By Amy Becker
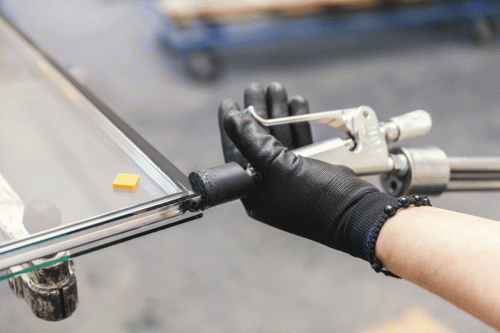
High-performance facades start with high-performing glass. Insulating glass units (IGUs) are a critical component of glazing system performance. Glass’s major role in energy efficiency, aesthetics, health, and wellness in buildings can only start with consistent, proven, and controlled IGU production and testing.
Not only do IGUs mitigate solar heat gain, thereby reducing heating and cooling costs, but solid glazing systems also allow building occupants to benefit from the wonderful qualities of daylighting, such as enhanced work performance, overall satisfaction, and better health.
However, to reap all these benefits and save on service costs down the road, IGUs must be properly sealed and materials adequately tested to prevent failure and increase the life of the installed units. To protect against failure, the Fenestration Glazing Industry Alliance (FGIA) offers rigorous voluntary testing standards.
Of note, FGIA is updating its IGMA TM-2400, Test Methods for IG Unit Sealants (Polysulfides, Silicones and Hot Melts) with detailed instructions for testing a vetted list of critical qualities, including longevity, tack-free time, shrinkage, moisture vapor transmission, shear adhesion, and air entrapment.
This article provides an overview of industry standards and specific examples of quality assurance criteria and test methods in the updated standard.
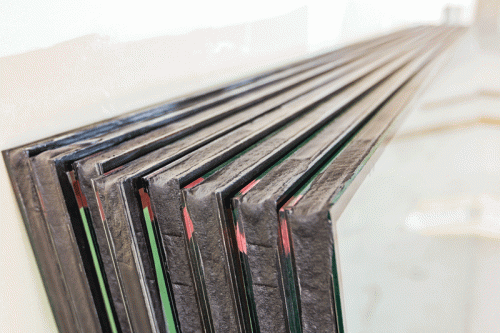
Methods and conditions
First, it is important to differentiate between the primary and secondary test methods covered in IGMA TM-2400.
A primary test method is a laboratory test that utilizes moderately precise to sophisticated test procedures and equipment to produce moderately to highly accurate test data for research and development, quality control standards, and vendor standards.
A secondary test method applies less-sophisticated test procedures and equipment, providing sufficient accuracy for quick, quality control testing.
Primary testing helps a fabricator get to know the compatibility nuances and performance characteristics of their glazing system; what material works with what and when. For example, it is critical to know how long an IGU can sit before it can be picked up and the processing continued. If one does not know, the IGU can slide apart during the rest of the build. This ensures that from project to project, their glazing system performs as intended. This primary testing also works to provide performance criteria for the fabrication quality control testing procedures.
Based on expected performance determined by the primary testing, secondary tests help to ensure that what is coming off the line, right now, is conforming. For example, checking at the beginning of the shift to make sure that the mix ratio is correct, or adhesion to the glass, or coatings, or spacer is what is expected each time. It includes verification that when, for example with two-part sealants, one part is replenished the mix still is performing properly together.
When integrated as part of a robust quality assurance program with logging of batch numbers at shift startup, testing optimizes fabrication processes, lessens rework, and ensures that the high-performing products you are creating are consistent and compliant. A little effort on the front-end can reap tremendous benefits at the back end. The following dives a little deeper into the some of the test details.
Before beginning any of the tests described below, all materials and apparatus must be equilibrated to 23 ± 1 C (73 ± 2 F), with a relative humidity (RH) of 50 ±10 percent (standard conditions) where applicable. Mixing the sealant base and appropriate curing agent should be done thoroughly, at proper ratios, for two to three minutes and slowly to avoid heat buildup.
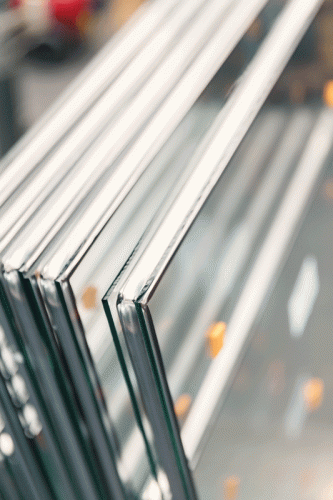
Tack-free time
Tack-free time is the time it takes for the sealant to cure and set fully. If proper tacking fails, the sealant runs the risk of migrating. This could cloud the vision area, and the displacement can also cause absorption issues. Improper tacking can leave stickiness on the surface and pick up dirt and debris, which could then penetrate the unit and cause seal failure.
