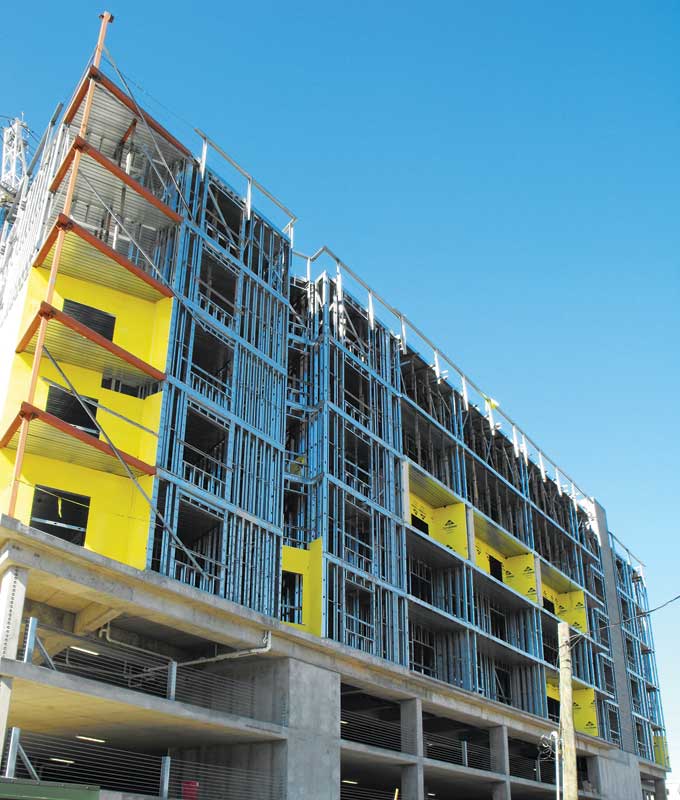
by Don Allen, PE, LEED AP, and Robert Wills, PE
Cold-formed steel (CFS) has been available in construction for more than a century, but some specifiers, architects, engineers, and other building professionals do not yet understand the full range of the material’s benefits and applications. Lightweight, strong, noncombustible, and easy to install, it is versatile enough to address many common obstacles (such as code, time, and cost restrictions) faced by specifiers and other building professionals.
When using CFS in a construction project, the material will have the same properties throughout the entire application. Steel is an isotropic material, therefore offering widespread consistency across construction products. Unlike alternative, bio-based materials like wood, cold-formed steel will not crack, warp, or change dimensions with moisture content, and does not have knots or other inconsistencies. This regularity allows manufacturers to create products fitting very tight tolerances, as they do not have to worry about products bowing or varying from other pieces.
In addition to material consistency, the logistical benefits of cold-formed steel extend from the manufacturing process to installation on the jobsite. Many CFS products are manufactured to suit specifications ensuring they fit seamlessly within a building. Manufacturers can pre-cut members to exact lengths—frequently within 1.6 mm (1/16 in.). This reduces waste both during production and on the construction site.
Once materials arrive at the jobsite, this combination of consistency and tight manufacturing tolerances allows builders to safely and easily construct building modules before installing them. The strength and stiffness of the material enables the construction of whole sections or systems (e.g. roof assemblies) on the ground. Such systems can include bracing, mechanical, plumbing, and sprinkler components, decreasing the amount of work required at high elevation, which in turn increases efficiency and reduces fall hazards. Offsite panelization of cold-formed steel wall and floor systems, when deemed appropriate for a project by the design team, can also reduce onsite labor costs and improve overall project cycle times. (Additional information on cost-effectiveness can be viewed at sfia.memberclicks.net/assets/CaseStudies/colborne_rev1.pdf and www.buildsteel.org/2016/10/14/building-cost-effective-mid-rise-building.)
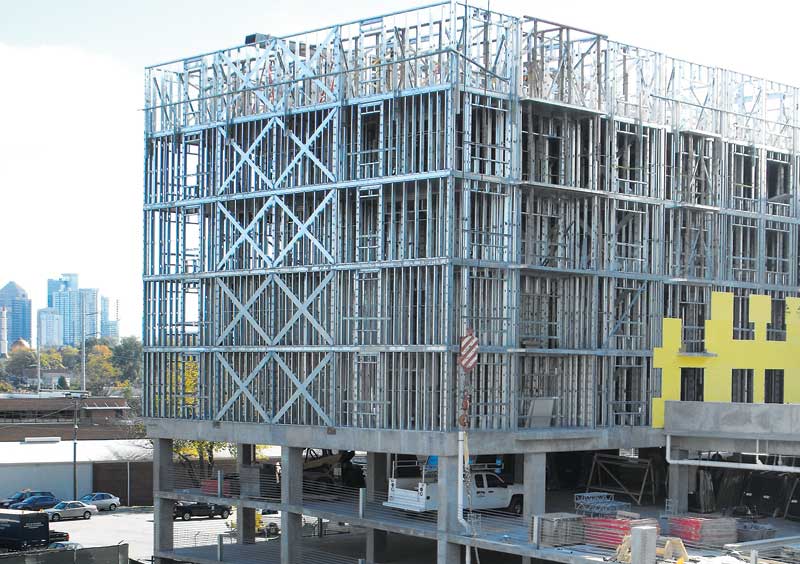
Design flexibility
The versatility of cold-formed steel allows specifiers and architects to develop mid-rise, multi-story buildings safely and efficiently, taking advantage of members with different thicknesses and yield strengths to distribute load effectively. For example, ledger framing can be implemented by stacking cold-formed steel-framed walls directly atop one another, eliminating the need to transfer roof loads through floor framing.
Cold-formed steel framing allows building professionals to change spacing, thickness, and yield strength of studs between floors for greater flexibility using load distribution members. As cold-formed steel is stronger than alternative materials, members can be placed farther apart within walls—they can be installed on 609-mm (24-in.) centers rather than the traditional 406 mm (16 in.). Beginning with thinner, more widely spaced members with lower yield strength in upper floors and then transitioning to thicker, more tightly spaced members in lower floors allows a more economical structure to be built, optimizing the steel for the applied loads. Having many light columns and beams rather than widely spaced heavy ones also leads to greater building resiliency, as members can pick up loads if adjacent ones are damaged. In the case of an emergency or natural disaster, these alternate load paths improve occupant safety and enhance resistance to disproportionate collapse.
In building design, shear walls are composed of braced panels that counter the effects of wind and seismic loads acting on a structure. For shear-wall applications, cold-formed steel can be used with diagonal-strap bracing or thin solid-steel sheathing to economically support the building in earthquakes and windstorms. When improperly detailed or specified, issues arise in these walls—high-profile screws used with thick straps and gusset plates can lead to uneven finishes. This problem can be prevented by using sheet-steel sheathing with low-profile head screws, or by using thinner, wider straps of steel with welds to eliminate gusset plates.
Some specifications require all exterior wall cavities to be filled with insulation, which can prove difficult when studs are tightly spaced within the wall, especially at jambs and posts supporting concentrated loads. The strength and versatility of CFS studs allows them to be more widely spaced, and using larger, thicker members at posts and jambs reduces the number of studs. With fewer studs at concentrated loads and greater gaps between existing studs, the number of thermal bridges are reduced, and spaces in walls are easier to insulate. Prepanelized, cold-formed steel walls enables manufacturers to tightly control fabrication quality, and can equip members to help support adjacent studs laterally, leaving more room for insulation.