
by Ivan Diaz-Loya, PhD
With evidence of climate change bringing awareness to greenhouse gas (GHG) emissions, the sticking point for concrete construction is the amount of embodied carbon in the material. Most of this embodied carbon comes from production of portland cement—the fine powder that hydrates and ‘glues’ sand and stone together to produce concrete.
Approximately 600 kg (1322 lb) of carbon dioxide (CO2) is released into the atmosphere for every ton of cement produced.1 This may not sound like much, but when the expected global cement output is 3.4 billion tons for 2013, it means roughly 2 billion tons of CO2—five percent of all manmade GHG emissions—will be released to the atmosphere as part of the cement production process.2
To bring this to the specifier’s perspective, when a cubic yard of portland cement concrete is specified to have a cement content of 249 kg (550 lb), that cubic yard of concrete already has around 149 kg (330 lb) of embodied carbon generated from cement production alone.
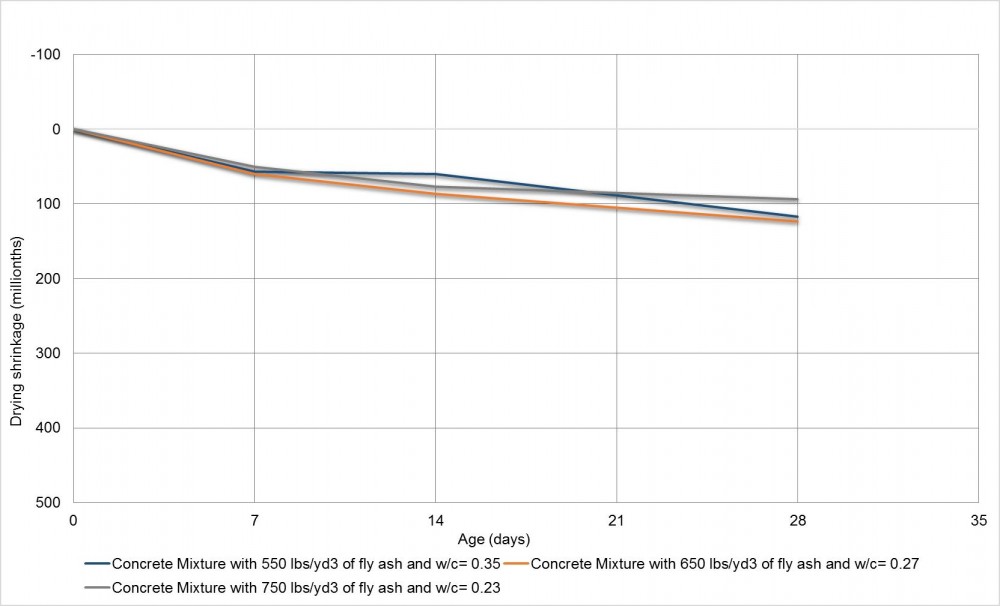
Concrete carbonation
Part of these emissions is recaptured throughout the concrete’s life when hydrated portland cement reacts with the CO2 in the atmosphere to form calcium carbonate—a process called carbonation. However, it is uncertain how much CO2 is reabsorbed into the concrete. Washington State University’s associate professor Liv Haslebach states in the article, “Concrete as a Carbon Sink,” published on Portland Cement Association’s (PCA’s) website, that although there have been numerous studies, no one has been able to put an accurate number to the amount CO2 recaptured though carbonation.3
