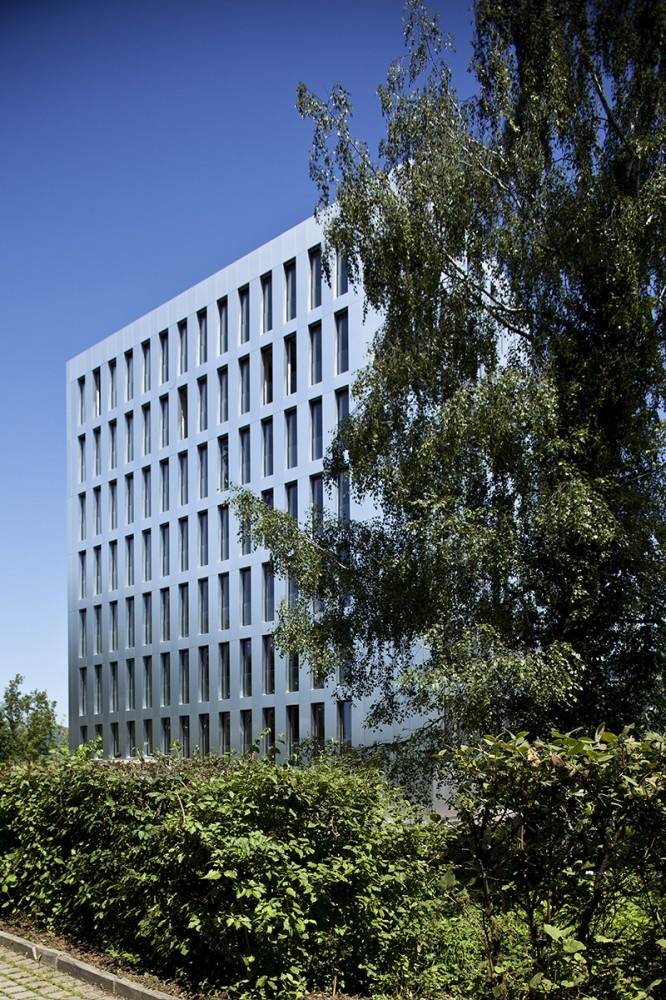
by Nabih Tahan, AIA
For buildings to perform better, the construction industry must change the way it designs and builds. Lifecycle Tower (LCT) ONE, an eight-story wood office building in Austria, is both a prototype and proof of a concept that demonstrates an innovative process and building. Through its use of wood, LCT ONE focuses on reducing the negative impact of buildings on the environment, while improving comfort and indoor air quality (IAQ) for occupants.
LCT ONE began as a research and development project based on the lifecycle assessment (LCA) of buildings. The motivation was to find a substitute for traditional construction practices that can have negative impacts on local and wider environments. The population is growing and the trends are shifting. People are moving from rural to urban areas. Cities must find new ways to grow around transit systems with sustainable developments that do not deplete resources and harm the environment. Therefore, cities must readapt to the current changes.
The sustainable wood and concrete hybrid building is now occupied and showcases a way of achieving mid-rise and tall buildings that can go up to 100 m (328 ft) and 30 stories.(Figure 1).
Motivation for research project
A sustainable strategy must consider the entire lifecycle of a building and its materials. This includes resource extraction, material production, construction, operation, demolition, and recycling. Since the Industrial Revolution, progress in developing cities translated into more concrete and steel produced with oil and coal, to build tall and mid-rise buildings. LCT ONE was developed to introduce alternatives by substituting renewable resources for fossil fuels, along with systems and processes that can yield better building performance.
