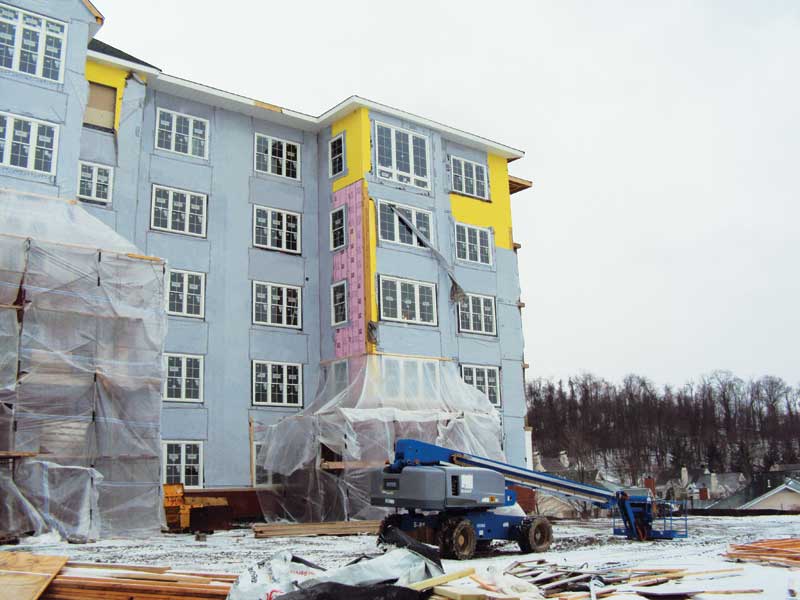
By Herbert Slone, RA, and Art Fox
Today’s high-performance building market is driven by increasingly stringent energy codes and a growing demand for greater building efficiency, sustainability, and affordability—meaning specifying and building masonry cavity walls and adhered masonry walls with materials that work together as a functioning system is more critical than ever. When designing a highly functional masonry wall, the list of wall system performance criteria an architect must consider is daunting.
The wall must provide thermal efficiency, often with several types of insulation. It must also offer air resistance while managing moisture with properly designed and placed water-resistive barriers (WRB). The assembly must resist water leakage, but when water does get in it must be able to drain out of the cavity or from behind the adhered masonry veneer.
Due to their porous nature, masonry cavity walls are ‘rainscreen walls,’ and are expected to allow water into the cavity—therefore, they must be designed to allow drainage and drying. Modern building science has shown high-quality adhered masonry walls such as stucco, stone, and thin brick must also include drainage. The wall must resist vapor permeation, but when vapor penetrates it must be able to dry, even when wetting and drying conflict with each other.
Structural connections must securely hold the entire system together, and at least three different modes of fire resistance should be considered for wall systems, with multiple product warranties managed with these modes of fire resistance. Architects must provide the contractor with a complete list of material and system specifications to ensure the project can be bid accurately.
Contractors need to be able to build with familiar, proven methods and materials that are readily available. They must have complete installation knowledge of every component, and when the project is complete they must provide job closeout information such as LEED and warranty documents.
Sometimes, the architect specifies everything the ‘right’ way, and the contractor installs the components the ‘right’ way, but problems still wreak havoc with the finished building. This is not because the building materials were poor quality or the contractor was incompetent, but simply because some products just do not work together. For example, if a thermoplastic polyolefin (TPO) flashing membrane is sealed with a polyether sealant—both of which are tried and true high-performance materials—the seal will almost immediately fail. For the contractor to provide the best quality construction, the architect must specify materials tested and verified to be fully compatible and ensure plans are accurately detailed.
Architects can speed the design process, reduce risk, and help the contractor produce the best possible building by using complete wall assemblies consisting of components designed and documented to work together as a code-compliant system, with complete compatibility, and which come with sequencing instructions making it clear how each component should be installed.
What is a complete wall system?
A complete wall system has five functional layers. Two of the layers are the wall boundaries, which are the structural backup such as steel or wood studs and sheathing or concrete masonry units (CMU), and a weather-resistant cladding such
as masonry on the exterior. Between these two boundaries are three functional layers containing all of the wall’s core components. Additionally,
a truly complete system provides the testing and documentation showing all the components performing as a system.
The three functional layers are:
- thermal efficiency;
- air/water management; and
- structural connections.
They comprise components that provide all of the necessary performance attributes for a high quality, sustainable wall. In stud walls, the thermal efficiency components include stud cavity insulation, continuous insulation (ci), and a vapor retarder if needed. In CMU walls, the block cells may be insulated. Insulation may also be installed on the interior or the designer may rely on ci on the exterior of the block to meet requirements.
Air/water management encompasses multiple drainage planes, including air and WRBs in both cavity and adhered masonry walls, plus through-wall flashing in cavity walls. Sealing against air and water intrusion also requires the specification of mechanical fasteners with sealing washers. In cavity walls, weep vents and mortar droppings protection must be included. In adhered masonry walls, a drainage plane and weep screed must be specified, all without missing a detail.
Structural connections must be accomplished with single-barrel masonry anchors and sealing washers to properly transfer loads while minimizing and sealing necessary penetrations. Mineral wool safing insulation may also be required for fire protection.
It’s good to see masonry making a comeback in the residential construction scene. Although the use of lumber will never really disappear, I think that the demand will change. I will have to do some more research on insulations for concrete and masonry buildings.
Great explanation here of masonry wall systems and their benefits. It’s nice to know how one should be handling a job like that.