A 2007 study by Claus Pade and Maria Guimares, “The CO2 Uptake of Concrete in a 100-year Perspective”, estimates the amount of CO2 recaptured through carbonation is between 33 to 57 percent over a century.4 Whatever the actual number, it only stands to reason by the time the hydrated cement in concrete fully carbonates, the structure will have reached the end of its service life, and another structure will be built using more portland cement concrete to replace the old one. Therefore, even in a perfect scenario where 100 percent of the CO2 is recaptured through carbonation and no new growth occurs, a revolving amount of CO2 is being maintained in the atmosphere as old structures decay and new ones are built.5
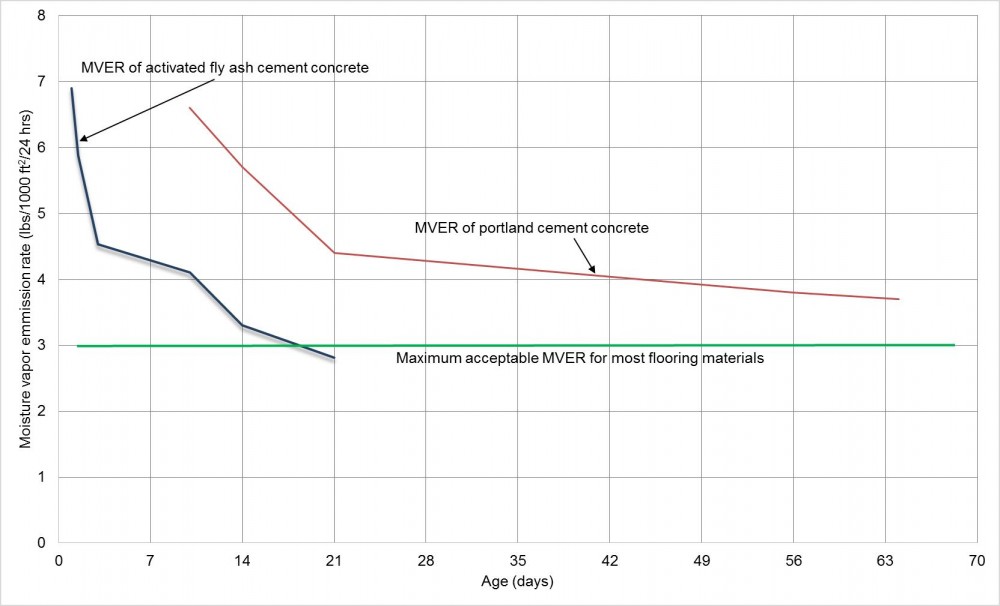
Alternative binder systems
PCA calls portland cement the “building block of the nation’s construction industry.” While portland cement will likely continue to be used for generations, there are alternative binder systems available for the production of concrete. One of these alternatives is fly ash—the fine powder filtered out from the flue gases resulting from the combustion of coal. Fly ash is typically rich in silica, alumina, and calcium oxide (CaO) in many cases. During the power production processes, fly ash moves rapidly from combustion to room temperature, forming tiny spheres composed mainly of reactive glass; the material has an appearance and fineness similar to portland cement.
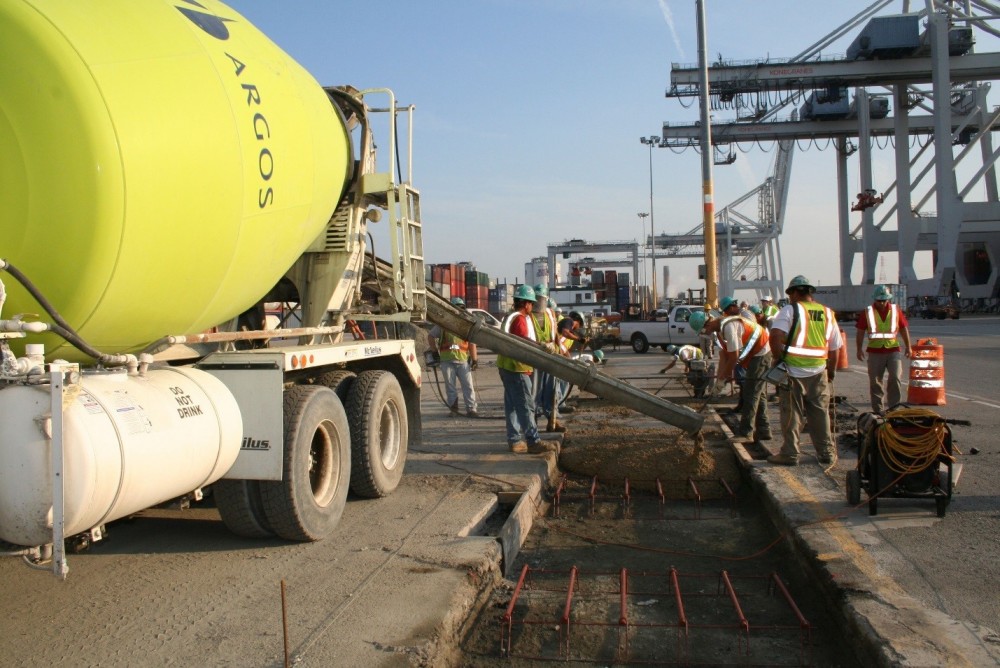
Fly ash can be easily activated using a small amount of alkalis in the form of hydroxides or pH-neutral hydro-carboxylic acid salts to form a strong and durable binder that can replace portland cement in the production of concrete. Although fly ash has long been used to partially replace portland cement (sometimes up to 30 percent), total replacement of portland cement virtually eliminates all greenhouse gas emissions associated with the production of the cementitious binder in concrete.
