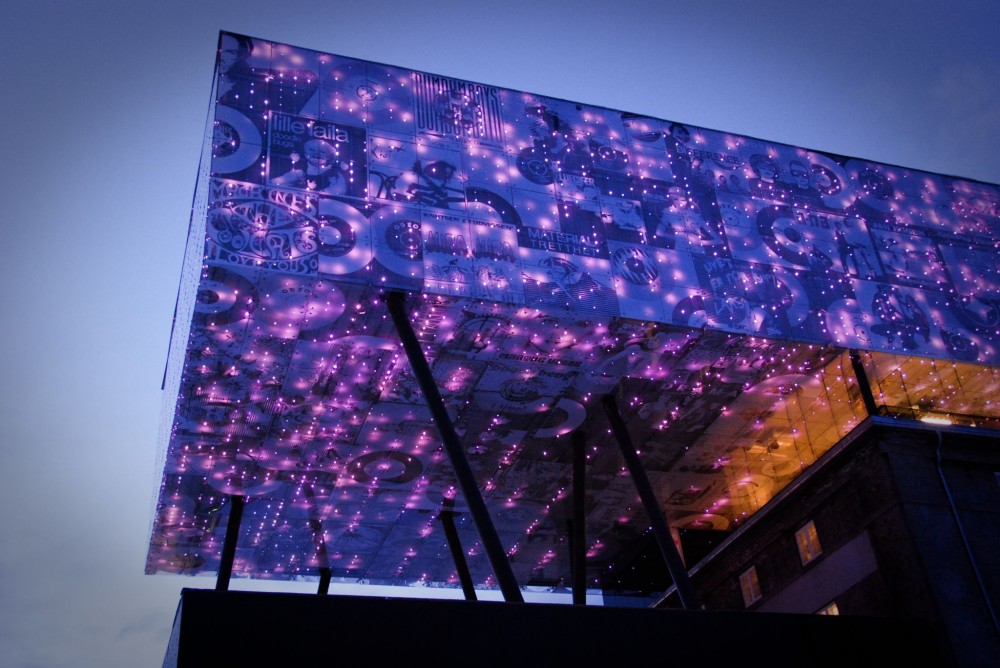
by Brian R. Savage, CPA
Previously, when architects wanted to add printed design elements to the glass skin of a building, they were limited to one- or two-color silk-screening or digital prints with difficult, organic-based inks. Now, ceramic-based inks have transformed digital imaging, resulting in a more controllable process with durable, long-lasting, hues.
The current generation of digital printers gives designers the opportunity to turn what was just the functional façade of a building into a decorative canvas. They also provide a way to optimize design, color, and solar performance for many types of façades. For example, curtain walls can have an image applied across the entire elevation while stone veneer can be replaced with a printed replica that can reduce cost and weight. Printing on punched openings can add a nice contrast to the other façade materials used in the building design.
Digital printing basics
There are various digital printing processes available for the architectural glass market. The two main differences within these digital printing techniques are the types of ink used and how the printer transfers the ink onto the glass substrate. This article focuses mainly on inkjet-style printers using drop-on-demand technology.

These printers employ a programmable print head that travels back and forth just above the substrate where the image is being applied. Each color of ink has its own grouping of nozzles on the print head that is individually activated and drops ink onto the glass substrate in the proper location—hence the name ‘drop-on-demand.’ The printers are usually located in a glass fabrication facility; the use of a clean room is recommended to reduce the chance of airborne particles contaminating the print.
Digital printing processes generally rely on organic ultraviolet (UV)-cured, inorganic ceramic inks that are fired to the glass during the heat-treating process, or specialized inks for printing on interlayers.
The cost for each of these printing types varies depending on the project’s size or complexity of the glass make-ups, but they are generally competitive with one another. UV-cured printing is suitable for interior applications, but has a limited use on exterior façades as the ink degrades over time.
Ceramic ink printing is useful in both exterior and interior applications, and can be employed in multiple types of make-ups. Printed interlayers must be used in laminated make-ups and may be subject to stretching and distortion during the fabrication process, but remain lightfast over extended periods.
In the past, the physical properties of ceramic frit—including the corrosive effect it had on the size of print heads and particles within the frit—made them difficult to print with an inkjet printer. Those drawbacks have been addressed and ceramic ink is now practical for use with a digital printer. Ceramic frit and ceramic ink are composed of microscopic particles of glass, pigments, and a liquid carrier. The liquid portion is dried and then fired so all that remains fused to the glass are the glass particles and pigments.
Digital printing’s flexibility means it can be used monolithically, or included in laminated and insulating glass units (IGUs). It can also be employed in combination with interlayers and have solar control coatings applied directly over the digital print, resulting in improved solar performance. Digitally printed glass can be used in numerous building areas, including:
- exterior façades;
- interior dividing walls;
- signage; and
- office walls.
