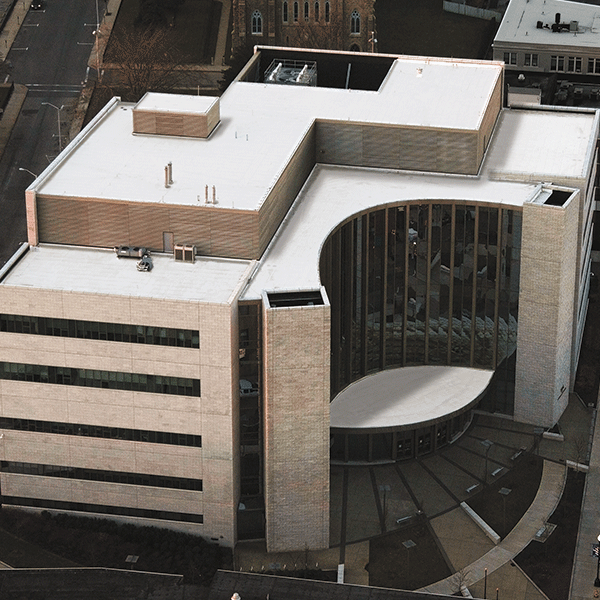
Photo courtesy GAF
by Lee Martucci
Building owners, commercial roof specifiers, architects, and contractors have some decisions to make when it comes to the material they should use to repair or replace a low-slope roof. Three popular choices include:
- coating over the existing roof;
- thermoplastic polyolefin (TPO) recover (putting a layer of TPO over the existing membrane); or
- TPO replacement (tearing off the existing membrane and installing a new TPO membrane).
Whether one is using a coating or a TPO solution, it is integral the roof is sound and no moisture is trapped within the assembly. It is important to determine which option will be most effective for the property, and the present and future needs of the building. Further, the underlying roof needs to be dry; it cannot have residual moisture.
TPO has been specified as a roofing solution for more than 20 years. Its benefits can include:
- highly reflective surface;
- good performance in ponding situations;
- resistance to mold, dirt, and punctures;
- durability; and
- ease of installation.
Coatings are also a viable option as they:
- have a highly reflective surface;
- are easy to install;
- require no tear-off;
- are typically considered a maintenance item and can be written off as an expense in the first year; and
- are monolithic and seamless.
There are many factors to consider when deciding between a TPO roof or a roof coating for low-slope commercial building spaces. Both have their own advantages and disadvantages; generally, neither is better than the other. However, before making this important decision, one must consider the many factors surrounding roofing specification.
Budget
Every commercial project has a planned cost estimate, so it is important to consider budget when deciding which material to specify. However, one should consider future expenditures as well as the present budget. If cost is a major factor, TPO and coatings have some overlap on price depending on the system, material, and thickness option. These roofing options may be treated differently for tax purposes. One should consult a tax advisor to determine which system is more beneficial from a tax perspective.
TPO is considered a long-term investment with its extensive warranty. Therefore, it is important to look at the potential future savings. Even if the initial installation price is high, it may be worth paying more upfront for the right system and not worrying about the roof, since it is guaranteed to last more than 20 years.
Time of year
When a roof repair is needed, it cannot be delayed too long. TPO induction welding or mechanically attached TPO can be installed in colder temperatures. Fully adhered temperature limits are 4 C (40 F) and up. Most coatings must be installed at 10 C (50 F) and above. Since water-based coatings can freeze, it is important to ensure the temperature does not drop below a certain point before the coating fully cures (typically in 24 hours).
TPO can also be installed in hot weather. Most coatings require the roof surface to be 48 C (120 F) or less so the coating does not blister, which can easily occur on a hot summer day—especially with a dark roof.
Wind and rain
Weather is a large factor when dealing with roof repair—wind and rain can be an enemy to a roof repair job. If it is windy, TPO has an advantage over coatings because the spray application can be challenging to use on gusty days.
Additionally, a coating must have time to cure and become rain-resistant. Most acrylics take approximately 24 hours to cure, but there are other coatings, such as silicone and solvent-based, that will cure faster and are more resistant to an early rain.
Rain is not as big a problem for a TPO installation. With many TPO systems, workers can continue until just before the storm starts and resume when the weather improves—allowing for greater flexibility on the project and with the contractor’s time. Regardless of the system, contractors should always follow best practices by checking the weather forecast and planning appropriately.
Ponding water resistance
Potentially a big problem on commercial roofs, ponding is often not covered in the warranty. The ponded water serves as a breeding ground for fungus, mold, and algae, the buildup of which can more readily break down a soft, water-based coating like an acrylic than a substance like TPO, which has heat-welded seams. Most acrylic coatings are not recommended in ponding situations due to a relatively high absorption rate. Silicone and polyurethane are better in these applications due to their low absorption rates. Regardless of the system, proper drainage is key to minimizing ponding water and designing a lasting roof.