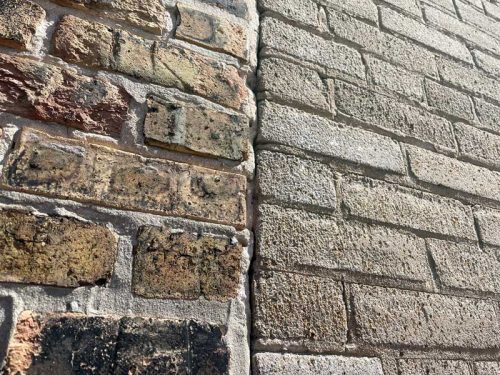
Not all bricks are created equal, and not all bricks are even created from the same material. While most bricks are made of fired clay, calcium silicate (or sand-lime) bricks are made by mixing lime with silica sand, which is then pressed into the desired shape. The molded units are then cured in a steam autoclave. Calcium silicate bricks are defined under ASTM C73, Standard Specification for Calcium Silicate Brick (Sand-Lime Brick).
Calcium silicate bricks were particularly popular in the 1910s and 1920s and remain available in the marketplace today (Figure 1). Unlike clay bricks, which vary in color and may warp during the firing process, calcium silicate bricks are typically very uniform in color and size. While often visually similar to clay masonry units, the material properties of calcium silicate bricks are somewhat different.
Key design considerations include the following:
- Absorption—As defined in ASTM C73, Grade SW (severe weathering) calcium silicate bricks are permitted to have a maximum water absorption of 240 kg/m3 (15 lb/cf), which is similar to the limits defined in ASTM C216 for clay bricks. Calcium silicate bricks typically have moderate absorption; as with clay masonry, thoroughly wetting the bricks as they are laid up or repointed is desirable to ensure a good mortar bond.
- Control and expansion joints—Unlike clay masonry, calcium silicate bricks do not experience long-term clay expansion. Therefore, the design of expansion joints does not need to consider any irreversible material expansion. However, control and expansion joints are still required to accommodate cyclical thermal movements, following the same design principles as clay masonry. If a mixture of materials is used in the design, appropriate joints should be included to isolate the different materials, considering the differential movement between calcium silicate and clay units.
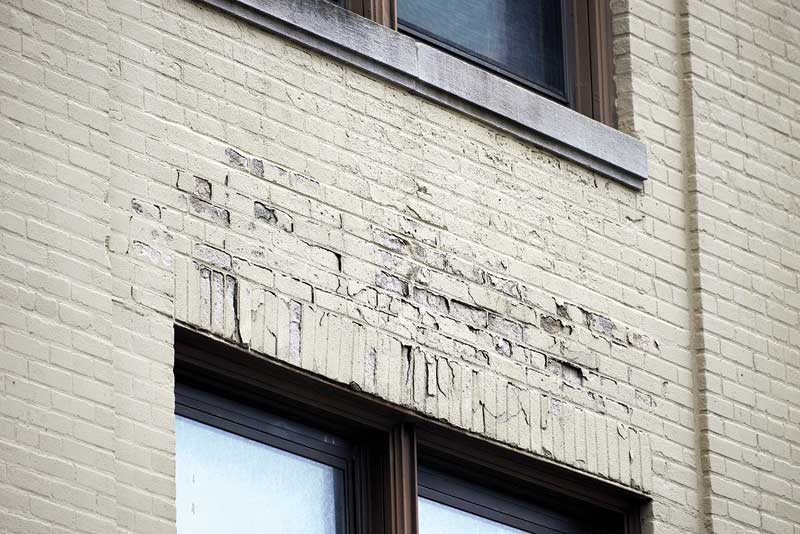
- Coating—Film-forming coatings are generally undesirable with clay masonry, and only highly breathable coatings should be considered. With calcium silicate bricks, surface coatings—including both film-forming coatings and water-repellant sealers—are unnecessary and can be damaging. In a recent project, even a somewhat breathable coating on calcium silicate brick was associated with freeze-thaw damage and face spalling of the bricks (Figure 2).
- Cleaning—In new brick masonry construction, cleaning products containing aggressive acids, such as hydrochloric acid, are often used to clean the completed masonry and remove mortar smears from the face of the units. With all masonry, this practice should be avoided to prevent deterioration of mortar, future efflorescence, or deterioration of embedded metal components. It is even more critical to avoid the use of aggressive acidic cleaners with calcium silicate masonry, as these chemicals can dissolve or discolor the brick.
Considering the material’s properties, proper design and installation can ensure the next generation of calcium silicate masonry provides the same durable performance seen in historic structures.
Author
Kenneth Itle, AIA, is an architect and associate principal with Wiss, Janney, Elstner Associates (WJE) in Northbrook, Illinois, specializing in historic preservation. He can be reached at kitle@wje.com.
Nikki Byl and Ariel Kousgaard of WJE also contributed to this article.
The opinions expressed in Failures are based on the authors’ experiences and do not necessarily reflect that of The Construction Specifier or CSI.