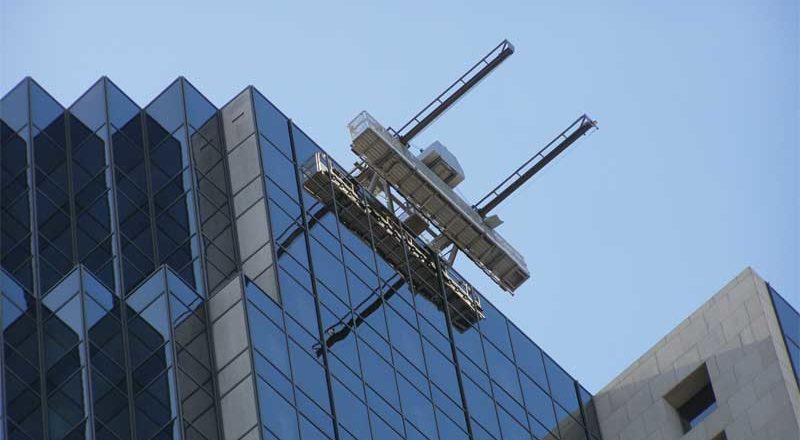
by Richard A. Dethlefs, PE, SE, Howard J. Hill, PhD, PE, SE, Leonard M. Joseph, PE, SE, Jonathan E. Lewis, SE, Karl J. Rubenacker, PE, SE, and Gwenyth R. Searer, PE, SE
Buildings taller than a few stories often include façade access equipment for washing windows, performing routine building maintenance, or engaging in construction activities on the building exterior. Building-mounted support elements for the façade access system may include davits, outriggers, and fall-arrest/lifeline anchorages. Proper design and load-testing of these components is a topic of considerable confusion and potentially dangerous misinformation. Having seen erroneous advice shared on several key technical aspects of this type of work on numerous projects, this article’s authors seek to provide a more comprehensive and rational summary of the design and testing requirements for façade access equipment.
Shown in Figure 1, façade access equipment is regulated by the Occupational Safety and Health Administration (OSHA), as well as other national and local codes and standards. It is important that engineers, architects, and owners, as well as the contractors who use the equipment, understand the regulations governing its design, inspection, and testing.
Design regulations
Codes and standards that address the design of façade access equipment include:
- OSHA;
- American Society of Civil Engineering/Structural Engineering Institute (ASCE/SEI) 7-16, Minimum Design Loads and Associated Criteria for Buildings and Other Structures; and
- 2015 International Building Code (IBC).
The design requirements for façade access equipment in these codes and standards are briefly summarized below.
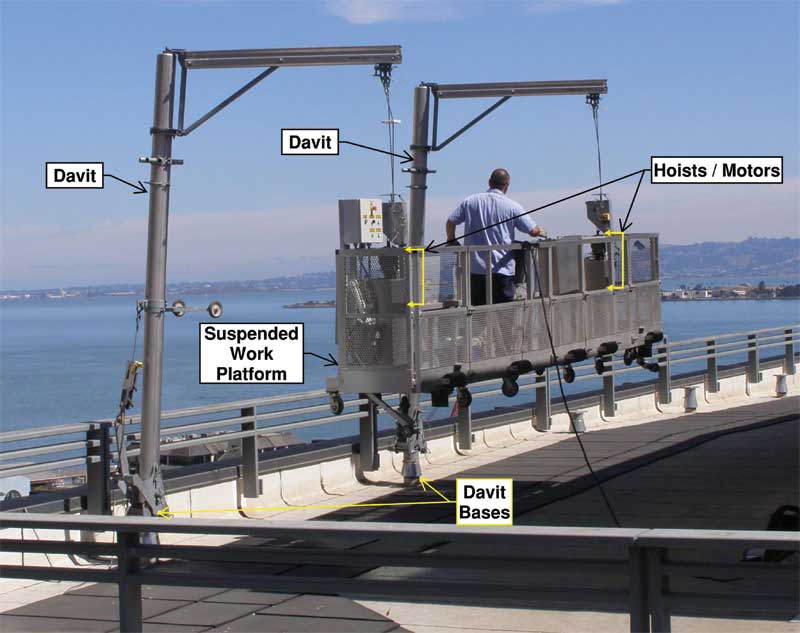
OSHA
The key to understanding the OSHA design requirements is having a clear comprehension of ‘rated load’ and ‘stall load,’ as these terms pertain to hoisting equipment for powered platforms.
‘Rated load’ is the safe working load that the hoist on a particular suspended window-washing platform is intended to lift. OSHA requires davits, outriggers, and connections to the building that support and/or provide backup for these elements be designed for a minimum of four times the rated load of the supported hoist. Why a safety factor of 4.0? Suspended platform starting and stopping loads are dynamic, resulting in forces that may be substantially larger than the static weight of the platform and its occupants. Additionally, hoists are machines capable of generating tension in the support lines far in excess of their rated load.
‘Stall load’ is the load at which a hoist stops operating. Since OSHA allows hoist stall loads to be as high as three times the hoist’s rated load, a platform moving up the side of a building that snags under a projection will continue to increase tension in the suspension cable until the platform breaks free of the obstruction, the hoist stalls, or an element of the suspension system fails. As a result, equipment designed to support four times the hoist rated load may only have an anticipated operating factor of safety of about 2.0 with respect to starting and stopping impact loads and 1.33 if a stall were to occur.
When façade access equipment is used for “construction” activities—defined by OSHA as almost any activity other than window-washing, including such mundane activities as painting and hanging of signage or holiday lights—the equipment must also be designed to resist 1.5 times the demands imparted by the stall load of the hoists they support. Absent knowledge of actual stall loads for all potential hoists that may be used with the equipment, façade access equipment for construction activities should be designed for 1.5 times the maximum permissible stall load, which is 3.0 times the rated load, resulting in a multiplier of 1.5 x 3.0 = 4.5 times the rated load(s) of the hoist(s).
OSHA fall-arrest/lifeline anchorages typically must be designed to withstand, without failure, 22.2 kN (5000 lb) per attached person. This might seem large for a worker who only weighs about 115 kg (250 lb), but dynamic behavior must be considered. To arrest a worker falling 1.8 m (6 ft), harnesses and lanyards are permitted by OSHA to generate up to 11.2 kN (2520 lb) of force. Thus, the 22.2-kN pound design load represents a fall-arrest factor of safety of about 2.0, which is not unreasonable for a fall-arrest/lifeline—especially considering that falls greater than 1.8 m are possible in some instances and workers may weigh more than 115 kg.
While the aforementioned load requirements for façade access equipment are generally clear, less clear is how to incorporate those load requirements into structural design and test loads for this type of equipment. OSHA requirements use terminology inconsistent with common structural engineering design methodologies, which has led to confusion in this regard. A clear and comprehensive discussion of the key structural requirements for design, assessment, and testing of façade access and building maintenance equipment can be found in ASCE’s 2015 publication, Façade Access Equipment: Structural Design, Evaluation, and Testing.