By Ian Hudock
Metal rolling and sectional doors are becoming popular in commercial construction thanks to their functional versatility and sleek designs. Much like other architectural elements, commercial structures have to look attractive while contributing to sustainable design and energy efficiency goals. For architects, designers, and specifiers, this means careful attention must be paid to the thermal performance of metal rolling and sectional doors.
R-value is often used for judging the insulating ability of static building materials, but metal rolling and sectional doors require additional considerations when it comes to assessing thermal performance. Since commercial doors are dynamic elements and comprise more than one material, builders must also take U-factor into consideration.
Here is a deep dive into everything architects, designers, and specifiers need to know about U-factor, including how it is measured, how it differs from R-value, and why it matters for specifying rolling and sectional doors.
R-value and U-factor
Unlike assessing the thermal performance of simple structures such as walls and ceilings, rolling and sectional doors are complex architectural elements and require more comprehensive evaluation. Where R-value is useful for static materials such as drywall, U-factor is a more accurate measure of the thermal performance of these multi-component assemblies.
R-value
- R-value measures the thermal resistance (insulating effectiveness) of a single material or architecture element. It indicates how well a material can resist heat flow, and it is commonly used to measure the thermal performance of elements such as walls, roofs, and ceilings.
- High R-value is good. A material with a high R-value means it is effective at slowing the rate at which heat passes through it. In colder months, heat stays in. In warmer months, heat stays out.
U-factor
- U-factor measures the rate of heat transfer through an entire assembly, not just a single material. It accounts for all components of an assembly, including its composite materials, their individual R-values, and how they perform collectively, including—in the case of doors—how much heat transfer occurs around the perimeter.
- Low U-factor is good. For a complex element (e.g. a rolling or sectional door), a low U-factor means the entire assembly is effective at limiting heat gain in the summer and heat loss in the winter, thus reducing HVAC demand and lowering energy costs.
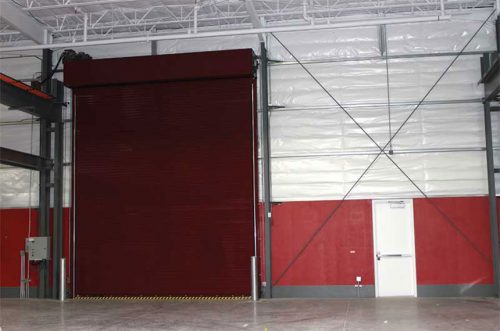
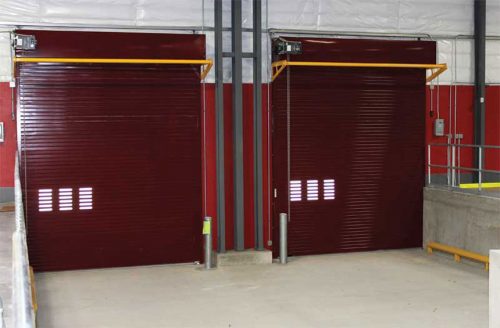
By seeking a low U-factor for heat transfer in rolling and sectional doors, building professionals can help ensure their designs are energy-efficient.
Understanding the operational mechanics and material components
Choosing a metal rolling or sectional door with desirable thermal performance involves navigating the complexities of how these doors function, their material makeup, and how they interact with a building’s thermal envelope.
Specifically, metal rolling and sectional doors operate by coiling up around a shaft or by folding up in sections as they open, and then unrolling or unfolding as they close. This dynamic movement has several implications for thermal performance requiring U-factor for accurate measure. These include:
- Air leakage—The door’s movement creates the potential for air infiltration between sections, between the door and the frame, and at the door’s threshold. To open and close, the door must maintain a slight clearance between these elements to operate smoothly. This clearance allows air exchange, impacting the building’s overall thermal envelope.
- Thermal bridging—Dynamic rolling and sectional doors feature metal opening and closing mechanisms that can act as thermal bridges, conducting heat out of a building in winter or into a building in summer.