Fly ash is typically produced from the combustion of coal to produce electricity, less than 35 percent of which is repurposed for beneficial use. The “2011 Coal Combustion Product (CCP) Production and Use Survey Report,” released by the American Coal Ash Association (ACAA), recorded only 23 million tons of fly ash were reused out of the 60 million tons produced in 2011.6 As such, approximately 37 million tons of fly ash could have been employed to produce activated fly-ash cement concrete instead of being sent to landfills. While some of this fly ash may have been lower quality, much of it could have been blended with high-quality material rather than disposed of.
Benefits of activated fly-ash cement
Activated fly-ash cement concrete not only offers environmental benefits, but also performance benefits, including:
- improved volume stability;
- mix design flexibility;
- high early strengths;
- low water vapor transmission at early ages; and
- resistance to corrosive and high temperature environments.
Mix design flexibility
Concrete mixtures using activated fly-ash cement are proportioned in the same way as their traditional counterparts; in many cases, they even follow the same guidelines given by the American Concrete Institute (ACI). After all, it is still concrete with only the powder being different. The main difference is the addition of the activating liquid; at typically less than 24,815 mL/m3 (5 gal/yd3) of concrete, it is less than two percent of the total volume of the concrete mixture.
The type of activator may vary, but sodium hydroxide and sodium silicate are typically used in combination to activate low or moderately low calcium fly ash (i.e. <15 percent CaO). Hydro-carboxylic acid salts, which have a pH close to neutral, can be used for fly ash with higher calcium contents. Since portland cement mixtures can have a pH higher than 13, concrete practitioners are already accustomed to the level of alkalinity that fresh sodium hydroxide/sodium silicate-activated fly-ash mixtures can exhibit.
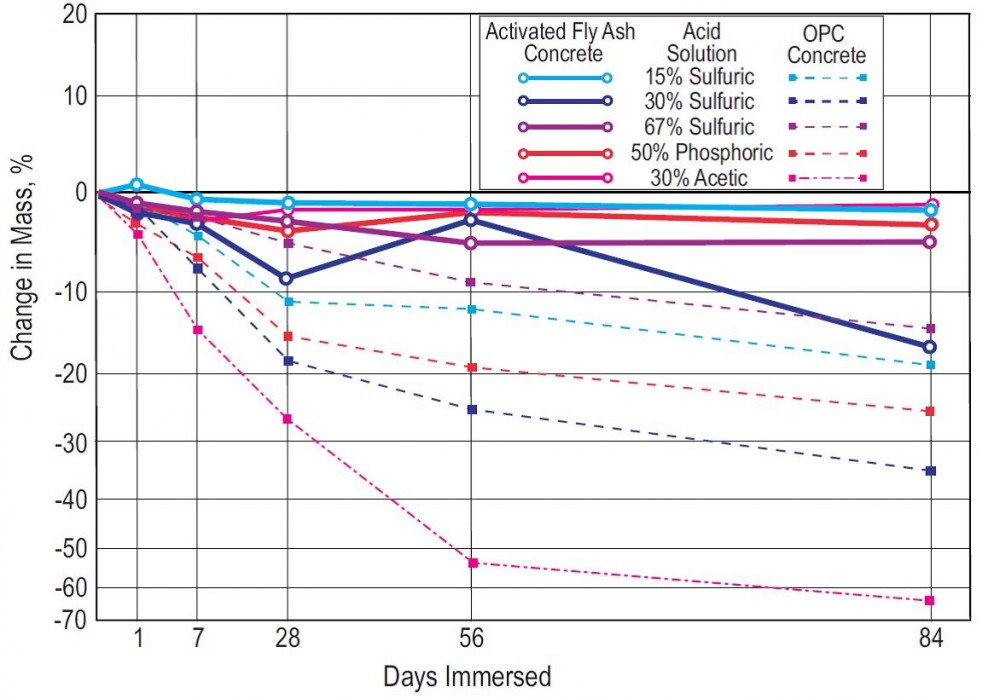