IGMA TM-2400’s primary method to test this is a laboratory procedure for confirming the tack-free time of sealants. This test evaluates the time interval after the initial mixing of sealant at standard conditions, in the absence of direct sunlight, in which a polyethylene strip is pulled away from a sealant specimen and does not have any sealant adhering to it.
Polytetrafluoroethylene (PTFE) molds measuring 127 x 38 x 6 mm (5 x 1.5 x 0.25 in.) diameter are cured for the specified tack-free time. Next, a polyethylene film is laid on the top surface, and then a brass weight is set on top of the film for about 20 seconds. Finally, the film is peeled at right angles to the compound.
If the polyethylene strip pulls off from the specimen and is free of sealant, the sealant meets the requirements for cure time.
Moisture vapor transmission and permeability
If and when moisture penetrates a “sealed” IGU, the unit is on a fast-tracked path to failure. Consequently, testing for moisture vapor transmission (MVT) and permeability is critical. Knowing the sealant’s key characteristics ensures its use in appropriate applications. These key characteristics are outlined in the IGMA TM-2400, which offers three different primary test methods: the simplified cup, the automated method, and the alternative automated method.
Currently accepted units are shown as g/24h*m2; the MVT is the rate of MVT through a barrier. The water vapor permeability is the value given when the MVT is multiplied by the thickness of the sample divided by the vapor pressure difference between the two sides commonly stated in metric perm centimeter as (g*cm)/(m2*day*mmHg). The SI unit is the (mol*mm)/(m2*s*Pa), and the U.S. unit gn*h–¹*ft–²*inHg–¹ always with the test conditions noted. Careful attention must be paid to the appropriate units during calculations.
Simplified cup method
The simplified cup test provides instructions for constructing a sealant specimen, which is then cast in a PTFE ring on a PTFE sheet. The sealant base and curing agent are mixed, and then another PTFE sheet is placed on top. The PTFE assembly is pressed with one of the glass lites to force out the excess material, and the assembly between the lites is fastened with clamps.
After the initial curing, the clamps, glass, and PTFE sheets are removed, and the specimen is forced out of the PTFE ring while checking for bubbles. After curing for seven days, the specimen is placed in a petri dish with distilled water and sealed on the dish.
The test then includes detailed calculations for measuring the specimens inside a desiccator and calculating the MVT over a few weeks. The report includes the following information for each specimen tested: the name and number of the batch, MVT and permeability, and the temperature maintained in the desiccator.
Automated method
Another option is the automated method, which measures the amount of moisture in g/m2 of exposed area per 24 hours that passes through a slab of a given thickness.
The procedure is described as pressing a bubble-free slab of test material between two pieces of mold-release paper. The 152 x 152 mm (6 x 6 in.) sample is then cured for seven days under normal conditions.
Next, the sample is run under a permeation analyzer at 23 ± 1 C (73 F) in accordance with the instruction manual. A film or mesh is used to support materials that sag or cold flow.
Using common international units, the permeability is calculated by the MVT times the specimen thickness of 1.5 mm (0.060 in.), divided by the
19.8 mmHg vapor pressure difference.
Alternate automated method
With the alternate automated method, the procedure varies in that the de-aerated sealant to be tested is pressed out into a sheet 1.5 mm (0.060 in.) thick, using the release substrate. The sealant and substrate are then removed from a heated laboratory press and trimmed to 152 x 152 mm (6 x 6 in.) with the release substrate intact.
Running the permeation analyzer and performing the calculations, then proceed in the same manner as the automated method.
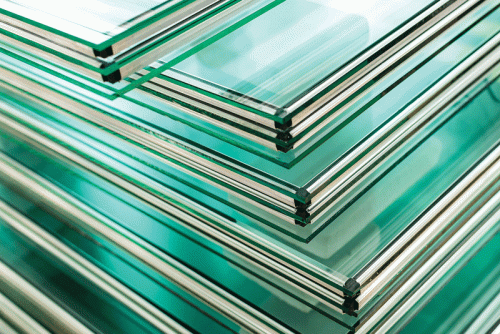
Shear testing
It is important to note that sealants in IGUs must properly adhere, or system failure is likely. Going one step further, cure time must be verified. IGUs are exposed to significant loading, so the performance characteristics of all aspects of the system must be verified. Shear forces can rip apart the IGU if the loads are too great.
