
by Ron Goodman, MBA
When replacing a roof, it has generally been good practice to tear off the existing assembly and replace it with new material. However, this is beginning to change. Simply getting rid of an older roof may not be the best choice for the building owner or the environment.
Sustainability is fueling the desire of building owners to decrease resource consumption and reduce landfill use. The advent of several forensic diagnostic tools is consistent with the trend of minimizing waste and extending the life of existing materials. Now, more than ever, building owners have multiple options to consider when roof systems need repairing.
To determine the best option for replacing an aged roof, the following technologies are useful:
- infrared and nuclear moisture scans;
- moisture meters;
- fastener pull-out equipment;
- insulation density tests; and
- Global Positioning System (GPS) tools.
When these are used in conjunction with thorough energy analyses and lifecycle costing, the best replacement approach becomes clear. With these technologies, building owners can make informed decisions based on both logic and economics.
These testing methods and technologies could not have come at a better time. Over the past 50 years, ethylene propylene diene monomer (EPDM) single-ply roofs have considerably grown in market share. As a result, there are now many aging EPDM assemblies throughout the United States, and owners will be faced with the task of finding cost-effective, durable solutions to keep them in proper working order without tearing off the existing roofs.
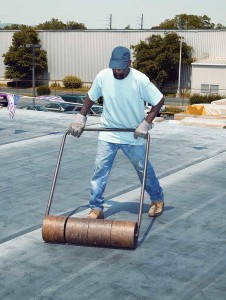
Several factors come into play when deciding how to address an EPDM roof at the end of its useful life. These include:
- thermal bridging;
- proper drainage;
- R-value;
- surface color;
- wind uplift; and
- hail resistance.
Other than complete removal or replacement, owners are faced with two primary options: restoration or re-covering.
The former usually encompasses reworking the flashings, seams, and terminations, while leaving the field membrane in place. EPDM is well-known for its long-term weatherability, so in most cases, the field membrane still has life left. This option is primarily used when the owner wants to extend the existing roof’s life or warranty coverage for an additional five to 10 years.
Re-covering the EPDM roof provides the ability to address more issues than a typical restoration. Proper drainage, thermal bridging, enhanced R-value, altered surface color, improved wind uplift, and better hail resistance are all issues better addressed with a roof re-cover. This option typically offers more performance than a roof restoration; in many instances, it can be warranted for terms up to 20 years.