- Seal integrity—Overhead doors are designed with seals and weatherstripping to minimize air leakage during movement and when fully closed. How well a door is engineered and the quality of its seals, impact its thermal performance and U-factor.
In addition to operational mechanics and differences in manufacturers and engineering, another argument supporting U-factor is material composition. Rolling and sectional doors can feature metal, typically aluminum or steel, and transparent or translucent materials, such as glass, acrylic, or polycarbonate. These materials impact thermal performance in several ways:
- Steel and aluminum—These materials provide strength, security, and durability, but these metals are also conductive materials that can easily transfer heat.
- Glass, acrylic, and polycarbonate—Added for aesthetics and function, these materials introduce benefits and challenges. Glass, for example, enhances natural light and visibility and reduces reliance on artificial lighting. Tempered, insulated, frosted, and low‑emissivity (low-e) glass all have different R-values. U-factor helps guide design choices by factoring the R-value of the transparent material into the door’s overall thermal performance expressed by its U-factor.
Specifying a metal rolling or sectional door with a low U-factor can dramatically enhance a building’s energy efficiency by reducing heating and cooling demand. For architects and designers, this means being able to deliver both visually appealing and environmentally responsible designs. For construction specifiers, it highlights the opportunity to select doors that align with energy performance goals without compromising style and functionality.
Designed for energy efficiency and more
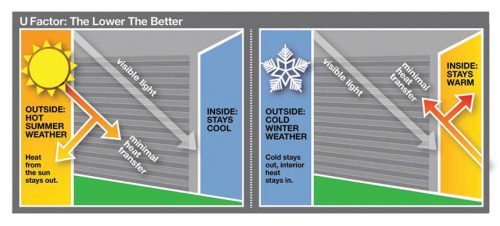
Metal rolling and sectional doors deliver a highly desirable combination of thermal performance and aesthetic appeal, which is made possible by continuing advances in material science and engineering. These advances have significantly elevated the appeal of these doors, and they are now available with more features that also attend to efficiency, such as:
- Natural light and visibility—Full-view sectional doors with glass, acrylic, or polycarbonate sections allow natural light to penetrate deeper into a building, reducing the need for artificial lighting. Maximizing natural light is a key consideration in sustainable design, contributing to energy savings and occupant comfort. Commercial clients also appreciate the reduced operational costs and the attractive, open feel of these designs.
- Optimizing space—New vertical-stacking door styles feature compact sections which stack above the door opening without overhead tracks and include gasketing between sections to address air infiltration. Their minimal space requirements do not interfere with other mechanical systems, and businesses such as restaurants and cafes have more space for tables.
- Flexible use—Rolling and stacking doors give commercial clients, such as event venues and car dealerships, the freedom to quickly adapt and add space to their properties without sacrificing heating and cooling efficiency when the doors are closed.
- More design options and finishes—Glass choices, metal finishes, and colors for metal rolling and stacking doors allow for custom designs that can complement virtually any architectural style. The broad range of options gives architects and designers the freedom to tailor doors to a specific aesthetic while still meeting the functional requirements and energy efficiency goals of their projects.
Together, modern design and engineering seamlessly blend thermal performance with aesthetic versatility to meet today’s architectural demands.
Opening the door to a new perception
Specifying a manufacturer who recognizes U-factor and integrates this measure into their commercial door designs is the ultimate goal for the building stakeholders who work with these architectural elements. A reputable manufacturer will contribute positively to the construction process, ensuring their rolling and stacking doors integrate seamlessly into the project while protecting the energy efficiency, design integrity, and smooth progression of the construction timeline. By prioritizing manufacturers who meet these criteria, construction professionals can enhance the quality and success of their projects, resulting in both energy-efficient and aesthetically pleasing spaces.
This full perimeter door sealing system is combined with thermally broken guide construction and insulated curtains to minimize air infiltration and thermal transference.
A commercial insulated door sealing system not only significantly reduces air infiltration but also reduces sound transmission.
Key distinctions between R-value and U-factor. R-value is ideal for evaluating static, single materials such as walls, whereas U-factor is used for dynamic multi-component assemblies like doors.