The primary and secondary dead load, creep, and overlap sheer tests can be utilized to evaluate a unit’s shear forces.
Dead load
Dead load occurs when one or more panes of glass in a multi-lite IGU are unsupported relative to the other lite or lites of glass in the same unit except for the support supplied by the strength of the sealant.
With the dead load test, a sealant’s ability to resist shear forces exerted by dead loading after the “tack-free” condition has been achieved is tested. Since some sealants do not gain full adhesive properties until after achieving a tack-free state, it is important to know when IGUs are stable and ready for handling, packing, shipping, and storage. The test also verifies a sealed IGU’s ability to withstand the dead-loading conditions that can occur with installation.
To perform the test, a cured, tack-free 101.6 x 101.6 mm (4 x 4 in.) IG sample, comprised of two lites of 3 mm (0.125 in.) glass and 12 mm (0.5 in.) of air space is placed in a dead loader. Then, a 10 kg (22 lb) platform and plunger assembly are placed on top and left for 10 minutes.
The movement of the unsupported lite is recorded in millimeters (or inches), and the adhesive characteristics of the sealant relative to the spacer and the glass are observed.
Creep
This creep test is needed to prevent an IGU from sliding or falling apart. It evaluates the ability of a hot-applied sealant to resist shear forces exerted by dead loading.
Sealant is placed onto a clean 25.4 x 75.2 x 6.4 mm (1 x 3 x 0.25 in.) glass substrate in a 191 C (375 F) oven for 10 minutes. Immediately after removing the specimen from the oven, the second glass substrate is placed on the sealant to produce a 25.4 mm (1 in.) overlap. Using a shimmed template, pressure is applied to produce a sealant thickness of 1.6 mm (0.063 in.).
After conditioning the specimens for 16 hours at 23 ± 1 C (73 ± 2 F), 50 percent ± 5 percent RH, a 1 kg (2.2 lb) weight is attached to one specimen and hung vertically for seven days.
The second specimen has a weight attached and is hung in a forced draft oven at 49 ± 3 C (120 ± 5 F) for seven days. The procedure is then repeated in a 70 ± 3 C (158 ± 5 F) oven with a third specimen. A 1 kg (2.2 lb) weight is attached to a fourth specimen and then hung in a forced draft oven with the temperature increased at 1 C (1.8 F) per minute until bond failure is observed.
In addition to recording the observations, as with the dead load test, each specimen should be recorded with the mode of failure, i.e. adhesive, cohesive,
and film.
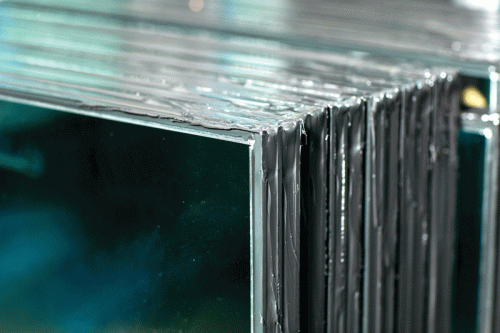
Overlap shear
This test is also critical to preventing sliding or deterioration. An overlap shear test measures the adhesion of sealants to 25.4 x 127 x 6 mm glass (1 x 5 x 0.25 in.) and 127 x 15.8 mm (5 x 0.625 in.) aluminum and galvanized steel spacers and their shear strength (#).
For this test, the mixed sealant is applied glass to glass and spacer to spacer, utilizing galvanized steel spacers and aluminum spacers. The assemblies are cured per the sealant supplier’s recommendations. Then, the specimens are mounted to a tensile tester and pulled in opposite directions at 50.8 mm (2 in.) per minute.
The overlap shear strength in pounds per square inch (PSI) or MPa is calculated as the maximum load (N or lbf) divided by the bonded area (mm2 or in.2). Types of test failure include cohesive or adhesive.
Overlap shear alternate method
With the overlap shear alternate method, the procedure for preparing the specimens is the same as the overlap shear test. The difference lies in the size and type of the metal substrates. Instead of 127 x 15.8 mm (5 x 0.625 in.) galvanized steel and aluminum spacers, 25.4 x 76.2 x 6 mm (1 x 3 x 0.25 in.) metal strips of #5052-H32 alloy aluminum or galvanized steel are used for the alternate method specimens.
