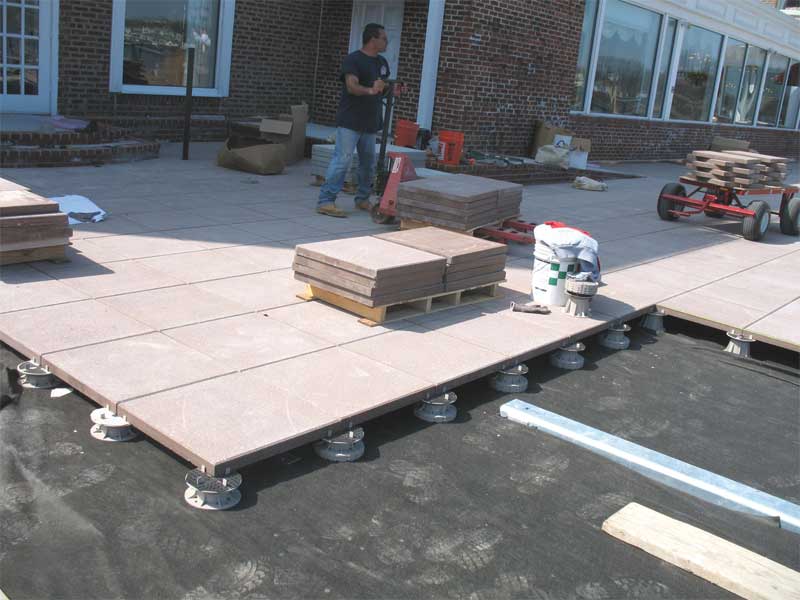
by Justin Henshell, FAIA, FASTM
Non-stop increases in urban land costs have led to more efficient use of space by building owners. This includes not only building upward, but also downward. Waterproofed plazas over occupied underground facilities and roof terraces (sometimes called waterproofed decks) became popular ways of maximizing both horizontal and vertical space. Underground spaces were once limited to storage areas, access tunnels, and parking garages. However, with the advent of air-conditioning, they became suitable for computer server rooms, offices, and public-assembly rooms. City planners encouraged architects and building owners to provide plazas as a means of expanding open space in crowded cities.
This article outlines the evolution of waterproofing plazas and terraces designed for pedestrian and light vehicle use over occupied spaces. It should prove useful to designers and waterproofing manufacturers who seek to avoid repeating the failures of the past. (This author is indebted to Dean Rutila, senior principal at Simpson Gumpertz & Heger [SGH] Engineers for reviewing the manuscript and contributing his insights gained in over 15 years of designing and investigating plaza deck waterproofing. As plaza waterproofing is in constant flux, this author would also appreciate any corrections or updating readers may have.)
The built-up bituminous membrane era
Prior to World War II, waterproofing over below-grade occupied spaces consisted of a built-up membrane of alternate layers of hot coal tar pitch reinforced with tarred rag and jute felts. The felts were assembled in a one-on-one or ply-on-ply system, usually applied as a two-or three-ply (sometimes shingled), then covered with two additional plies (Figure 1). Membranes were often surfaced with a pour coat of hot coal tar pitch prior to the placement of a concrete wearing course or the installation of quarry tile on a cement setting bed.
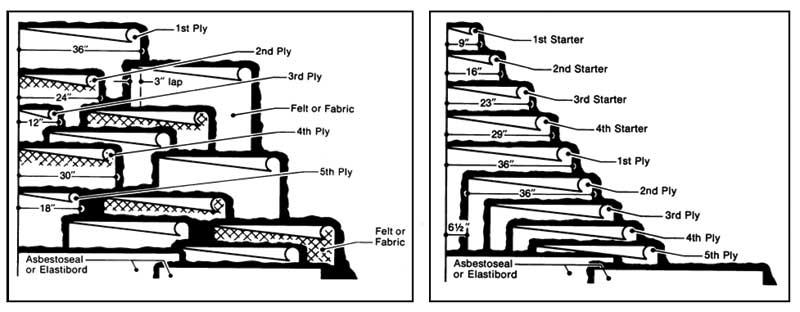
Image from Philip Carey Co. Waterproofing Catalogue, 1971
The wearing surface, which was exposed to the elements, moved in response to ambient temperature changes. As it was bonded directly to the membrane, it often produced inplaner stresses at the interface between the two. In winter, these stresses would cause splitting of some of the plies closest to the surface. However, they would reseal themselves because of the cold-flow properties of the coal tar pitch. The self-healing qualities were enhanced by heat from the space below, which kept the membrane warm. Heating oil and coal were inexpensive, so slabs were not insulated.
Coal tar pitch has low viscosity, and softens easily. Its ability to flow under all temperatures and heal itself is one of its most beneficial physical/chemical properties. This self-healing quality and superior water resistance made it the ideal membrane for use on plazas over occupied spaces in that era. Pitch and pine tar were also known for their water-resistant properties—in their many forms, they had been used for centuries to caulk the wood hulls of ships.
Coal tar pitch was produced as a residue (called ‘destructive distillation’) when coal was fired in closed vessels in the absence of air in order to make coke. Coke was an important constituent in the manufacture of blast-furnace steel. Roofing and waterproofing manufacturers refined this residue to produce waterproofing and roofing bitumens, as well as creosote.
Coal tar pitch was also used to waterproof basement walls subject to hydrostatic pressure. Foundations were constructed using bricks dipped in hot coal tar pitch to form a waterproof masonry wythe, against which the concrete foundation wall was cast.