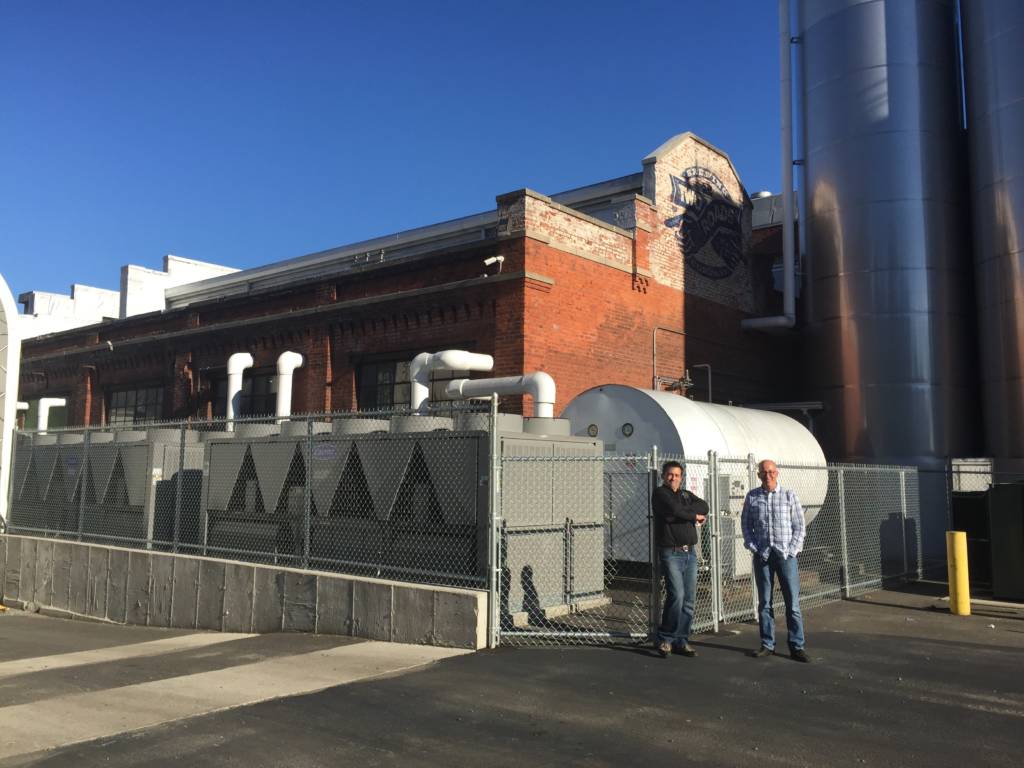
Photo courtesy Carrier Enterprise
Many people have opinions on what makes for a ‘perfect’ beer, but few are aware of the important role heating and cooling has to play in the craft-brewing process. The temperature of the wort (i.e. the liquid created in the beer-brewing process) affects the success of the brewing; thus, it is crucial for artisans like the Two Roads Brewing Company to utilize efficient chillers.
Formed in 2012, the Stratford, Connecticut-based company originally employed an 80-horsepower chiller system for the brewery, which was housed in a 1920s building once home to a metal-forming machinery manufacturer. However, as Two Roads gained success, two expansions were required, the first of which began in late 2015 and is expected to increase the brewery’s annual production from 75,000 to 150,000 barrels by the end of this year.
Given the critical role temperature plays in beer-brewing, these expansions necessitated a corresponding HVAC system upgrade. A priority for this upgrade was integration of the old HVAC system with the new, but simplicity of installation, energy efficiency (i.e. avoiding ozone depletion), return on investment (ROI), and controllability were also relevant.
The project team selected two air-cooled screw chillers designed for low-temperature operation, which could also integrate with the original chiller to exceed the company’s planned capacity and accommodate a 180,000-barrel facility. A parallel arrangement also allows the original HVAC system to be used as backup when the facility encounters high volume.
The new chillers have a flow rate of 1608 L/min (425 gpm) each, leaving 33 percent propylene glycol mix and ultimately producing 100 tons of process cooling. They can operate to –28 C (–20 F) ambient, thanks to low ambient kits, and are installed adjacent to the old system, on large concrete pads outside the building.
Additionally, the chillers offer the following features:
- suction-line insulation;
- freeze protection;
- isolation valves;
- electrocoated micro-channel-type condenser coils;
- non-fused disconnects;
- control transformers; and
- a proprietary noise-reducing package.
The standard HVAC controls have also been upgraded to allow the operations engineer to remotely view chiller plant operation and alarms as well as modify settings.
First off I acknowledge that I have not submitted any articles for public review, but this article is under the Form+Function and I don’t see the connection to this category. The article has stated historical information about the brewery and the company’s drive to increase their annual production two-fold, but I don’t follow the Form+Function part. My take is, it is missing how the additional chiller features help with the function of the new system and how it helps with production. On an architectural note, a few years ago I completed a HVAC chiller upgrade for two MRI units. The fencing around the new HVAC chiller was also a part of the architectural upgrades to that project. Not a simple fencing product shown in the photo above. The fencing could have been a part of the Form+Function.