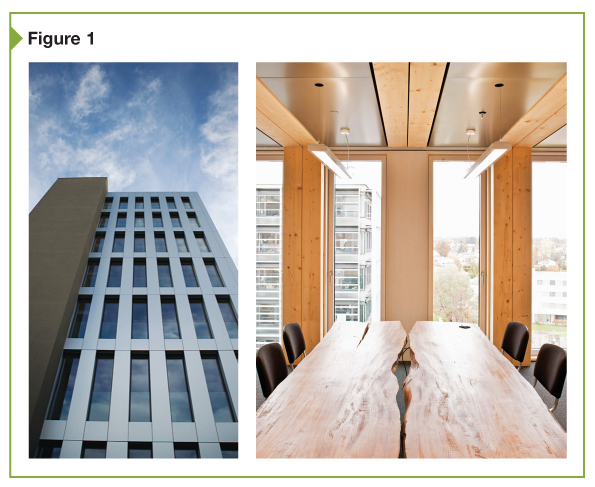
Forestry carbon cycle
Wood is a renewable resource that grows from the sun—it is the ultimate solar product. Trees absorb carbon while providing oxygen. Modern timber-based products, such as engineered lumber, are available worldwide. Heavy glued-laminated timber (glulam) members are stable, will not shrink and twist, and can be pre-cut and prefabricated to exact tolerances, which are airtight, resulting in saved energy. At the end of a building’s life, the wood can be reused for other purposes and later turned into fuel and energy.
Further, use of wood is carbon-neutral. In other words, growing forests absorb carbon from the atmosphere and wood products store carbon. It remains stored when wood products are recycled into other products. At the end of their life, bioenergy is produced from these products, as well as from mill and forest residues and reforestation ensures the carbon cycle continues.
Ecological backpack
Selection of building materials should be linked to the use of natural resources, including raw materials (renewable and non-renewable), energy, water, and land. To specify products for the LCT system, data was collected and calculations performed to measure the total amount of natural resources required to produce a certain product or building. Since trees grow above the ground, it is resource- and energy-efficient to extract and produce wood as a building product. Wood has a much lower ecological ‘backpack’ than traditional materials, such as concrete and steel.1
Prefabricated construction process
Austria has a long history of prefabricating high-performance building components out of wood. The process begins with computer-aided design (CAD) software used to cut lumber using computer-numerical-controlled (CNC) machinery. The members are assembled in a carpentry shop, under a controlled environment where windows, insulation, sheathing, vapour retarders, and finishes were installed. The components are made to tight tolerances, can be quickly assembled onsite, and meet the most stringent blower door test requirements. Modern timber technology is available and can deliver high-performance buildings using renewable resources (Figure 2).
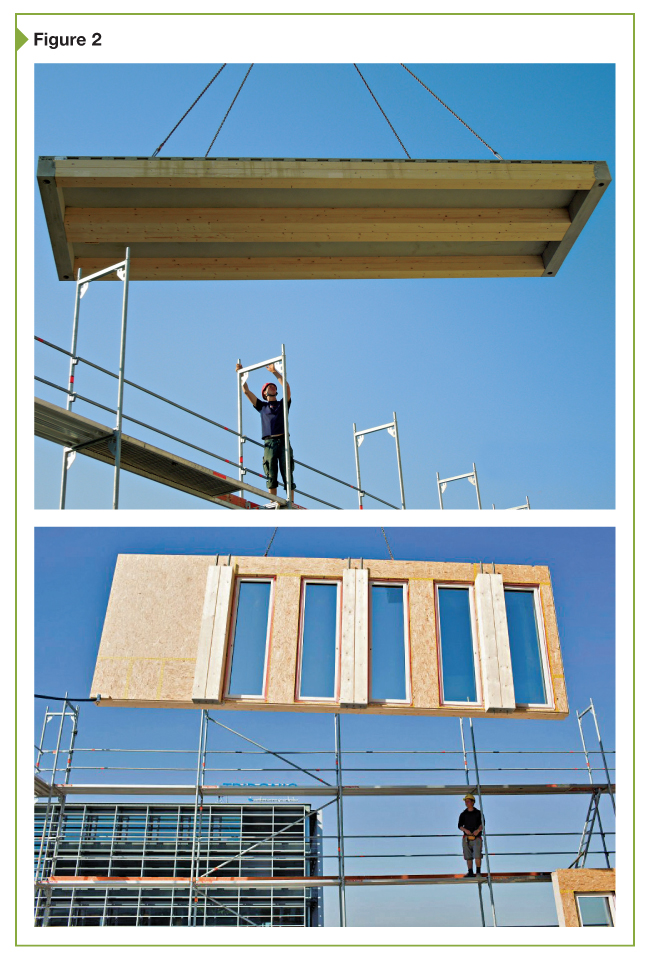
Operation and maintenance
Existing buildings consume a lot of energy during their operational life. To reduce consumption, the LCT system was developed according to the stringent Passive House standard introduced in Germany. The strategy is to drastically reduce consumption before relying on renewables. This is the surest path to reach zero net energy. Highly efficient solar and mechanical equipment have an ecological backpack, therefore ‘less is more.’ No need to heat and cool is more sustainable than heating and cooling with renewables or high-efficiency equipment.
