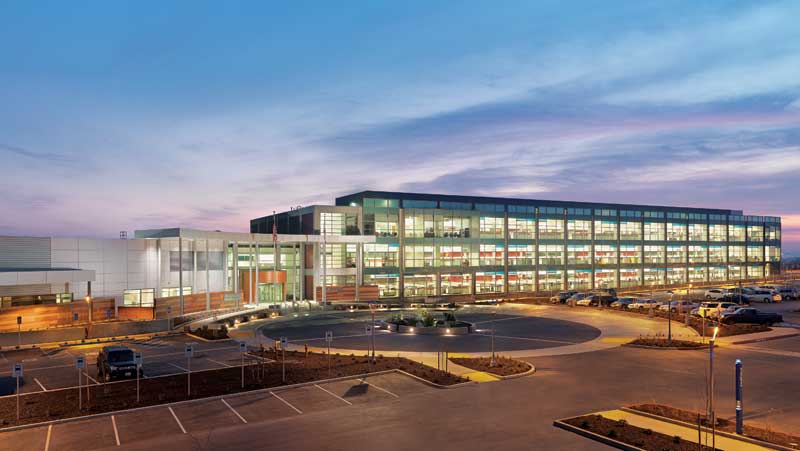
by Brian Miller, PE, LEED AP
Recent code changes, more stringent sustainability requirements, and a challenging economy are some of the factors increasing demand for high-performance structures that integrate and optimize several attributes on a lifecycle basis. This definition carries with it several shifts from ‘business as usual.’
The concept of ‘high-performance’ encompasses sustainability and its related concepts and practices. However, it goes beyond a ‘this-or-that’ approach by requiring optimization of all relevant attributes for a project. Hence, characteristics such as energy and water conservation, safety, security, and durability are no longer just options, but requirements that must be integrated into the overall design, construction, and performance of a structure. (This definition of ‘high-performance buildings’ is paraphrased from the 2007 Energy Independence and Security Act [401 PL 110-140].)
At the same time, ‘high-performance’ also focuses on a structure’s long-term performance, which is a marked change from the first-cost-driven approaches often seen. One vital attribute of long-term performance is ‘resiliency.’ A natural extension of sustainability, it focuses on the structure’s ability to resist natural and man-made disasters such as earthquakes, fires, hurricanes, tornados, floods, and terrorist attacks. It also encompasses how quickly the structure can be back in service after such events occur, and the resources required. Essentially, high-performance structures must be resilient against various forces, and protect occupants and property within.
Once the mindset is shifted to this bigger picture, traditional materials and approaches may need to be rethought. To build high-performance structures, one needs high-performance materials that are versatile, efficient, resilient, and able to meet multiple requirements and challenges. One example is precast concrete, which offers the strength, durability, and fire resistance of concrete, but with additional benefits such as offsite manufacturing, which offers speed of construction, minimal site impact, and a high degree of quality and versatility.

Photo courtesy Brian Erkins, Metromont Corporation
Wall systems
A major component of a high-performance structure is the exterior wall system. Precast concrete wall systems can be categorized into three main groups: solid, thin-shell, and insulated sandwich wall panels (ISWPs). The first two types offer traditional, durable wall systems that can be integrated with other interior wall systems (e.g. steel-stud and cavity walls), while ISWPs offer additional benefits.
ISWPs are made up of two wythes of concrete sandwiching an internal layer of rigid insulation. Inner and outer wall thicknesses vary based on project needs, design requirements, degree of composite action required, or how much the two walls work together to resist loads.
These are face-sealed (rain barrier) systems with the outer wythe serving as the primary defense against bulk rainwater intrusion. It also provides the exterior architectural finish and a continuous air barrier, which is now required in certain climate zones by the 2012 International Energy Conservation Code (IECC). Typically a minimum of 76 mm (3 in.) thick, the outer wythe also acts as a vapor retarder. However, this is usually not a concern since the layer of rigid insulation typically serves as a vapor barrier.
For this inner core, several types of insulation can be used, such as polyisocyanurate (polyiso), expanded polystyrene (EPS), or extruded polystyrene (XPS). Each has different properties and advantages. The thickness of this insulation layer is selected to provide the R-value to meet energy requirements. Usually, the insulation is run edge-to-edge meeting continuous insulation (ci) requirements of both IECC and American Society of Heating, Refrigerating, and Air-conditioning Engineers (ASHRAE) 90.1, Energy Standard for Buildings Except Low-rise Residential Buildings.
The concrete inner wythe often provides the structural capacity, but it can be designed to work compositely with the outer wythe. The two wythes are typically connected by composite material ties, which eliminate thermal bridging. The degree of composite action between the wythes, determined by the structural designer, is controlled by the type and frequency of the connectors. Precast fabricators can assist in the design of these wall systems and help ascertain which is most appropriate for the project.
When an ISWP’s interior wythe is used as the exposed interior wall surface, it provides a durable surface and saves the need for additional materials such as drywall, interior furring, and wall compound (along with the trades and labor to install them). Precast concrete also helps improve the overall indoor environment, as it neither contains volatile organic compounds (VOCs) nor offers a food source for mold or mildew.
Specifying ISWPs also maximizes the thermal mass effect, which essentially provides an increased effective R-value, reducing heating and cooling loads. The thermal mass effect also helps maintain a uniform temperature (improving occupant comfort), and often shifts peak energy demand to times when energy costs are lower. This can help reduce HVAC equipment’s required capacity (i.e. size), improve energy efficiency, and lower operational costs since less energy will be required to heat and cool the structure.