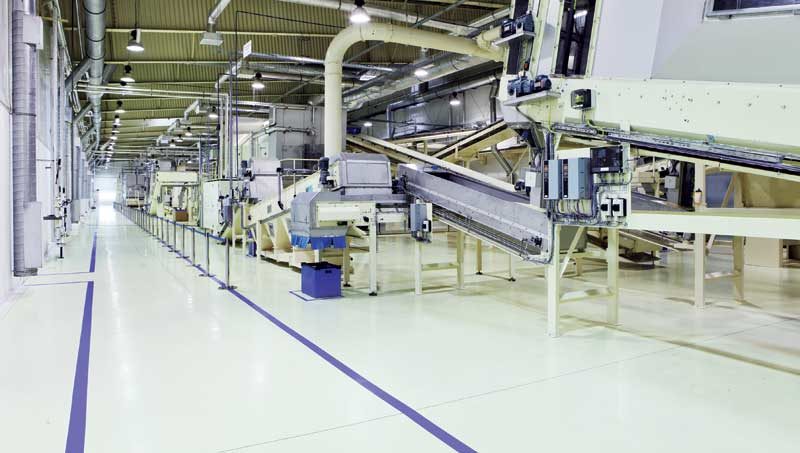
by Casey Ball
Specifying either a new or renovated flooring system for a commercial building often comes down to the quoted cost of the materials and labor needed to complete the job. However, that final quote is never the best measure of the floor’s true cost to the building owner—rather, it is just the check amount written to the contractor. The actual cost includes much more.
First, the building owner must be prepared for some downtime related to the flooring installation. No one will be able to walk through the area for a given period, halting progress on other work. Depending on conditions, contractors may need to take extra time to set up containment systems to eliminate airborne contaminants and mitigate odors. Ultimately, the faster the coating is applied and the sooner it dries and cures, the sooner everyone can resume normal operations. Anything a specifier can do to speed up these processes, such as recommending a fast-cure flooring system, can help minimize downtime and its associated costs.
The labor required to complete a job can also vary based on the chosen flooring. Specifiers can influence efficiencies and cost reductions by recommending products that are easier to install. The final crew size is the contractor’s decision, but if the specified product can help reduce application time, the project can achieve significant worker-hour savings.
The longevity of the flooring system and its repairability, however, are the primary indicators of its total cost of ownership. If the coating scuffs easily or if it is prone to deterioration when exposed to chemicals, maintenance crews will be busy making repairs, leading to more downtime and increased costs. Additionally, the sooner a building owner has to replace a floor, the greater its life-cycle costs. By recommending a system that offers durability, specifiers can help reduce maintenance needs, delay flooring replacements, and ultimately reduce expenditures.
Considering these ‘hidden costs’ provides a much clearer picture of a floor’s true price, and how to select the best system for a given project. However, one must also recognize swapping one flooring type for another can come with some tradeoffs—for example, faster installation might also mean higher odors. Surprisingly, it may be more cost-effective to install flooring that is more expensive upfront because its various downtime requirements and life-cycle costs are less than with a system with a lower initial expense. This article reviews several flooring types, outlining their potential hidden costs.