The energy modeling software program Passive House Planning Package (PHPP), is an accurate tool for predicting heating demand and peak heating load in low-load buildings. The PH standard is based on energy performance (kWH/m2/year [kWH/sf/year]); in Europe, the predicted energy consumption during the design phase has proven to be accurate when compared to actual consumption during operation.2 These metrics and strategies are valid across different climate regions of the world.
To guarantee maintenance and durability, a building science consultant is part of the integrated design team and advises on the permeability and diffusion of the entire building enclosure. The most important aspect is airtightness, which prevents air and moisture from entering the building enclosure. Additionally, the building’s exterior finish material is always installed on a rainscreen, creating a ventilation layer behind it and allowing any water penetration to drain before it reaches the building enclosure.
Urban mining
All building products originated from mining the earth. At the end of their ‘lives,’ buildings are typically added to landfills and new materials are mined. The LCT research project strived to develop a solution where reusable materials are saved from landfills. Urban mining conserves our natural resources, eliminates potential energy costs, and greenhouse gas (GHG) emissions. When a building has reached its full useful life, urban mining of the LCT system can be activated, extracting materials to reuse, recycle, and convert into bioenergy, thus protecting landfills from unnecessary waste.
System and product development
As a result of the research phase, LCT ONE was designed and built as a proof of concept. The goal was to develop a system and products that can be used on any urban infill projects, but with wood replacing concrete and steel, where possible. The goal was to introduce an industrial process for buildings—similar to the process used by car and computer companies to design and build their products. Instead of miles per gallons, building performance can be guaranteed in kWh/sf/year.
To reach this goal for tall, large-volume wood buildings in urban settings, the LCT system integrates:
- planning;
- offsite production and onsite assembly;
- use and future conversion;
- dismantling; and
- recycling of buildings.
Structural system
The LCT system was developed as a core and shell that acts as the structural system and enclosure of a tall, large-volume wood building. This system is analogous to the ‘Intel Inside’ of a computer. It is the hidden operating system on which each manufacturer relies, but each computer looks and performs according to the manufacturer’s design and specifications. Similarly, the core and shell of the LCT system can be looked at as the ‘LCT Inside’—each architectural and engineering team can design the building according to its own aesthetics, integrating the site and client’s program requirements into the design.
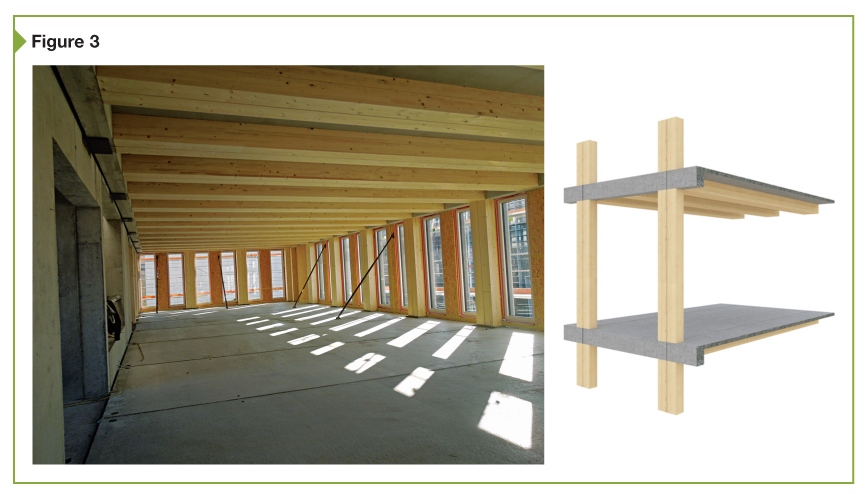
The core is where the elevators, stairs, wet rooms, and shafts are located. It serves as the building’s stiffening element. While wood is the optimal choice as a material for the core, concrete and steel can also be used until codes enable creation of taller wood buildings.
