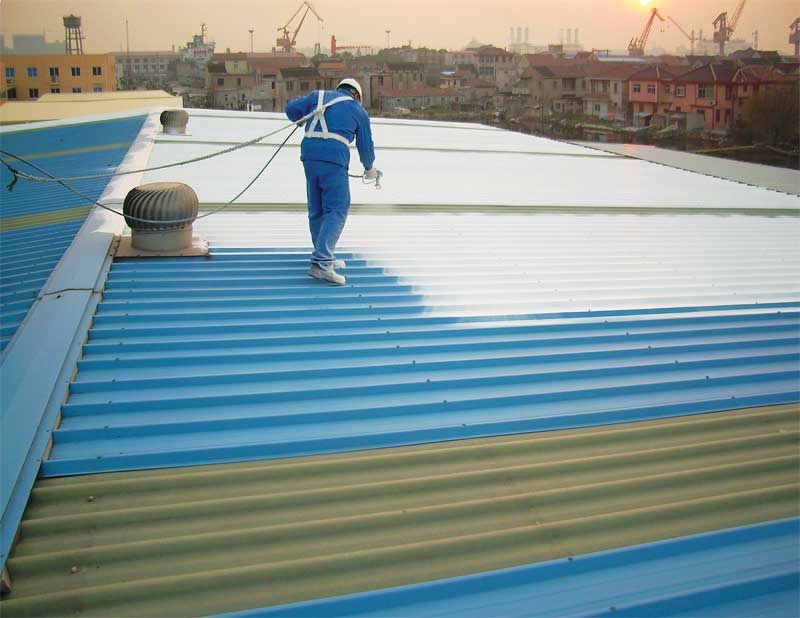
by Steven Heinje
What are the differences between paints and roof coatings, and what are liquid-applied membranes? Which material is ideal when an existing roof is not in a leak-free condition? This article seeks to define these products and systems in order to establish guidance for their correct selection and use, and to identify what factors favor specifying a liquid-applied solution versus a prepared roofing solution.
Paints, coatings, and liquid-applied membranes are all polymer-rich, and share a few key attributes. They are usually based on resins possessing very good weathering resistance, and are frequently cross-linked in some fashion to confer toughness and chemical resistance. They are somewhat over-engineered to compensate for the vagaries incumbent with field application.
In basic terms, a paint is a finish where cosmetics are typically a primary attribute. Surface protection may also be a key selling point, but paint must look good. Sold in specific sheen levels and in a broad range of colors, it usually has limited flexibility, but its hardness provides for exceptional weathering and colorfastness in a thin film.
Coatings, on the other hand, are films used to provide surface protection or other resistance properties. Color range and appearance are determined completely by performance considerations. A coating generally has an elongation greater than 100 percent and good low-temperature flexibility, is high in solids, and requires a thicker film to achieve long-term weathering and waterproofing.
The third category, liquid-applied membranes, are fully reinforced systems comprising a fabric and one or more coatings or resins. They are used to encapsulate and adhere the reinforcement.
Paint applications
In roofing, paint applications are almost exclusively used on steep-slope metal systems for aesthetic or reflective purposes. When metal comes painted from the factory, it is called an original equipment manufacturer (OEM) paint; these baked metal finishes are usually more durable than an aftermarket maintenance coating. Although not intended to improve the water shedding of the roof system, a metal roof may still benefit from the corrosion-inhibiting, temperature-reducing, and eye-appealing properties of a paint job.
Steep-slope metal roofs are often important architectural details. Bare metal, despite its luster, has only moderate solar reflectivity and fairly poor emissivity, so it gets very hot. All paints, even dark ones, allow more heat to escape the metal, lowering the roof’s peak temperature. Paints with deep colors can employ special pigments that absorb less heat from the sun. Most white roof paints are rated for their solar reflectivity and emissivity. Together, these values will produce a Solar Reflective Index (SRI) that can predict the peak surface temperature.
In terms of cool roofing, there can be no better improvement for metal than applying a white coating to a rusting roof. Often, these roofs are not well-insulated—as they rust, they become less reflective, holding and conducting heat into the building. This dramatically increases the load on air-conditioning. Ultimately, paint can be seen as the first step in a long-term maintenance program that might later involve coatings or membranes.
Coating applications
Today, most coatings are based on acrylic, silicone, or urethane resins—all seek to extend the existing roof’s service life and, as a rule, prevent water intrusion. This requires a much higher degree of crack-bridging than found in paint. A coating must be able to protect a number of transitions subject to cyclical movement, such as:
- flashing to the membrane;
- flashing to the structure;
- joints at protrusions and curbs; and
- any seams within the membrane.
This implies there must be an appropriate degree of low-temperature flexibility, substantial elongation, and a thick film. A coating should never be used to overcome a structural issue and, while they must tolerate movement, coatings cannot overcome the limitations of an improperly engineered roof system.
Although many coatings are sold as part of a cool roof solution, it is important to recognize they should not be selected in the same way one would choose a paint (i.e. solely considering appearance or reflectivity). A coating should provide robust barrier properties, starting with increased water resistance, and often include some combination of chemical resistance (e.g. plasticizers, oils, and stack emissions) and resistance to abrasion, impact, or vapor intrusion (e.g. water, oxygen, and carbon dioxide [CO2]).
Typically, coatings properties include tensile and elongation, which are usually reported at standard temperature and humidity. Crack-bridging is the key to performance; it is a function of elongation at a low temperature, tear strength, and film thickness.