Sealant adhesion
Adhesion is the glue that keeps the whole IGU together. In the absence of strong adhesion, air, water, and/or moisture can penetrate and cause eventual failure or even cause the unit to fall apart. Knowing how the sealant interacts with the other parts of the IGU ensures its adequate performance.
Sealant adhesion can be evaluated by tensile peel strength, with the hand peel method or with 180-degree angle peel adhesion tests.
Tensile peel strength
The glass panels and aluminum strips should be thoroughly cleaned and dried before setting up the tensile peel strength primary test method.
The sealant is mixed and then applied over half the length of the 25.4 x 127 x 3-6 mm (1 x 5 x 0.125-0.25 in.) glass strips. Additional sealant is then applied to the glass, and 25.4 x 203.2 x 0.125- 0.25 mm (1 x 8 x 0.006-0.010 in.) aluminum strips are placed over it.
Bars are placed on either side of the prepared panel so that when a metal rod is rolled over them and the aluminum strip, enough pressure is exerted to eliminate air voids, assure good sealant contact, and provide a sealant thickness of 0.5 mm (0.020 in.).
The panels are then placed in a 49 ± 3 C (120 ± 5 F) oven for two to three hours, then removed and left at ambient conditions for 24 hours. Afterward, they are placed in the tensile testing machine and pulled at a rate of 50.8 mm (2 in.) per minute. Results in N-m (lb/in.) width and percentage of adhesion loss are recorded.
The test also provides an option for long-term exposure evaluation. After preparing 18 peel adhesion panels as described above, six are set at standard room temperature conditions, another six are placed at 70 C (158 F) to test for thermal stability, and the remaining six at 49 ± 3 C (120 ± 5 F) with greater than 95 percent RH to test for moisture resistance.
Panels are checked after two days, 15 days, and 30 days and recorded for peel strength in N-m (lb/in.) width, type of failure, and to what surface, as applicable.
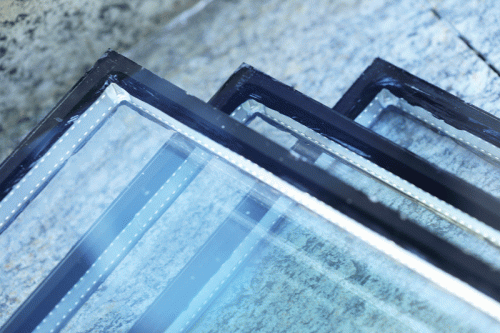
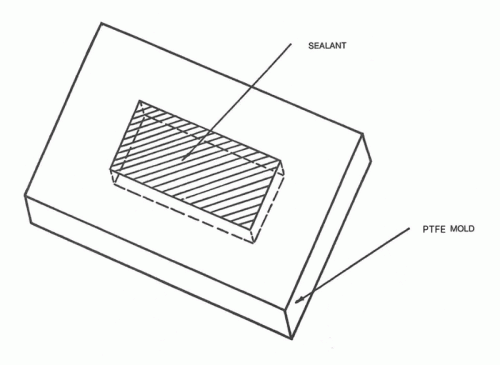
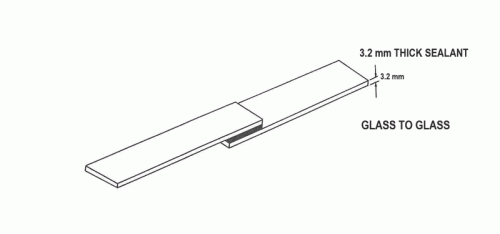
Hand peel method
The hand peel method, a secondary test method, describes a procedure for qualitatively determining the peel adhesion properties of a sealant to glass and metal.
With a spatula, a patty of sealant is applied to the 76.2 x 76.2 x 6 mm (3 x 3 x 0.25 in.) glass panel sample at about 50.8 to 63.5 mm (2 to 2.5 in.) square by 6 mm (0.25 in.) thick. The top surface is smoothed so that complete contact with the glass surface is attained with no bubbles or voids.
Next, a 50.8 mm (2 in.) section of the 76.2 to 101.6 mm (3 to 0.75 in.) long metal spacer is embedded in the patty, with the balance of the spacer section protruding beyond the edge of the patty to serve as a handle. The test specimen is then cured for 24 hours.
To test adhesion to the metal, the spacer section is lifted or twisted to apply tension to the band area. Then, the adhesion failure and the effort used to affect the spacer’s movement are noted.