The gravity loads are carried by a series of heavy-timber glulam posts on the exterior of the building spaced approximately 3 m (10 ft) apart. These posts are exposed on the building’s interior, adding to the warm aesthetic of the space. For fire protection, the size of the post is increased beyond the structural requirements. Approximately 38 mm (1 1/2 in.) of wood for one-hour fire protection is added to each exposed surface of the posts, which creates a charring layer in case of a fire. Wood burns ‘safely,’ because based on fire tests, calculations, and simulation, predictions can be made on how long wood will withstand the flames—therefore, the building codes allow this additional thickness in recognition of the superior fire endurance demonstrated by large wood beams and columns in fires. (Figure 3).
Hybrid wood/concrete floor slabs span about 9.1 m (30 ft) between the exterior heavy timber posts and the core, transferring all lateral forces from the former to the latter. The benefit of a hybrid system is it takes advantage of the properties of each material to meet all the structural, fire, acoustic, and thermal requirements using the least amount of resources and energy. The hybrid slabs were tested in a full-size fire chamber and passed a two-hour fire test.
International Building Code (IBC) requires ASTM E119, Standard Test Methods for Fire Tests of Building Construction and Materials. However, in this case, the tests were performed in Europe according to International Organization for Standardization (ISO) 834, Fire Resistance Tests—Elements of building construction, which is the governing full-scale furnace test.
The design of the slabs provides a built-in fire separation between each floor because there is no wood-to-wood contact between floors.
Integrated building enclosure
The building enclosure is then integrated with the core and shell to give the building its aesthetic appearance. The façade is a curtain wall that withstands wind loads, but not gravity forces. The seismic forces are transferred from the glulam posts to the hybrid slabs through a hinged connection.
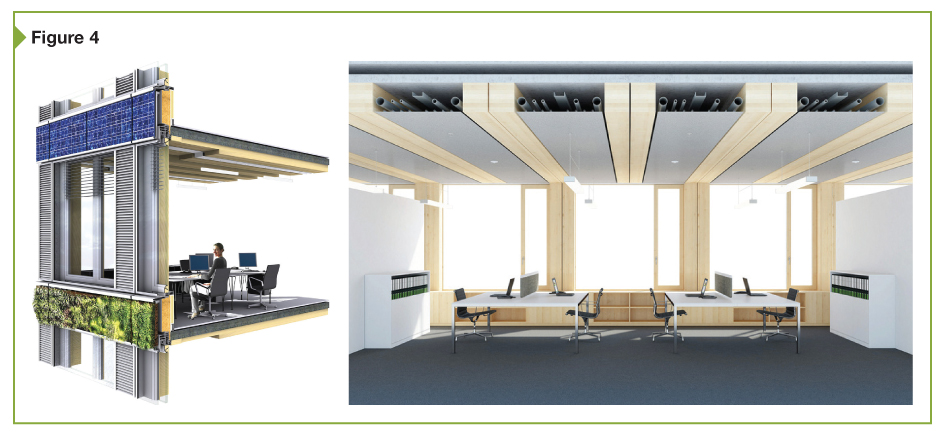
The enclosure can be made of any material, but many prefer wood, as it is a renewable resource. The windows, insulation, water, air barriers, vapor retarders, and exterior finishes are designed with the collaboration of a building scientist, mechanical engineer, and exterior wall manufacturer. These sections take into consideration the orientation of the building, as well as the energy performance and standard demanded by the client.