Nevertheless, handling concentrated solutions, especially of sodium hydroxide, may be challenging to certain ready-mixed concrete operations because of its high alkalinity. Hydro-carboxylic acid salts on the other hand, are neutral by pH and produce fresh activated fly ash cement concrete with a pH of around eight. Once the concrete hardens, the pH raises to around 12, which is necessary to protect reinforcing steel from corrosion.
Hydro-carboxylic acid salts activate (or modify) high calcium fly ash by allowing the formation of a solution equilibrium, and the solubility of fractions of the fly ash that do not normally react when mixed with water alone. Then, when calcium aluminosilicate hydrates nucleate and grow, they produce a predictable set time and normal, but accelerated, strength development.
Volume stability
Another benefit of using fly-ash cement is the reduction of water necessary to achieve workable concrete mixtures compared to portland cement mixtures. This allows for fly-ash cement concretes with low water-to-cementitious (w/c) ratios, and the main reason the concrete exhibits low drying shrinkage. Drying shrinkage values of activated fly-ash cement concrete range from 100 to 300 millionths, while regular concrete values range from 400 to 800 millionths after 28 days. This important feature reduces the potential for cracking and can speed up construction times for concrete flatwork and foundations.
Vapor emission rates at early ages for floorcoverings
For floorcoverings and coatings applied over concrete, activated fly-ash cement offers a tremendous advantage given its inherent rapid drying. When flooring materials are applied over concrete with high moisture vapor emission rates (MVER), moisture can condensate beneath the floor covering and dissolve the alkalis in concrete, raising the pH. These conditions can break down the adhesive and cause failures in the flooring such as blistering and delamination. Months can pass from the time the concrete is placed until it has acceptable MVER levels (typically 1.45 kg/100 m2 [3 lb/1000 sf] daily) to apply a low MVER floor covering. This can leave installers with the choice of meeting the construction schedule or waiting for the concrete to dry. Activated high-calcium fly-ash cement concretes do not require wet curing and dry quickly, allowing flooring systems with the most stringent placement requirements to be placed in less than three weeks.
