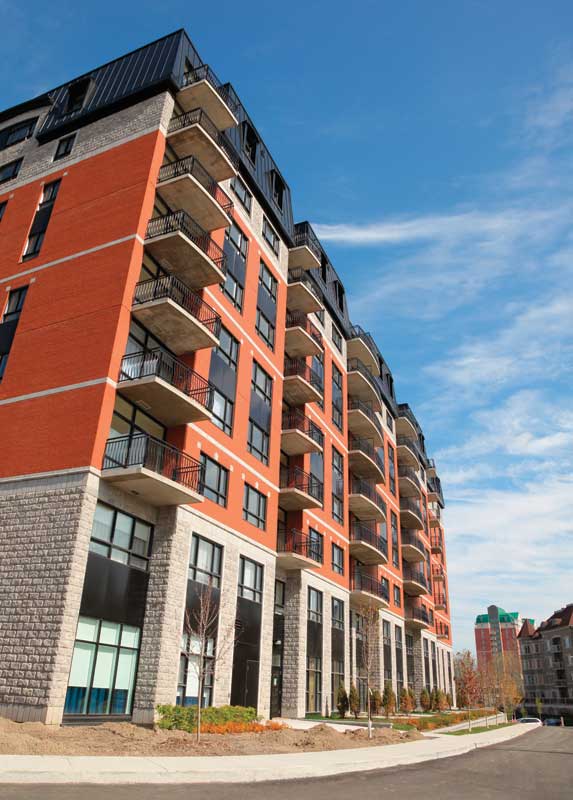
by Jeff Diqui, Arch. Eng., CSI
Failures of claddings like adhered masonry veneer–also known as manufactured stone–often stem from poor flashings, misapplied air and water-resistive barriers (WRBs), and limited drainage. Resulting problems related to moisture intrusion into the wall assembly’s dry zone are moist wall interiors, wet insulation, and rot in sheathing and framing.
Experience has shown detailing flaws in cast-stone veneer causes leaks which can lead to severe damage inside the wall. Rain and wind are often the culprits. A related effect in adhered masonry veneer cladding is inward vapor drive, which can occur in warm weather. It forces moisture stored in the masonry through vapor-permeable housewraps and building papers and into the sheathing and stud bay. This can lead to condensation and water accumulation within walls, as well as wood decay and condensation on interior surfaces. (For more information, see “Adhered Veneers and Inward Vapor Drives,” in the summer 2009 edition of Journal of Building Enclosure Design by John Straube, P.Eng., PhD, et al.)
Some have assumed WRBs between claddings and sheathing layers prevent moisture damage. Research and field experience demonstrate the WRB alone may not always suffice. (See “Improving Drainage and Drying Features in Certain Conditions: Rain Screen Designs for Absorptive Claddings,” in the December 2008 report by National Association of Home Builders [NAHB].) Common practices, such as using double layers of housewraps or asphalt-impregnated papers behind the absorptive claddings, are shown to be ineffective under some climate and weather conditions, particularly if poorly constructed details allow excess water into walls.
Moisture infiltration and damage should be avoided; design detailing can prevent water entry into walls. Additional protection behind absorptive claddings is afforded with three integrated components: a drainage plane, a properly located and continuous air barrier and WRB, and an air gap or space created by a drainage medium, such as filament nylon mesh. Some of these solutions are cavity-wall systems, engineered by a single manufacturer, while others are built-up assemblies consisting of several components.
Applied with fundamentally sound design details, these three elements provide an enhanced drainage-and-drying assembly that improves enclosure performance. Recent code changes—including the 2012 International Building Code (IBC) and International Energy Conservation Code (IECC), which include requirements for WRBs, air barriers, continuous insulation (ci), and drainage—reflect the effectiveness of this approach in mitigating moisture damage.
