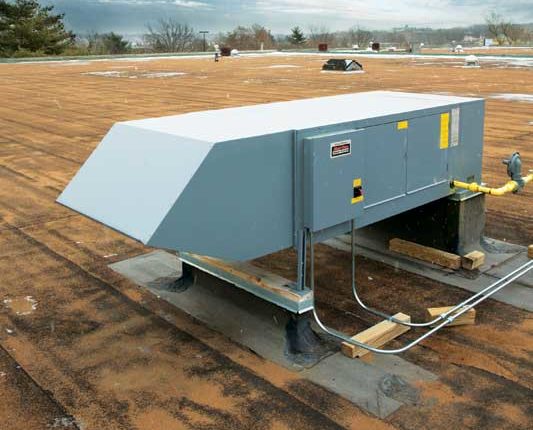
by Marc Braun
The Better Buildings Alliance, an initiative of the United States Department of Energy (DOE), is designed to improve the efficiency of commercial and industrial buildings in the U.S. by driving leadership in energy innovation.
The commercial buildings sector—where 15 percent of the total floor space comprises warehouse and distribution space—consumes nearly 20 percent of all energy used in the United States. As a nation, the U.S. spends more than $200 billion annually to power the country’s commercial buildings. Unfortunately, much of this energy, both electric and natural gas, is wasted because of inefficient or outdated technology. Energy-efficient technologies, if installed, commissioned, and operated properly, are a cost-effective way to save money and reduce pollution (Figure 1).
Over the past 25 years, the American Society of Heating, Refrigeration, and Air-conditioning Engineers (ASHRAE), 90.1, Energy Standard for Buildings Except Low-rise Residential Buildings, has dramatically increased the minimum efficiency requirements of commercial buildings and their associated equipment. The Pacific Northwest National Laboratory (PNNL) reported that over this period there was a 44 percent improvement in lighting efficiency, 27 percent improvement in cooling efficiency, 21 percent improvement in building envelope efficiency, and 37 percent improvement in overall efficiency across commercial buildings built to meet ASHRAE 90.1. Unfortunately, PNNL reported only a one percent improvement in heating efficiencies during those same 25 years.(See M. Rosenberg, et al’s 2014 article, “Roadmap for the Future of Commercial Energy Codes,” for the Pacific Northwest National Laboratory. The 2012 International Fuel Gas Code can be found online at publicecodes.cyberregs.com/icod/ifgc/2012/icod_ifgc_2012_6_sec011.htm)
For many of these buildings not requiring space cooling, non-centralized equipment such as unit heaters provide the space-heating. Unit heaters are found in commercial and industrial buildings throughout the United States—most prominently in warehouses, distribution centers, and loading docks. In addition to space-heating, these buildings require ventilation systems to meet the minimum required code ventilation rates of ASHRAE 62.1. For most applications, separate systems provide space-heating and outside air, adding project complexity and energy consumption.
The Department of Energy published a study, “Field Demonstration of High-efficiency Gas Heaters,” where it discussed how high-temperature heating and ventilation (HTHV) direct gas-fired heaters dramatically reduce energy consumption when replacing unit heaters in warehouses and other high-bay buildings.
These direct-fired technologies—often referred to as ‘make-up air heaters’—have been widely adopted as high-efficiency ventilation units. The surprising thing is specialized versions of these products can accomplish high-efficiency space-heating when ventilation is not required, such as during unoccupied times. This is because they feature an innovative high-discharge temperature and high-velocity discharge. In the study, HTHV direct-fired gas heaters demonstrated a 20 percent gas savings when replacing the heating function of standard indirect gas-fired unit heaters. (See J. Young’s 2014 report “Field Demonstration of High Efficiency Gas Heaters,” prepared for Better Buildings Alliance, Building Technologies Office, Office of Energy Efficiency, and Renewable Energy of the U.S. Department of Energy). If widely adopted to replace traditional heating systems, these HTHV technologies could substantially reduce energy consumption and utility bills for warehouses and other types of high-bay applications throughout the country.
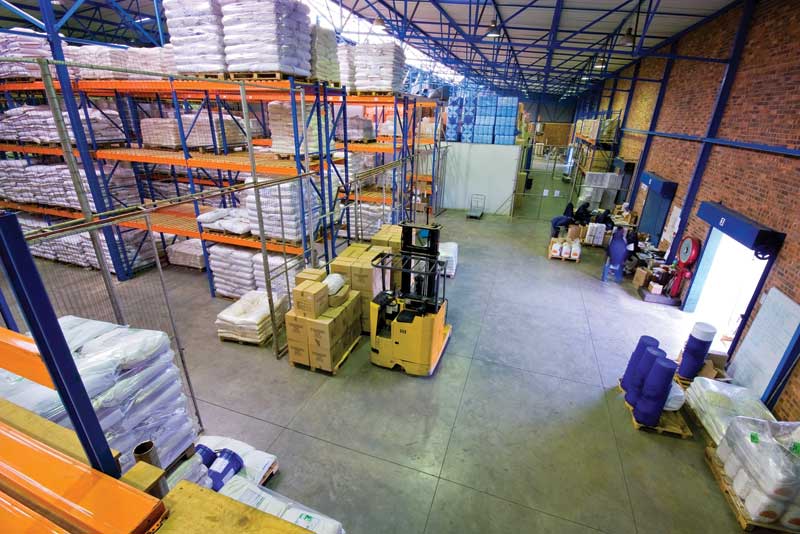
Photo © Bigstock.com
Direct gas-fired heaters meeting American National Standards Institute (ANSI), Z83.4, Non-recirculating Direct Gas-fired Industrial Air Heaters, blend 100 percent outside air directly with a gas flame. Every joule (Btu) of energy created from the gas combustion is delivered directly to the space without any heat exchanger losses. HTHV technologies are those that ANSI Z83.4 certified to a maximum discharge air temperature, greater than or equal to 66 C (150 F), and a maximum temperature rise, greater than or equal to D78 C (D140 F).
During winter operation, the heated outdoor air is delivered at temperatures slightly above the ambient space temperature to a maximum of 77 C (160 F), offsetting air being displaced by an exhaust system or building infiltration. Temperature controls typically maintain a relatively constant discharge air temperature for ventilation applications, or space temperature for heating applications. This is done by modulating the gas flow (i.e. typically, modulation is 20:1) to adjust for varying outdoor temperatures, space-heating, and ventilating needs.
During mild weather, the equipment is generally fitted with an economizer thermostat to disable the burner when the outdoor temperature approaches the desired indoor temperature. Due to the ventilation air and the combustion air being delivered by a common blower, gas combustion heating cannot occur without proper ventilation. This feature causes the safety standards for both Canada and the United States to harmonize with these technologies. Equipment certified to ANSI Z83.4 can be installed with a minimum amount of ductwork, providing an efficient and cost-effective installation. Additionally, the weatherized technology offers installation flexibility as units can be placed indoors or outdoors or in horizontal or vertical configurations while still being always connected to 100 percent fresh outside air.
The 2012 International Fuel Gas Code (IFGC) requires all HTHV direct gas-fired technologies to be certified under ANSI Z83.4. These technologies are covered specifically under Section 611 of the IFGC and by reference in the 2012 International Mechanical Code. The IFGC states ANSI Z83.4 technologies are to be used for commercial and industrial applications for heating and ventilation requirements per the scope of that standard.