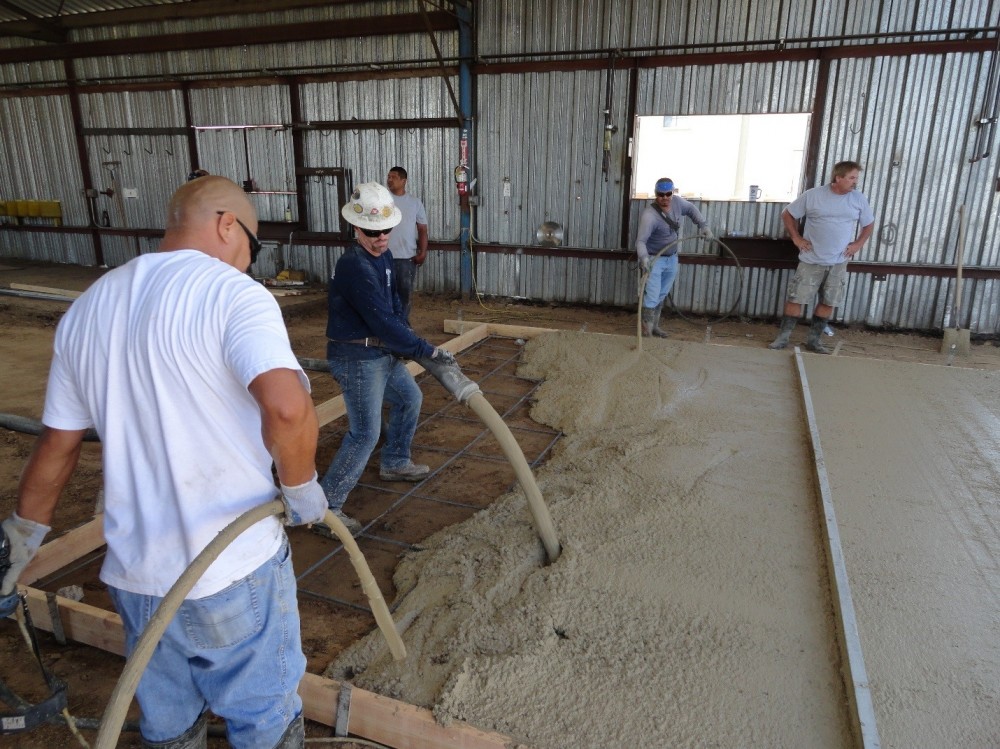
Resistance to corrosive acids
Activated fly-ash cement concrete also offers high chemical resistance, mainly due to a combination of two factors:
- its low w/c ratio, which can be 40 to 50 percent less than typical portland cement mixtures, resulting in a denser concrete (approximately 80 kg/m3 [5 lb/y3] more than portland cement concrete) that restricts the ingress of destructive agencies; and
- calcium in activated fly-ash cements is combined in a less soluble form than in portland cements.
Portland cement concretes contain a high proportion of calcium hydroxide, which is highly soluble in most acids. This causes the material to quickly decompose. Conversely, activated fly-ash cement concretes have no excess calcium hydroxide, making them more resistant to corrosive acids.
Resistance to heat and temperature changes
The reaction products of activated fly-ash cements decompose at higher temperatures than those of portland cement, making them able to withstand such conditions. Additionally, because the overall thermal properties of concrete also depend on the characteristics of the aggregate being used, it is important how heat travels into, and through, the material.
Many heat-related failures in concrete happen not because hydration products decomposed, but rather due to temperature changes in the structure, which create a tremendous amount of thermal stresses. An example is when a heated glass jar bursts when exposed to ice-cold water. The higher density of activated fly-ash cement generates two important changes in the thermal properties of concrete: higher heat capacity and thermal conductivity.
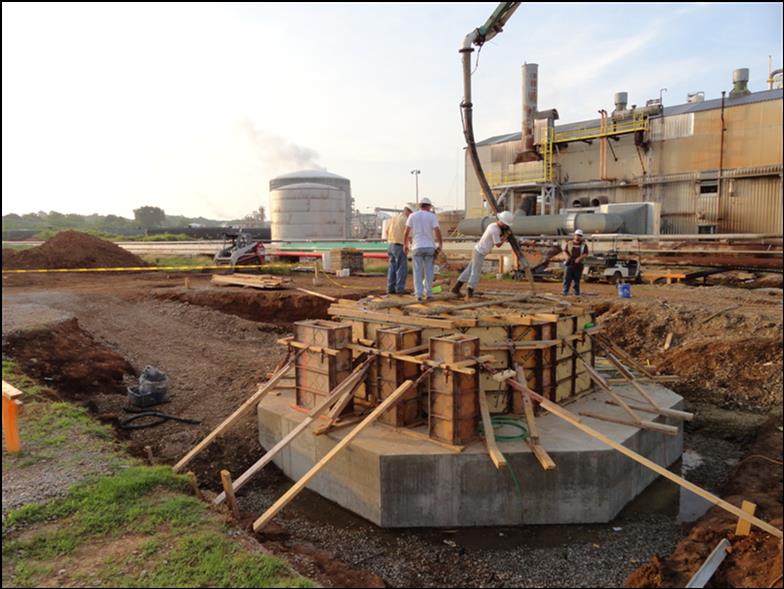
Although low thermal conductivity is one of the most sought-after features in most construction materials, it is not as desirable in more brittle (and thus thermal stress-susceptible) materials like concrete. Activated fly-ash cement concretes absorb heat more slowly, and dissipate heat more rapidly through its concrete structure than portland cement concrete because of thermal conductivity which effectively reduces the thermal stress on the concrete. For example, an activated fly-ash cement concrete slab raises its temperature more uniformly, having a lower temperature gradient between the top and bottom of the slab. These features are not only desirable in high temperature exposure applications, but also in regular concrete flatwork applications as they minimize the potential for curling and cracking caused by daily temperature fluctuations.