Integrated MEP Systems
Similarly, the mechanical, electrical, plumbing (MEP), and fire protection systems can be integrated within the core and shell and optimized according to the building orientation and enclosure. The systems can be prefabricated and are easily accessible between the structural members. (Figure 4).
Planning process
As a prototype, LCT ONE is proof of the Lifecycle Tower concept. Its foundation and core were built onsite with traditional reinforced concrete construction. The building enclosure was timber frame and the floor elements were made out of the wood/concrete hybrid slabs.
To guarantee performance, the LCT concept is designed to automatically meet the requirements of certification programs. However, as a prototype, it was necessary to compare the LCT system to mainstream certification programs. As mentioned, LCT ONE was designed to meet Passive House and received official certification from the Passive House Institute in Germany. It also applied and received Deutsche Gesellschaft für Nachhaltiges Bauen (DNGB) Gold certification from the German Sustainable Building Council.
Energy standards and certifications
The goal was to meet the energy requirements of Passive House because it has proven to be accurate in predicting actual energy consumption. In collaboration between the engineers and building enclosure manufacturer, the building envelope—as well as the mechanical, electrical, and ventilation systems—were designed to optimize the building performance according to the given location and orientation. By using the PHPP software, multiple reiteration were attempted to optimize the balance between the orientation, building enclosure, mechanical, electrical, and renewable energy systems.
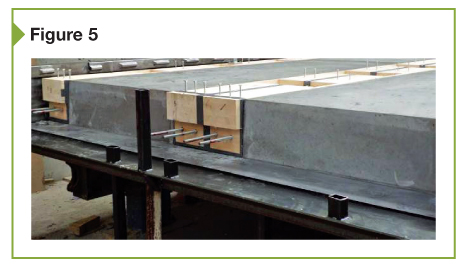
Orientation
The building orientation was governed by the property’s existing location. The orientation created a negative effect on the energy balance. The building would have performed better if it could have been rotated by 90 degrees. To mitigate the effect of the orientation, the thermal performance of the building envelope was improved by increasing the thickness of the wall and insulation and specifying higher-performing triple-glazed windows.
Building enclosure
The building enclosure consisted of prefabricated timber frame walls, where the insulation, windows, and sheathing were installed offsite. The connection and intersection between all wall, floor, and roof elements were designed to minimize thermal bridging. Insulation was applied on the exterior of the window frames to decrease heat losses through thermal bridging. All joints were taped to be airtight in order to meet the Passive House blower door test requirements. This test is one of the three requirements needed to meet Passive House certification. It measures infiltration air flow at a pressure difference of 50 Pa. The requirements stipulate it cannot exceed 0.6 air changes per hour (ach) at 50 Pa.
The shape, size, and number of windows were optimized for low heat loss in the winter and low heat gain in the summer, as well as to reduce demand for artificial lighting throughout the year. Tilt-and-turn operable windows were specified to allow for natural ventilation—as they open to the interior, they allowed exterior shading devices to be installed for reducing heat gain in summertime.
Passive heating and cooling
Passive heating is achieved by large windows in the staircase (eastern orientation). The morning sun heats up the concrete wall and heat is stored in the wall’s thermal mass. Passive cooling is achieved by operating the chiller machine in a free-cooling-mode during most of the year. Further, the optimized ratio between transparent windows and opaque walls, as well as deep window reveals, prevents the office building from overheating in the summer.
