Designing Effective Insulation: Gravity, thermal bridging, and the importance of being continuous
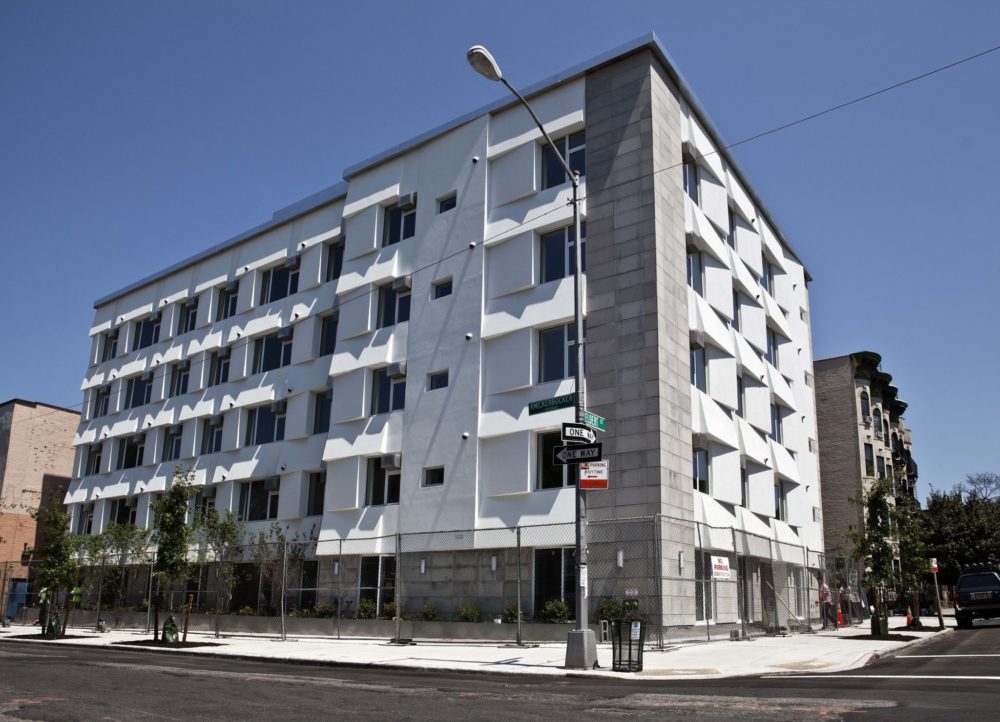
by John Edgar
Insulation manufacturers have devised numerous ways to improve the thermal performance of their products. Adding carbon or alumina particles to expanded polystyrene (EPS) increases infrared reflectance, and hence boosts R-value. For buildings that need heat stopped during the day and released at night, there are phase-change materials. More exotic products, like vacuum insulated panels (VIPs) and aerogels, boast great R-values for difficult-to-insulate locations. Materials using recycled or renewable products will appeal to those chasing points under the green rating programs.
Unfortunately, none of this matters when these high-performance products are installed ineffectively. It is old news batt insulation in steel studs loses half its R-value. Steel studs themselves act like ‘radiator fins’ to the exterior—they are a prime example of a thermal bridge, along with shelf angles and structural connections.
Thermal bridging
New research shows that thermal bridging through insulation is a much more serious problem than previously suspected. Continuous insulation (ci) outbound of the studs is the accepted solution. Code-writers have taken note and change is coming. For example, in the International Energy Conservation Code (IECC), Table C402.1.2 provides the total U-value of the opaque wall area including continuous insulation. It also references the American Society of Heating, Refrigeration, and Air-conditioning Engineers (ASHRAE) 90.1, Energy Standard for Buildings Except Low-rise Residential Buildings. If ASHRAE 90.1 is modified to include linear transmittance, as described in this article, then there will be significant change in the way buildings are designed.
In some ways, the new battlefront in construction will be energy conservation versus gravity. Thermal bridging needs to be eliminated, but something has to hold the cladding on the building. In all methods of construction, the cladding dead load has to be secured to the structure through the ‘continuous’ insulation.
What holds the insulation in place? It could be adhesive, as is the case for exterior insulation and finish systems (EIFS). However, screws with washers are often used to secure the insulation to the supporting structure. Typically, for thermal energy calculations, the diameter of the screw shaft can be compared to the insulation area, yielding a thermal bridge ratio of about 0.05 percent—an apparently insignificant amount. In fact, a thermally conductive shaft transmits heat from an area many times larger than its diameter (Figure 1).
Thermal bridging through fasteners cools the temperature inside by radiating heat out of the wall. If the fastener tip is below the dewpoint, the result may be condensation and potential corrosion—not good for long-term durability and resilience. Fortunately, there are now inventive collections of fasteners that have reduced thermal conductivity and are corrosion-resistant.
With the energy modeling discussed in this article, the starting point in the calculation will be a ‘clear wall’—that is, an area of opaque wall devoid of major thermal bridges. The ‘clear wall’ value is determined by guarded hot-box calculations. Insulation fasteners are included as part of the ‘clear wall,’ so their effect is thus included in the base calculation. Essentially, there is no need to model every one. However, if a particular design is running close to the acceptable mark, something as trivial as fasteners may require examination.
Calculating thermal performance
The way the building envelope’s thermal performance is calculated has changed, thanks to more powerful computers and an amazing degree of sophisticated modeling. The same computer simulations that model heat shield performance during spacecraft re-entry also work, for example, to determine heat loss through a floor slab.
Until recently, the parallel approach to heat loss calculations was used. As with the slab penetration shown in Figure 2, the energy flow through the wall and slab were calculated based on the elevation area. The heat flows were added based on the ratio of wall to slab area. Any lateral flow of energy was ignored.
The reality is energy moves in all directions and a cold uninsulated slab will draw heat not only from the slab, but also from the interior air and wall assembly above and below (Figure 3). Therefore, the insulation in the wall is rendered less effective because heat flows around it and out the slab. The problem has been how to accurately calculate the energy end run.
In July 2011, engineering firm Morrison Hershfield Ltd. presented a paper to ASHRAE showing how advanced computer modeling could accurately predict heat flow through thermal bridging. (The firm’s “Thermal Performance of Building Envelope Details for Mid- and High-Rise Buildings (1365-RP)” was presented to the American Society of Heating, Refrigeration, and Air-conditioning Engineers’ Technical Committee 4.4 on July 6, 2011). This research evaluated thermal performance data of 40 common building envelope details for mid- and high-rise construction. The modeling was validated by 29 guarded hot-box measurements. The intention was to modify the energy calculation methods described in ASHRAE 90.1.