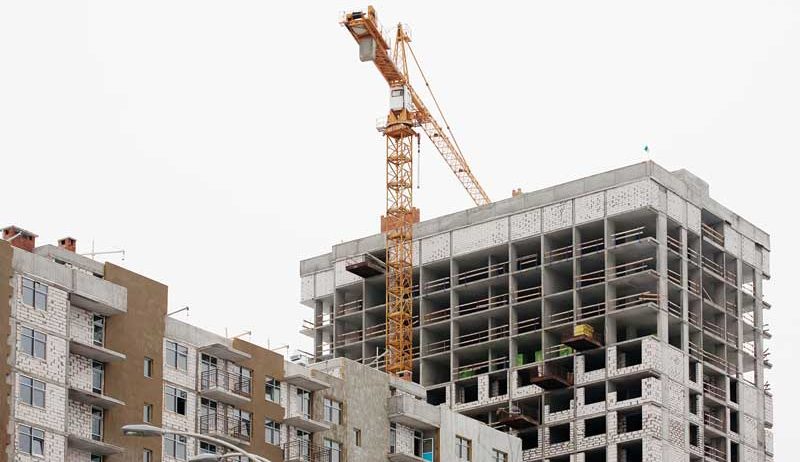
by Anthony Katona, CDT
Concerns with global warming and energy consumption mean design/construction professionals need a better understanding of how these topics affect commercial buildings. This article presents an overview of the effects U.S. model building and energy codes—along with industry standards—have on low-slope roofs (assembled with insulation above the roof deck) and exterior masonry walls. (The figures used in this article are believed to be true and accurate, but cannot be guaranteed. Some of the information comes from “Cutting through I-Code Confusion: A New R-value Guide for Roofs and Walls,” an Architectural Roofing and Waterproofing [BNP Media] article by James Hoff [Tegnos Research], sponsored by the Center for Environmental Innovation in Roofing (CEIR) and two product manufacturers. Visit here. It is important for design/construction professionals to always use their own judgment, and get the advice of independent professionals to find the right strategies for their business and their particular situation.)
The Polyisocyanurate Insulation Manufacturers Association (PIMA) defines continuous insulation (CI) as “insulation that is continuous across all structural members and is free of significant thermal bridging, other than fasteners and service openings. It is installed on the interior, exterior, or is integral to any opaque surfaces of the building envelope.” (This comes from PIMA Technical Bulletin [TB] 403, Continuous Insulation Using Polyiso Wall Sheathing. Visit here.)
It can be used with various structural wall systems and cladding materials such as cement board, stucco, brick veneer, and stone, among other wall finish materials. Further, the installation of CI can be placed on the interior or exterior side of the wall with proper consideration of climate-dependent moisture vapor control code requirements.
CI serves several important functions in high-performing roof and wall systems, offering continuous thermal insulation, moisture vapor control, weather-resistive barrier (WRB), and air barrier roles. Three of the benefits of using a CI insulation board material, such as polyisocyanurate (polyiso), include:
- increasing thermal performance by blocking thermal bridging;
- lowering operating costs by keeping heat loss to a minimum; and
- reducing air infiltration and exfiltration by taping or sealing the joints in the CI further restricts air movement throughout the wall assembly, which helps reduce building heat loss even more.
Additionally, the National Roofing Contractors Association (NRCA) asserts roof system manufacturers typically require all approved applicators to place the CI in two discrete layers on the exterior side of the roof deck in order to obtain their no-dollar-limit (NDL) warranties. Moreover, all rigid-insulation boards covering the roof deck must be staggered and offset a minimum of 150 mm (6 in.) in all directions. This installation procedure effectively eliminates thermal breaks that would occur if the edges of the top layer were in direct alignment with the bottom layer of insulation.
The U.S. Department of Energy (DOE) currently calls for CI or cavity plus CI not to be broken up by framing members. It is also possible to use CI alone to meet energy code requirements without any cavity insulation for the ultimate ‘warm
wall’ design.
Upgrading insulation amounts in our commercial buildings not only reduces energy use, but the added comfort also often translates into increased productivity for occupants, which can lead to higher occupancy rates. Further, choosing to upgrade existing buildings (i.e. improving the energy efficiency of roofs and walls) ultimately creates numerous jobs, typically improving local economies.
Advancements in energy efficiency
While improvements in energy efficiency are critical to the design of the next generation of sustainable buildings and renovations, there is still some confusion over options for the level of thermal performance. To begin with, the I-Codes now recognize two separate levels of thermal performance:
- a minimum code level in the International Energy Conservation Code (IECC); and
- an above-the-code level in the International Green Construction Code (IgCC).
Both IECC and IgCC offer two paths to determine roof and wall R-value. One is based on International Code Council (ICC) standards, while the other comes from the American Society of Heating, Refrigerating, and Air-conditioning Engineers (ASHRAE) standards. In previous editions, the resulting R-values from ICC and ASHRAE paths were frequently identical, but recent editions of I-Codes and ASHRAE standards contain significant differences.
It is important to know the 2012 IgCC no longer contains the traditional roof and wall R-value tables used in previous codes. Consequently, it may be difficult to determine the exact roof and wall requirement for a new building or renovation project.
As a rule, the U.S. model energy codes and standards (including both the 2012 IECC and also ASHRAE 90.1-2010, Energy Standard for Buildings Except Low-rise Residential Buildings) maintain providing an uninterrupted thermal barrier over entire roof and wall areas. Additionally, these prescriptive energy codes and standards call for providing an uninterrupted vapor barrier primarily when the geographic location of the building and climatic conditions support the installation (i.e. where applicable).
These energy codes and standards are essential requirements for commercial building construction because they virtually eliminate heat loss through studs, structural steel columns, steel joists, steel purlins, and any open joints in rigid-board roof insulation—otherwise known as thermal shorts or thermal bridging.
Good information. Very useful.