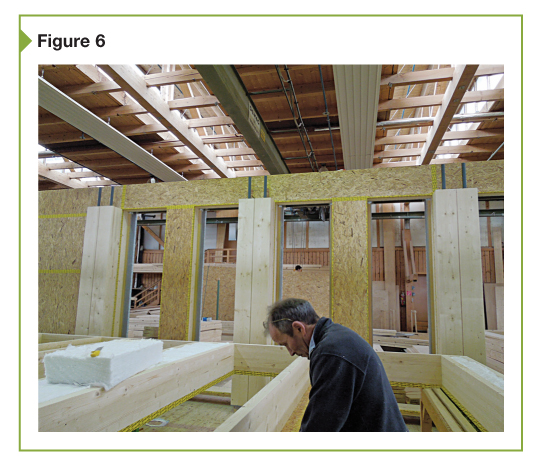
Building system
The following building systems were used on LCT ONE:
- heating system: district heating system—renewable-fueled combined heat and power;
- cooling system: conventional chiller machine with enhanced free-cooling-option;
- hot-water system: highly efficient, decentralized water boiler on each floor;
- heat recovery ventilation: central system installed in basement with carbon dioxide (CO2) sensors on every floor that control the amount of air introduced;
- lighting: fully automated and daylight-dependent lighting system (including motion detection), automated dimming and zoning, and daylight-dependent shading operation and positioning;
- services: fully automated building services system;
- controls: motion and window detector controlled heating and cooling, as well as CO2 sensors;
- waterless urinals; and
- photovoltaics (PV): 10-kW (peak) rooftop system—prepared for future installation of a 10-kW PV on the southern façade, which will be required to become a zero net energy building.
Verification
Blower door tests were conducted in two stages. The first was a random test at two floors performed after the installation was completed. (The core was excluded.) The result was 0.35 ach at 50 Pa. Before commissioning, a blower door test was performed on the entire building, including the core. The results were 0.55 ach at 50 Pa, meeting the Passive House standard.
Construction process
While foundations and concrete core where being built onsite, the wall elements and the hybrid wood/concrete floor slabs were produced offsite. The assembly of the wall and hybrid floor elements took eight days onsite, one floor per day.
Producing slabs
The industrial production of the hybrid wood/concrete slabs took place in a precast concrete shop. The heavy timber glulam beams were supplied by a lumber manufacturer who cut them accurately with CNC machinery and attached the required metal fasteners and connectors. The beams were delivered to a precast concrete manufacturer, who placed them in metal forms, added metal reinforcement and poured the concrete. This process was repeated daily for each form. The advantage of this system is it allows the concrete to cure offsite and prevents additional moisture into the building. Additionally, prefabricated slabs are assembled quickly onsite (i.e. eight minutes per slab) to tight tolerances (Figure 5).
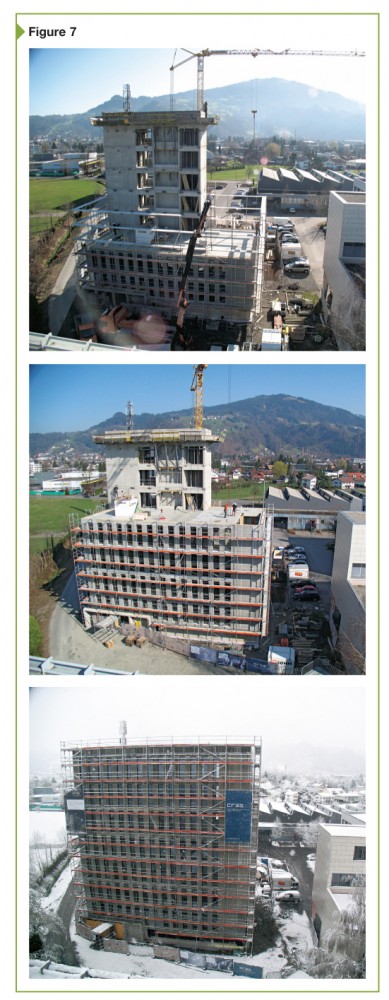
Producing walls
The walls were produced in a local carpentry shop. Engineered lumber was used for all wood members, including studs. The panels were produced on tables, horizontally, where the timber frame, sheathing, and insulation were installed. After standing up the walls, the windows were installed. All joints, including around the windows, were sealed airtightly with high-performance tapes (Figure 6).