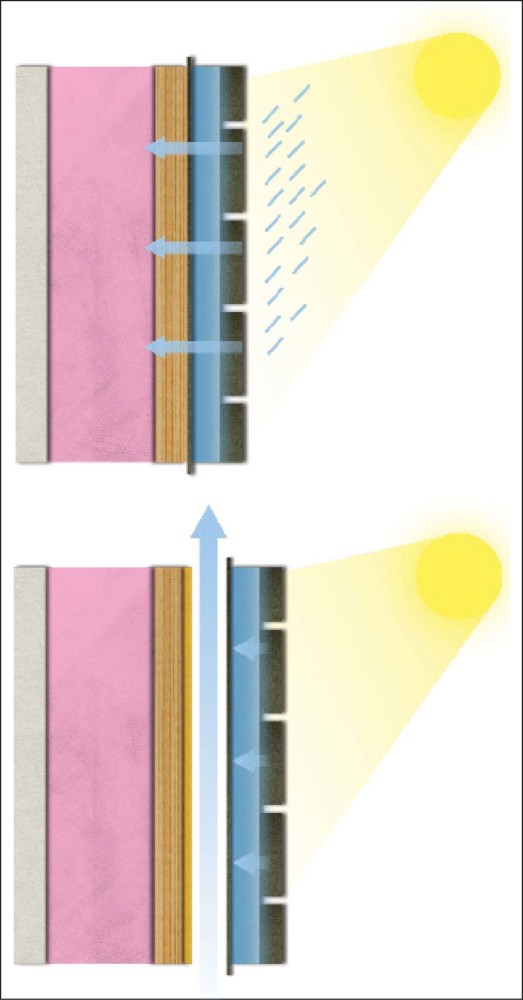
What is not working?
Conventional walls using absorptive claddings for residential and light commercial buildings have typically employed a concealed barrier approach to water management. (See “Improving Drainage and Drying Features in Certain Conditions: Rain Screen Designs for Absorptive Claddings,” in the December 2008 report by National Association of Home Builders [NAHB].) Any water penetrating the adhered masonry veneer cladding encounters the WRB—usually felt, building paper, or housewrap—intended to stop the migration of bulk water. This common assembly may not always be sufficient for adhered masonry and thin brick veneer.
These claddings tend to absorb water through their molded facing units, mortars, and scratch coats. Moreover, according to experts such as John Straube, P.Eng., PhD, they have low outward drying potential as compared to other cladding types, and tend to dry slower. The absorptive elements are typically applied as the outermost wall materials, so they are likely to encounter wind-driven rain, airborne moisture, and even lawn sprinkler spray.
Behind the façade, the cementitious facing materials are typically in direct contact with the WRB that is intended to stop bulk water intrusion, moving any water to flashings or weep screeds. Water sometimes remains in places where the cladding is in contact with the barrier (see “Improving Drainage and Drying Features in Certain Conditions: Rain Screen Designs for Absorptive Claddings,” in the December 2008 report by National Association of Home Builders [NAHB]); under some conditions, those locations may remain wet for long periods. (For more information, see “Adhered Veneers and Inward Vapor Drives,” in the summer 2009 edition of Journal of Building Enclosure Design by John Straube, P.Eng., PhD, et al.)
Various methods have been used to improve this simple assembly type. Some housewraps and WRBs have been reformulated to provide enhanced protection. Furring strips can be employed between the two WRB layers as a rainscreen. Other drainage spacers—including dimple sheets and drainage mats—have been shown to enhance drainage and drying within the wall. (See “Water-managed Wall Systems” in a 2007 issue of The Journal of Light Construction by Joseph Lstiburek, M.Eng., PhD, P.Eng.)
Yet, bulk water intrusion is not the only enemy; another challenge is inward water vapor drive. Since many WRBs are highly vapor-permeable, the moisture stored within the masonry veneer or mortars can be driven by the sun, directly heated through WRBs, and into the sheathing and stud bays behind (even in cold climates).
Bulk water intrusion and vapor drive have led to damage and rot in sheathing and structural members, both in wood- and steel-framed structures. (For more, see the report, “Development of a Rainscreen System for Adhered Manufactured Stone,” by Robert Rymell, P.Eng., C.Eng., from the 2007 Canadian Building Science and Technology Conference, hosted by the Alberta Building Envelope Council [ABEC] South.) Some WRBs deteriorate over time or moisture can get in through errant fastener penetrations that miss studs, or both.