In the past, activated fly ash cement concretes were only accomplished in highly controlled lab conditions and were impossible for field applications. While this perception still remains for many, the reality has changed. Activated fly-ash cement are now being used as a one-for-one replacement for portland cement concretes in many applications.
In 2009, Missoula Federal Credit Union (MFCU) built the first Leadership in Energy and Environmental Design (LEED) New Construction (NC) v2.2 Platinum-certified building in Montana using 100 percent fly-ash concrete (i.e. portland cement-free) as the main building material. The concrete mixture incorporated recycled glass as aggregate, and was used to build the footings, foundation walls, floor slabs, interior components, column surrounds, and roof beams. Montana State University developed the concrete mixture and worked with local contractors and architects to design and build the new branch office for MFCU. Researchers at Louisiana Tech University have also been running field tests since 2008 to create confidence in activated fly-ash cement concrete.
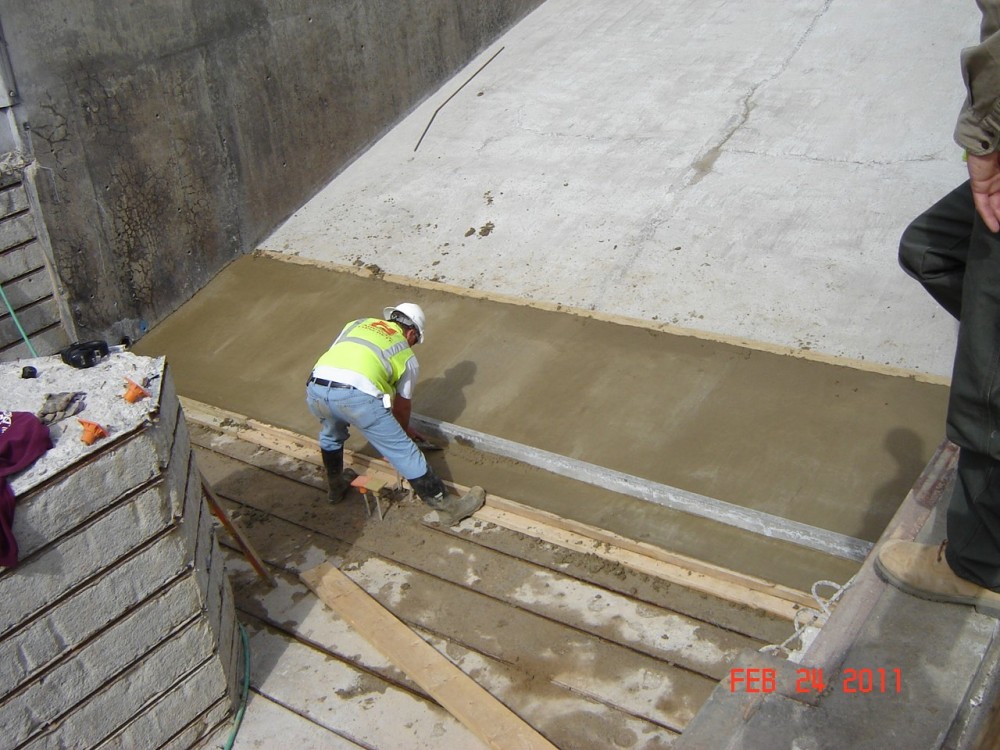
These ingredients can be easily introduced to existing ready-mixed concrete plants. Activating liquids can be plumbed into the plants in the same way most admixtures are currently used and given most plants already have a dedicated silo for fly ash, there is no need for setting up additional storage for it. Leading designers and specifiers have started taking notice of the capabilities and advantages activated fly ash cement concretes provide to their clients.
