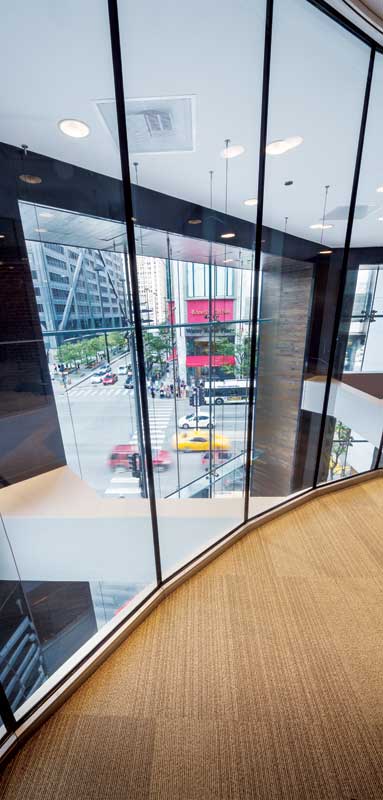
by Lindsay Hampton
Modern architectural designs favor open spaces and natural light throughout large buildings. Now, even enclosed interior areas like offices, corridors, and stairwells are using interior glass to open up otherwise windowless spaces. This requires fire-protective glazing that offers not only life safety, but also visual and color clarity.
Architects have relied on glass ceramics as a fire-protective window glazing for more than 30 years. Originally, glass ceramics were used as cooktop surfaces because they have no thermal expansion. In other words, they do not experience thermal stress when heated locally and will not break. Untempered non-ceramic glass products will crack when heated, creating an opening through which smoke and flames can pass. When used as part of a fire-rated window assembly, glass ceramics can effectively prevent fire and smoke from moving between rooms for 20 to 180 minutes, depending on the application and code requirements.
If cold water is spilled on the hot surface of a glass ceramic cooktop it will not shatter as normal glass would. Likewise, falling raindrops or cold water from a fire hose will not crack or shatter the glazing of a fire-heated glass ceramic window. This unique property makes glass ceramics a safe choice for compartmentalizing building sections designated by local code officials as requiring hose stream tested ‘fire-protective’ openings or windows.
Glass ceramics, like other fire-protective building materials, do not prevent the penetration of radiant heat. Some codes prohibit glass ceramic use where ‘fire-resistive’ partitions and walls—which block heat as well as smoke and fire—are required. Additionally, codes typically restrict ‘fire-protective’ glazing materials’ area to 25 percent of a wall.
Still, according to a number of experts and authorities having jurisdiction (AHJs), fire-rated glass ceramics meet or exceed building codes and life-safety requirements for fire protection. Additionally, these products allow the opening of fire separations and exterior walls, permitting natural daylight to penetrate further into a building’s interior. Exposure to natural light has been shown to have significant health and performance benefits for occupants, and its presence can greatly reduce the need for electric lighting—an advantage for building owners who aim to meet energy efficiency or utility cost goals.
Even with its fire- and life-safety performance, glass ceramic glazings have a tradeoff. The glass is traditionally amber-colored cast and has higher levels of distortion and haze compared to float glass. However, over the last decade, the various manufacturers of glass ceramics have incrementally improved the transparency of the once-heavily tinted fire-rated products. The natural, but unwanted color is now nearly invisible except when placed against a stark white surface or paired with the more transparent float glass, which has a slight greenish tint. Even so, some architects and building owners worry the yellow-hued panes might appear discolored when compared with nearby windows or doors containing more transparent glass.
The yellow earth-tone tint feared by architects and owners is a byproduct of the manufacturing process. During the production of glass ceramics, components of the glass partly crystallize and leave fine-grain pieces embedded in the matrix. When these beneficial crystals are heated they contract in proportion to the scope and volume of the expansion of the heated glass. These two actions within the matrix negate each other, so there is no thermal expansion or cracking.
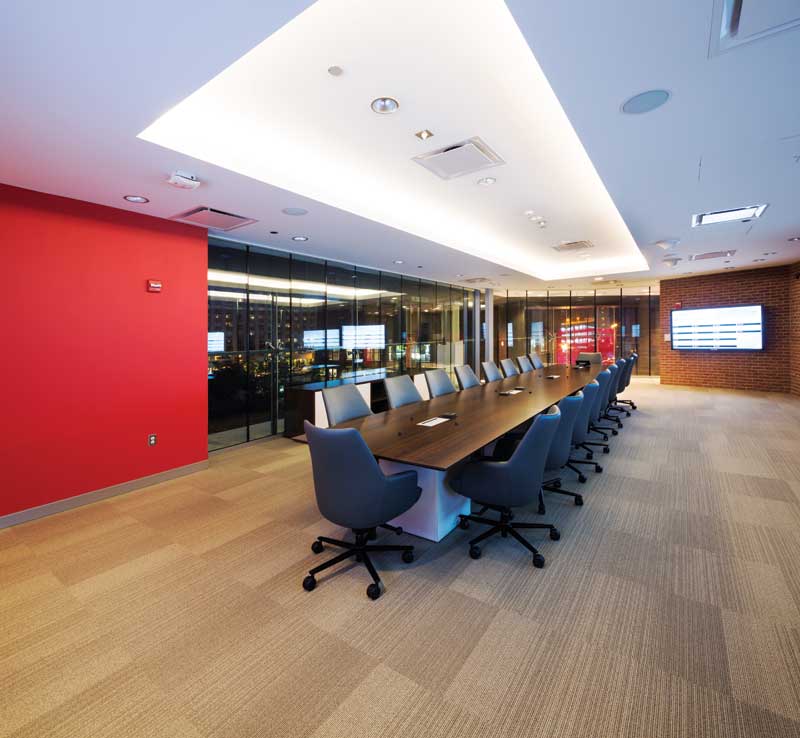
Color rendering
The inherent chemical composition of the glass matrix results in a final product with a slight amber hue, which can distort the colored appearance of objects on the opposing side of the glass. Generally, the darker or more colored the glass tint, the greater the deviation from the actual color of objects viewed through the glass.
However, manufacturers have recently introduced fire-rated glazings with substantially improved color rendering, reflectivity, and clarity, along with less distortion, greater ultraviolet (UV) absorption, and better light transmission. Through various technologies, manufacturers have produced glass-ceramic glazings that measure 85 to 97.1 out of 100 on the color rendering index (CRI). This scale determines how ‘true’ a color appears when viewed through the glass. The color of an object viewed in natural daylight without any glass between the eye and the object would rate 100.
These high ratings for color clarity would have been unheard of a decade ago when manufacturers began their quest to improve the transparency of glass ceramics. Many of these products can now meet the aesthetic goals of building design professionals and decision-makers at schools, hospitals, and commercial buildings who require products that comply with increasingly stringent fire codes while still demanding visual quality comparable to float glass.
To rank higher on the CRI, manufacturers have altered their processes in several ways. For example, one maker of fire-rated glass ceramic has offset the amber cast by introducing more neutral gray tones, which the human eye perceives as unnoticeable. However, an unfortunate side effect may include an increase in the glass’ hazy appearance. Another manufacturer has achieved the industry’s highest CRI (i.e. 97.1) by incorporating refined raw materials into the manufacture of its glass ceramic product and improving surface-polishing technology. The unique chemical composition and manufacturing process contribute a glass ceramic that can more closely match the visual qualities of standard architectural float glass.