The versatility and resolution capability of ceramic ink means various types of images can be printed, including photorealistic images, text, variable graphics, and patterns. Additionally, textures similar to wood grain, granite, and marble can be produced with excellent results. Both the transparency and opacity of the print are controllable. (These types of prints will be referred to as ‘images’ throughout this article.)
Digitally printed glass can be maintained in the same manner as other ceramic frit-coated glass. As a general rule, if it harms the glass, it harms the print. The recommended cleaning procedure includes using a conventional window-washing solution or mild soap and water in conjunction with a nylon bristle bush where needed. Razor blades, putty knives, and metal parts of glazing tools can scratch the printed surface, so care must be taken with their use. However, in most applications, it will be permanently protected in an insulating or laminated unit.
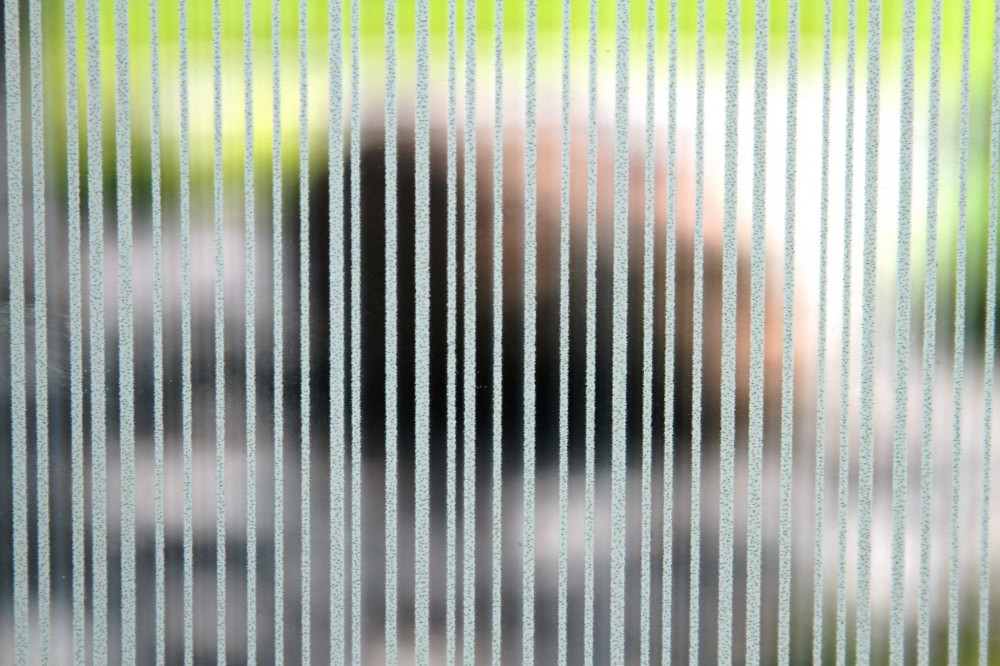
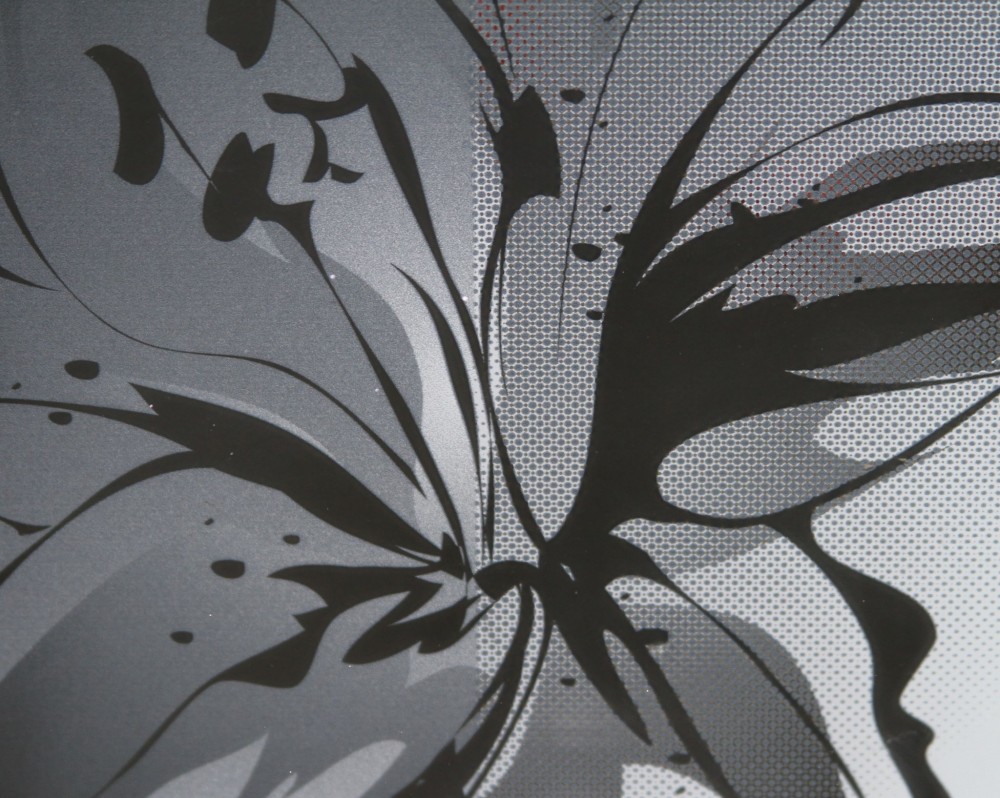
Comparison to other glass enhancements
In the past, when there was a desire to add a visual design element to a building’s façade or interior, architects have largely been limited to a narrow range of products, including silk-screened designs and various interlayer systems. Each product has its advantages and disadvantages.
