FAILURES
Deborah Slaton, David S. Patterson, AIA, and Jeffrey Sutterlin, PE
This function becomes more complicated when considering wind-driven rain and the project-specific variations of magnitude, intensity, and duration of rainfall and wind speed. Since the directionality of wind-driven rain can change throughout a single storm, it is not always obvious what combination of environmental factors are contributing to water leakage in a building enclosure assembly.
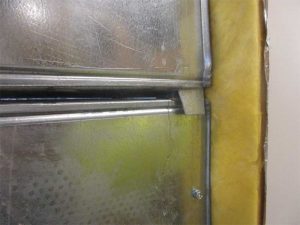
One of the design strategies for resisting rainwater penetration is a drainage approach, such as a rainscreen or cavity wall system, which relies on the outer surface of the enclosure assembly to deflect rainwater, coupled with a dedicated internal drainage plane to redirect water that bypasses the outer surface back to the building exterior. This strategy is commonly understood and implemented in exterior wall assemblies, but it is also important to consider components of mechanical systems that are part of the assembly, particularly when potential exists for rainwater to flow into them. If overlooked, the overall performance of the enclosure may be compromised.
For example, the top floor of a 30-story residential tower located in the southeastern United States incorporated a mechanical penthouse housing HVAC equipment. Storm-resistant louvers were installed in the exterior wall assembly on three elevations of the penthouse to provide ducted intake air for the mechanical equipment. As the louvers were larger than the ductwork to satisfy the desired building aesthetic, metal blank-off panels were installed on the interior of the un-ducted portions of louvers.
Although the blank-off panel assembly included a sheet metal collar fabricated with a sloped bottom (presumably intended to direct water into the weeped sill of the louver), the collar was positioned below the upper edge of the louver sill, creating a trough where water that bypassed the louver during wind-driven rain events would collect rather than draining to the building exterior. In addition, compressible open-cell foam gaskets were installed at blank-off panel joints and along the interface between the blank-off collar and louver frame. However, the foam gaskets did not achieve a continuous seal along these joints, resulting in several gaps. The use of open-cell foam gasketing with gaps suggests these gaskets were installed to reduce air flow through joints rather than to resist water penetration, perhaps indicating overreliance on the “storm resistant” designation of the louvers to mitigate water penetration.
Approximately 18 months after construction, a high-wind event with intermittent periods of heavy rain resulted in flooding of the mechanical penthouse and significant water damage at the four floors immediately below the penthouse. Upon investigation, it was determined the flooding at the mechanical penthouse was caused by the lack of watertight perimeter seals between the louver frame and blank-off panel collar, and between joints in the blank-off panels where wind-driven rain was allowed to penetrate.
Water collecting at the base of the blank-off panel also flowed into the interstitial wall cavity of the exterior enclosure, where it traveled down to the floors below. To correct this issue, the blank-off panels were modified to incorporate functional drainage provisions to redirect water bypassing the louvers back into the sill of the louver, and then to the building exterior. As well, all internal and perimeter joints in the blank-off panel assembly were sealed to prevent water penetration.
Deborah Slaton is an architectural conservator and principal with Wiss, Janney, Elstner Associates (WJE) in Northbrook, Illinois, specializing in historic preservation and materials conservation. She can be reached at dslaton@wje.com.
David S. Patterson, AIA, is an architect and senior principal with WJE’s office in Princeton, New Jersey. He specializes in investigation and repair of the building envelope. He can be reached at dpatterson@wje.com.
Jeffrey Sutterlin, PE, is an architectural engineer and associate principal with the Princeton office of WJE, specializing in investigation and repair of the building envelope. He can be reached at jsutterlin@wje.com.
The opinions expressed in Failures are based on the authors’ experiences and do not necessarily reflect that of The Construction Specifier or CSI.