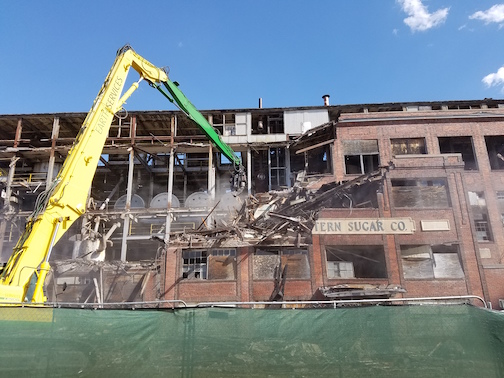
Photo courtesy ESA
How open-air demolition halved costs for a sugar factory project
by Sue Rose
The small town of Ovid rests in the far northeast corner of Colorado near the Nebraska border. While its modern amenities are limited to a couple of restaurants, a grocery, and a gas station, the town retains a significant historical landmark: the gleaming white storage silos containing beet sugar from what once was the Great Western (GW) Sugar Company’s finest factory.
Built during the booming sugar economy of the early 1900s, Ovid’s huge GW factory was built with coal, steam, and mules. The town incorporated in 1925 during the factory’s construction, and by 1940 had grown to a resident population of 650—twice the town’s current population. Unfortunately, Colorado’s sugar economy died off with the expiration of the Sugar Act in 1974, and the factory closed two years later.
By September 2006, the entire domestic beet-sugar industry had become grower-owned. Amalgamated Sugar, a cooperative of sugar beet farmers, bought the Ovid property in 2002. It had been abandoned except for the warehouse and silos, which were still in use. Amalgamated Sugar did not anticipate the liability they had taken on along with the purchase of the property.
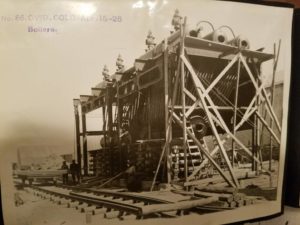
Photo courtesy TASCO
As with other abandoned sugar factories now dotting the rural landscape, Ovid’s abandoned factory was truly dangerous—structurally unsound and riddled with asbestos. In 2011, a death at an abandoned sugar factory in a nearby town (a person died after plunging 23 m [75 ft] while exploring the ruins) brought attention to the need to demolish and abate these sites.
Amalgamated Sugar made the commitment to abate and demolish the factory site, which included 11 smaller buildings, a 10,777-m2 (116,000-sf) mill, and a 59-ha (146-acre) site. The enormous price tag for the job would have to be borne by the cooperative’s 750 farmers themselves, with no hope for return on their money. Still, they deemed the investment worthwhile to eliminate the looming liability. They contracted with Schafer Environmental Consulting to devise a plan for abatement and demolition that would leave only the sugar storage silos and one warehouse standing.
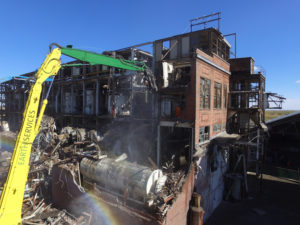
Photos courtesy ESA
Five years in planning stages
For five years, Schafer conducted extensive research and worked a complex series of proposals with the Colorado Department of Public Health and Environment (CDPHE). Several abatement and demolition firms bid on the project, intending to use traditional methods—that is, fully containing the structure in poly sheeting and then demolishing the structures after all asbestos had been removed. The costs were astronomical, ranging from $7.3 to $11 million. Earth Services & Abatement (ESA) proposed an alternate plan that might, if successful, save millions of dollars.
Central to the problem was the mill. According to Rod Schafer, that building was like a massive city within itself, housing its own power plant, huge boilers, and rusted machinery.
“The upper floors were collapsing,” he explained. “Engineers and the local fire department assessed the building, and calculated what would be necessary to rebuild parts of the structure to make it sound enough to proceed with the asbestos abatement.”
The customary method would have been first to enclose the mill, abate the asbestos, and then to demolish. However, there were tremendous safety concerns related to abating the main structure. Walls were collapsing, floors had dangerous penetrations, and handrails were mangled and broken. In short, it was unsafe to abate. To find a safer, more cost-effective way, ESA teamed up with Schafer and CDPHE.