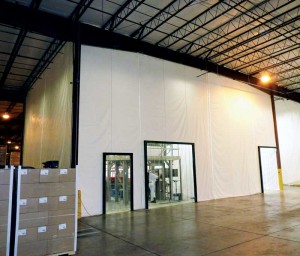
by Jon Schumacher
Similar to most industrial sectors, regulatory requirements in both pharmaceutical and food manufacturing have become more stringent than ever. In response, the equipment and processes used in these industries have also become more sophisticated. A prime example of this can be seen in the ongoing improvements in door and wall products used in clean room and wash-down applications.
In both the pharmaceutical and food industries, clean rooms are essential for ensuring contamination control. Moreover, clean room planning has evolved into its own specific area of industrial design. Keeping airborne contaminants generated by people, process, facilities, and equipment from suspending in the environment is a primary concern for these designers. However, clean room designers have increasingly come to realize one of the best ways to minimize contamination is to prevent contaminants from entering the room in the first place—hence, the growing interest in clean room doors and walls.
As their name suggests, clean rooms create environments that maintain an extremely low level
of environmental pollutants such as dust, airborne microbes, aerosol particles, and chemical vapors. More accurately, a clean room has a controlled level of contamination specified by the number of particles per cubic meter at a specified particle size.
To give perspective, the ambient outside air in a typical city contains 35 million particles per cubic meter in the range of 0.5 μm and larger in diameter, corresponding to a rating of ‘9’ under International Organization for Standardization (ISO) 14644-1, Cleanrooms and Associated Controlled Environments, while an ISO ‘1’ clean room allows no particles in that size range and only 12 particles per cubic meter of 0.3 μm and smaller. (As a point of reference, human hair is about 75 μm across, depending on the person.)
In the pharmaceutical industry—where clean room requirements of ISO ‘6’ to ‘8’ are common—clean rooms play a crucial role in the manufacturing of products required to be free from microbial and particulate contamination and be protected from moisture. Although regulations are not quite as stringent in the food industry—with respect to the particulates range—clean rooms, clean areas, and wash-down walls are equally important in the prevention of contamination.
In both industries, doors and walls play an essential role in clean room operations. Today’s high-performance fabric doors fit virtually anywhere and are uniquely designed to address the need for environmental control, productivity, safety, and cleanliness. They are used not only to prevent cross-contamination, but also to aid in maintaining correct room pressures and air circulation rates, and helping to ensure optimal operating efficiency. While anti-microbial walls have always been important in segmenting environments with differing levels of clean requirements (or clean/non-clean environments) there is a growing use of flexible, industrial ‘curtain walls’ for applications subject to wash-down protocols. Not only are they quicker, easier, and less expensive to install than traditional construction, but they can also be moved or reconfigured if changes in the process or floor plan occur later.
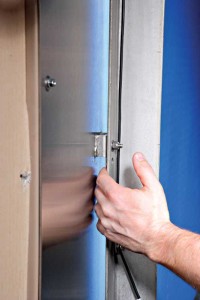
The role of doors
High-performance doors and flexible fabric curtain walls have evolved in recent years and are a viable option for various food and pharmaceutical applications.
The primary function of most industrial doors is to provide tight environmental separation, yet allow occupants and equipment to quickly and safely move from one area to another. For pharmaceutical manufacturing, doors take on an even larger role by allowing companies to achieve and maintain a specified level of cleanliness for a given clean room. High-speed fabric roll-up doors (also called upward-acting doors) are commonly used in clean rooms. They are also an integral part of airlocks that form buffers between different classes of clean areas.
The goal in virtually all clean rooms is to maintain an air pressure differential between rooms, pushing air from the opening’s cleaner side to the less clean side. Occasionally, the goal is to keep particulates within a certain room to avoid cross-contamination with the processes in adjoining rooms. For these reasons, most facilities incorporate multiple pressure steps within the building’s structure. The steps typically range from 5 to 13 Pa (0.02 to 0.05 w.g.) between rooms, but can be as high as 50 Pa (0.2 w.g.).
A door capable of at least 0.2 w.g. in pressure differential is needed to maintain a tight seal and minimize air leakage. Given the need to maintain pressure differentials, doors that seal tightly and cycle quickly are essential in pharmaceutical manufacturing. A properly designed door helps ensure the facility’s makeup fans can satisfy the required amount of makeup air needed to maintain pressure. Another prerequisite in overall door design is cleanliness, since doors must operate in
a pristine manufacturing environment. Any high-speed door used in pharmaceutical manufacturing must also balance the need for productivity with operational safety.