After production, all the slab and wall elements were shipped to the site and assembly began. Five skilled carpenters were able to assemble all the components, water- and airtight in eight days, for all eight stories (Figure 7).
To verify the energy standard will be met, blower door tests were performed twice as mentioned—once when the installation was done and again before commissioning.
Conclusion
LCT ONE begins with the premise the building industry does not automatically have to rely on concrete and steel for all urban buildings; it demonstrates there is the opportunity to substitute timber for many applications.
Wood is a renewable resource. Essentially, while one building is in construction, the sun is producing the timber for the next building. Timber technology has advanced, where modern industrial machinery and processes make it possible to erect timber buildings quickly, economically, and according to all building regulations and high-performance standards.
LCT ONE is pioneering a new way of building, based on guaranteeing performance. It was developed according to a system that can be the shell and core, while still offering flexible design solutions and architectural and aesthetic possibilities to make each building unique. By following this ‘system approach,’ the performance of buildings can be guaranteed, similar to the performance of cars, computers, and other products manufactured through industrial processes.
The LCT system can be applied as a worldwide solution. With its introduction in Europe and now beginning in North America, it serves as an inspiration to wean the traditional building industry away from only fossil-fuel-intensive products and systems. Less-developed countries, especially those with forests, can adapt the LCT system to modernize their building industry. They can introduce new sustainable forestry management policies and begin manufacturing modern, engineered lumber products to build high-performance timber buildings. A new process of education to create new green jobs and affordable housing solutions could be an alternative to attempting to develop building solutions that rely on fossil-fuel-based resources that less-developed countries do not have and cannot afford.
Notes
1 For more on the ‘ecological backpack’ concept, see M. Ritthoff et al’s Calculating MIPS: Resource Productivity of Products and Services, at epub.wupperinst.org/frontdoor/index/index/docId/1577. See also K.-H Robèrt et al’s “Strategic sustainable development–selection, design, and synergies of applied tools” in the June 2002 issue of Journal of Cleaner Production. (back to top)
2 For more information visit, www.cepheus.de. (back to top)
Nabih Tahan, AIA, is an international architect, Passive House consultant, and vice president of business development for Cree Buildings. For more than 30 years he has honed his knowledge in architecture, energy efficiency, and sustainable timber-based construction methods through work in Austria, Ireland, and the United States. In 2005, his own retrofitted home became the first Passive House home in California. Tahan also acts as the North American ambassador for Cree Buildings, and educates architects, developers, building engineers, and municipalities on the potential of tall wood buildings. He can be contacted at nabih.tahan@creebuildings.com.
ich bin eine freiberufliche Dolmetscherin und moechte ich Ihnen
hiermit eine Anfrage schicken.
Es geht um die Professoren aus Japan, Herr Wirtschaftswissenschaft Prof. Nishiyama und Prof.
Iuchi der Meijo Universitaet in Nagoya, moechten Im Maerz Ihre Firma besuchen.
Ihre Recherchenreise nach Deutschland hat die Themen : Energiewende in
Detuschland, Biomass-energien, BHKW und energieeffiziente Gebaeude in Deutschland
Meijo Universitaet macht jedes Jahr eine Studienreise nach
Deutschland mit den Themen der duetschen innovativen Technike, vor
allem mit den erneuerbarern Energien.
Die Beiden Professoren machen vorher eine Recherchenreise nach
Deutschland , um eine Besuchsziel im Vorfeld zu recherchieren.
Ihre Firma ist sehr interessant fuer die beiden Professoren, so
moechten wir Sie bitten, uns eine Erlaubnis zu geben, Ihre Referenzbebaeude zu
besuchen und sich ueber Energiesystem kennenzu informieren.
Wir sind am 1. Maerz in Regensburg und bleiben bis 5. Maerz in Bayern.
Ich wuerde mich ueber Ihre Rueckmeldung freuen.
Mit freundlichen Gruessen