is not discussed at all above. Maybe next time ya oughta title your article something that has to do with the content.