During the test, a razor knife is used to cut through the patty two parallel cuts about 6 mm (0.25 in.) apart across the length of the patty. At one end of the 6 mm (0.25 in.) section, the razor blade is run under the patty to produce a tab of sealant free from the panel. The tab is then used as a grip, and tensile peel tension is applied to the sealant. Again, adhesion loss and the effort used to affect movement should be noted.
This procedure can also be used to evaluate adhesion after various specimen conditioning procedures, such as high temperature, water immersion, UV, and UV with water exposure.
180-degree peel adhesion
The 180-degree peel adhesion primary method evaluates the peel strength of a hot-applied sealant on glass, aluminum, or galvanized steel.
The sealant, measuring approximately 25.4 x 63.5 x 3.2 mm (1 x 2.5 x 0.125 in.), is placed onto a glass substrate 25.4 x 152 x 6.4 mm (1 x 6 x 0.25 in.) and metal substrates of #5052-H32 alloy aluminum or galvanized strips, 25.4 x 152 x 0.6 mm (1 x 6 x 0.025 in.).
After conditioning for 10 minutes in an oven at 191 ± 3 C (375 ± 5 F) and removed, a wire cloth is placed onto the sealant. Using the shimmed template, the specimen is pressed to embed the wire cloth and produce a sealant thickness of 1.66 mm (0.063 in.). The sealant is then trimmed from the edges to create a 25.4 mm (1 in.) uniform width. All specimens are then conditioned for at least 16 hours at room temperature before testing.
Samples are placed in a tensile tester and pulled in a 180-degree peel fashion at a rate of 50.8 mm (2 in.) per minute. The results are recorded as the maximum peel strength N-m (lb/in.), and the mode of failure is specified.
Optional long-term exposure testing can be conducted. Four specimens are placed at room temperature conditions, four are conditioned to
70 ± 1 C (158 ± 2 F) in a thermal stability test, four are set at 38 ± 1 C (100 ± 2 F) with 100 percent relative humidity to measure water vapor resistance, and four are conditioned to 1.6 ± 1 C (35 ± 2 F) in water for a moisture resistance test.
Two panels from each group are checked after three days and then after 30 days. The maximum peel strength (N/mm or lb/in.) and the mode of failure results are recorded.
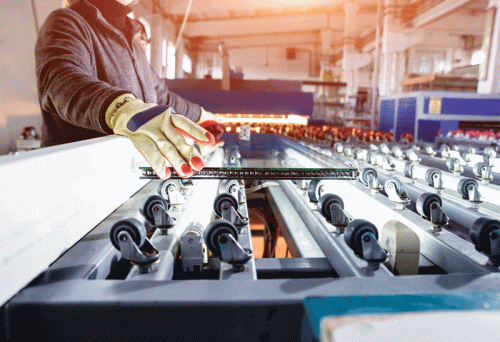
In summary
A high-quality, well-constructed building envelope system is key to enjoying daylighting, energy efficiency, occupant comfort, enhanced productivity, and health and wellness of building occupants. IGU systems are a key contributor to supporting that high-performing building system.
To best ensure this, IGUs and their sealants must be thoroughly tested and evaluated so that their performance characteristics are well known.
Author
Amy Becker is the Fenestration and Glazing Industry Alliance’s (FGIA’s) glass products specialist. She oversees the operation of the Insulating Glass Certification Council and Insulating Glass Manufacturers Alliance (IGCC/IGMA) and the Insulating Glass Manufacturers Association of Canada (IGMAC) insulating glass certification programs. Additionally, Becker serves as the internal auditor for FGIA fenestration certification programs. With more than 20 years of industry experience, she is also a staff liaison for glass-focused committees and task groups. She represents FGIA and its members at meetings of other industry organizations. She can be reached at abecker@fgiaonline.com.
Key Takeaways
High-performance facades begin with high-performing glass, making insulating glass units (IGUs) essential to glazing systems. IGUs play a significant role in improving energy efficiency, aesthetics, and occupant wellness by controlling solar heat gain and optimizing natural daylight. However, to maximize these benefits, proper IGU production, sealing, and material testing are critical in preventing failure and prolonging the system’s lifespan. The Fenestration Glazing Industry Alliance (FGIA) has introduced updates to its IGMA TM-2400 standard, outlining rigorous sealant testing methods. These methods assess key qualities such as tack-free time, moisture vapor transmission, and shear strength. This article examines industry standards and highlights testing procedures that ensure IGUs meet the necessary performance benchmarks for high-performing building envelopes.