After the publication of the article, “Specifying Metal Rainscreen Assemblies,” by Geremy Mendelson, CDT, in the July 2020 issue of The Construction Specifier, we received the following letter.
Dear Editor,
Several members of the Insulated Metal Panel Alliance of the Metal Construction Association (MCA) have expressed concern insulated metal panels (IMPs) are unfairly cast in a negative light in this article. Not only are many such statements absent of context due to lack of important details, but others are just plainly wrong. Following are five such examples:
1. The term “rainscreen” is used quite carelessly by the author without appropriate detail. There are many types of rainscreen systems, both pressure-equalized and non-equalized, and virtually every one of them involves some type of drainage cavity or void. IMPs can be used as either the cladding or the backer depending on where they are located relative to the cavity. These two applications are quite different, and most manufacturers have specialized systems for each one. The author seems to have confused these different applications and simply labeled IMPs as a poor choice without examining the details of any specific system or providing substantiation for the judgment.
2. The article says IMP joinery is “not designed to last more than a couple of years and will eventually fail, causing the entire vapor, air, and water barrier to be left open.” This statement is false. IMPs have been used as both cladding and back-up panels for rainscreen systems successfully for decades in some of the harshest environments. Moreover, if this statement were indeed true, horizontal IMPs would not be able to perform as well as they do as a sealed wall system either.
3. Another statement reads, “There is no waterproofing warranty for insulated panels without additional control layers…” Again, this is simply not true. When IMPs are used as the backer system, the panel is rarely used with any additional control layers. It functions quite well as the last line of defense against liquid water to the wall assembly and is warranted for this application every day.
4.The cost impact of the National Fire Protection Association (NFPA) 285, Standard Fire Test Method for Evaluation of Fire Propagation Characteristics of Exterior Wall Assemblies Containing Combustible Components, testing on IMP versus single-skin cladding is grossly mischaracterized. When discussing IMPs, the article says, “There are NFPA 285-certified panels, but this adds to the cost.” When discussing single-skin [panels], the article says, “The NFPA 285 requirement does not add cost to single-skin panels…” Again, this leads to a false impression in absence of important details. The requirement for NFPA 285 testing is triggered in the International Building Code (IBC) by the presence of a combustible material somewhere in the wall assembly. This is usually foam plastic insulation or a weather-resistive barrier, but any case, the test is required for single-skin cladded assemblies when these materials are present as well. Conversely, it is not required when only non-combustible materials are used, as is the case with mineral wool core IMPs.
5. In reference to IMPs, the article states, “Custom colors or finishes are difficult to get, as the manufacturing process is focused on exceeding minimum volume levels of production.” Again, this is simply not true, as is indicated by the fact that most IMP manufactures also make single-skin panels and the processes they employ to procure pre-painted coil for these products are identical. True, there may be minimum volume requirements for custom colors, but they are no more or less restrictive than for single skin.
In summary, we are of the strong opinion this article is lacking in sufficient detail and analysis to pass any meaningful judgment on the performance of IMPs as a part of a rainscreen assembly. It also makes several statements in absolute terms that we know to be false. Frankly, we are quite concerned that these messages, both the bold and subtle, might pass as guidance to any building professional who happens to read them. We welcome any reader to visit our website for complete and accurate information on IMPs at www.metalconstruction.org/insulated-metal-panels.
Sincerely,
Robert A. Zabcik, PE, LEED AP, technical director, Metal Construction Association Insulated Metal Panel Alliance
For clarification, we reached out to the article’s author. Geremy Mendelson, CDT, offers this response:
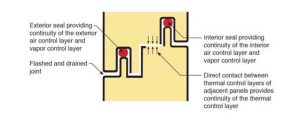
Image courtesy Building Science Corporation
In my role as the president of the Los Angeles chapter of CSI I felt it was incredibly important to be as neutral as possible and to point out the advantages and disadvantages of each product category. My research was done by interviewing people with decades of experience in the manufacturing and installation of these products. Please see the below responses to each point that was made.