In July 2012, the Georgia Ports Authority used activated fly-ash cement to replace part of the lane where overhead mobile gantry cranes operate in the Port of Savannah. The Federal Highway Administration (FHWA) is now looking at the potential use of activated fly-ash cement concrete in rigid pavements and other transportation structures by signing cooperative research agreements (CRADAs) with leading producers of activated fly-ash concrete.
The Department of Defense (DOD) has also been using activated fly-ash cement concrete regularly to the replace concrete slabs that receive impingement heat from vertical takeoff and landing aircraft. Military bases throughout the United States, and internationally, have successfully been using activated fly-ash cement concretes for more than a decade now in the construction and rehabilitation of surface and aviation transportation infrastructure.
![This graph shows typical strength development curves of concrete using high calcium fly-ash activated concrete with hydrocarboxilic acid salts as binder. [CREDIT] Data courtesy Patel et al’s, “Green concrete using 100 per cent fly ash-based hydraulic binder,” Proceedings of the 2012 Concrete Sustainability Conference (Seattle).](http://www.constructionspecifier.com/wp-content/uploads/2015/11/Typical-strength-development-curves-of-activated-fly-ash-concretes-1000x683.png)
Since activated high-calcium fly-ash cement relies on its hydraulic activity to harden and gain strength, it can be considered hydraulic—this a candidate for meeting ASTM C1157, Standard Performance Specification for Hydraulic Cement. Conversely, for fly ash with a lower calcium content—typically Class F per ASTM C618, Standard Specification for Coal Fly Ash and Raw or Calcined Natural Pozzolan for Use in Concrete—ASTM Committee C01 on Cement recently formed a task group to develop standard test method for testing compressive strength of alkali-activated fly ash and natural pozzolan cement. This test method is expected to be the base for the development of future specifications.
Conclusion
The current social and cultural forces shaping the construction industry are increasingly calling for materials in addition to meeting performance requirements and being produced with environmental responsibility. With regulations looming, it is difficult to predict what will happen in five, 20, or 50 years. On the bright side for fly ash, the EPA is now considering other options, none of which label the material as hazardous waste. 7
Activated fly-ash cement offers a solution by providing a value-added product while reducing the use of portland cement and associated emissions, and recycling a coal combustion product into beneficial construction materials, reducing landfill and disposal facilities.
Notes
1 For more information, visit www.globalcement.com/news/item/1806-decoupling-carbon-emissions-from-cement-production. (back to top)
2 Visit www.nature.com/news/green-cement-concrete-solutions-1.12460. (back to top)
3 Visit www.cement.org/tech/carbon_sink.asp. (back to top)
4 For more information, see Claus Pade and Maria Guimares’ “The CO2 uptake of concrete in a 100-year perspective” from the International Symposium on Sustainability in the Cement and Concrete Industry held in Lillehammer, Norway in 2007. (back to top)
5 For more, visit www.nrmca.org/greenconcrete/concrete%20co2%20fact%20sheet%20june%202008.pdf. (back to top)
6 Visit, www.acaa-usa.org/associations/8003/files/Final2011CCPSurvey.pdf. (back to top)
7 Visit www.epa.gov/epawaste/nonhaz/industrial/special/fossil/ccr-rule/ccrfaq.htm#3 (back to top)
Ivan Diaz-Loya, PhD, joined CeraTech Inc., in 2011 as a research engineer to help develop a better understanding of activated high-calcium fly-ash cement concrete. He holds a PhD in engineering from Louisiana Tech University, where his research focused on the material. Diaz-Loya is a member of American Concrete Institute (ACI) and ASTM where he chairs a task group developing a test method for compressive strength of alkali-activated fly ash cement mortars. He can be contacted by e-mail at ivan.diazloya@ceratechinc.com.