1. The rainscreen by definition is a system which is comprised of a number of materials or layers composed in a way to facilitate a back drained ventilated or pressure equalized system.
The article merely points out IMPs alone may not be defined as a ‘rainscreen system’ (as defined by American Architectural Manufacturers Association [AAMA] 508, Voluntary Test Method and Specification for Pressure Equalized Rain Screen Wall Cladding Systems, or AAMA 509, Voluntary Test and Classification Method for Drained and Back Ventilated Rain Screen Wall Cladding Systems). The article does not disqualify IMPs can be, and are used, as a backer or the cladding layer. Great emphasis is exerted on the fact that multiple layers are needed for a true rainscreen system. Below are some scholarly articles that define and measure rainscreen systems as published by various academic and professional institutions:
- the National Research Council Canada’s (NRC’s) studies and subsequent recommendations to designers and professionals in the building and construction industry proposed a formalized cladding system that would not substantially increase neither the cost nor complexities of the construction process. Further, Kirby Garden’s 1963 article in NRC’s Division of Building Research’s Canadian Building Digest, “Rain Penetration and Its Control,” laid out the concepts, methods, and materials involved in the new form of cladding arrangement, and popularized the term “open rainscreen” and the overarching rainscreen principle;
- “Empirical validation and modeling of a naturally ventilated rainscreen façade building,” citation data Energy and Buildings, ISSN: 0378-7788, Vol: 43, Issue: 4, Page: 853-863, publication year 2011;
- “Pressure equalized rainscreen joint modeling with the numerical model PERAM,” citation data Building and Environment, ISSN: 0360-1323, Vol: 30, Issue: 3, Page: 385-389 publication year 1995; and
- “Capturing a Scheme Design for Rainscreen Cladding,” by A. Watson, A. Kalian, A. Gibb, C. Anumba, and E. Agbasi (2007) in Computer Aided Civil and Infrastructure Engineering, 22: 149-161 doi:10.1111/j.1467-8667.2007.00477.x.
2. Building Science Corporation 2015 publication called, “Insulated Metal Panel System,” discusses the importance of the joinery between panels; the interior joint sealant is paramount for compliance with the International Energy Conservation Code (IECC) and the IBC requirements as it relates to water, air vapor, and thermal control (Figure 1).
The article merely points out that these joineries vary by manufacturer and not all are designed or constructed equally. Failure of the sealant within the joint can lead to overall system failure. The writer does not argue the fact that there are reputable manufacturers that have better design than others. However, the generic low bid provider may not be robust enough to withstand the harsh environmental loads. Publication from Pie Consulting and Engineering notes a robust quality assurance (QA) program is required to ensure long term durability of IMPs installed. Most IMP manufacturers do not provide onsite continuous QA programs guaranteeing the critical joint installation by installer. The article is merely noting that without such program and maintenance, IMPs may fail in a few years.
3. The article correctly states that there is no watertight or hygrothermal warranty if IMPs are used standalone. The author agrees. If used as part of a rainscreen or other system with additional layers, there may be a warranty. Even then, the warranty will be from multiple entities with no single source of responsibility. The article emphasizes a single source warranty for the entire system and is critical for the owner to mitigate future risk and headaches.
4. The author agrees with this statement and the article notes that National Fire Protection Association (NFPA) 285, Standard Fire Test Method for Evaluation of Fire Propagation Characteristics of Exterior Wall Assemblies Containing Combustible Components, requirements are not applicable (exempt under IBC chapter 14, 1403.5, “Exceptions”) when all non-combustible materials are used in a rainscreen system/assembly. These non-combustible systems are superior to other systems in that regard (when compared just for that one element).
5. This is not related to IMPs. This statement is a general one for all panels. Nowhere in the article does it say that IMPs are the only product that has difficulty getting custom colors. The main focus of the “custom color” statement is to alert potential specifiers of the consequence of choosing custom color(s). By doing so, there may be a potential volume, price, and time factor they need to consider.