Silk-screening is usually the most cost-effective when there is a desire for only one or two colors, a repeating pattern is used, or there are many units to be silk-screened. However, the actual screen used in the silk-screening process can be cost-prohibitive, and is limited in the number of prints it can produce before reaching the end of its useful life.
Printed and colored interlayers can be useful when solid hues are required, but since they must be bonded between two pieces of glass, they can only be used in make-ups with a laminated component.
Digital printing helps remove some of these barriers, but may not be the ideal solution in all instances. It should be thought of as a complement to other technologies, including silk-screening and interlayers, and not necessarily as a replacement. If there is a desire for multiple colors within a design, a complex design is used, or an image is stretched across multiple units of the elevation, digital printing may be ideal.
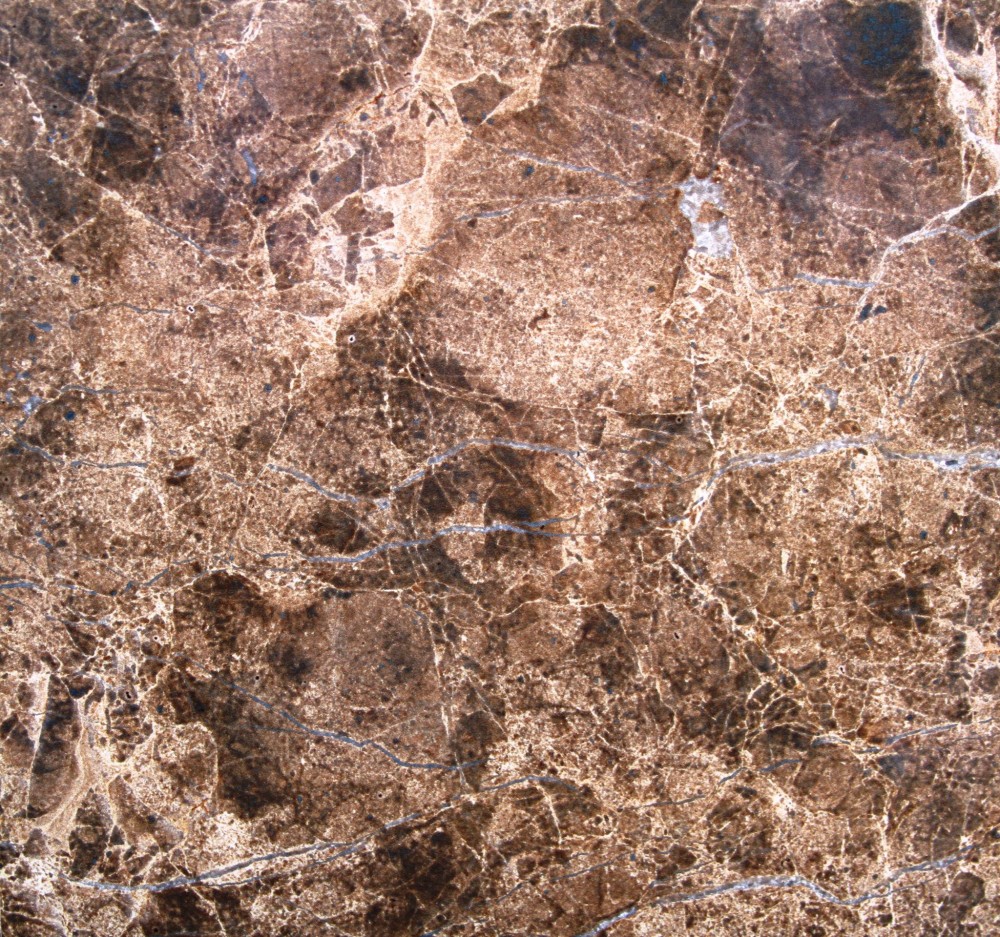
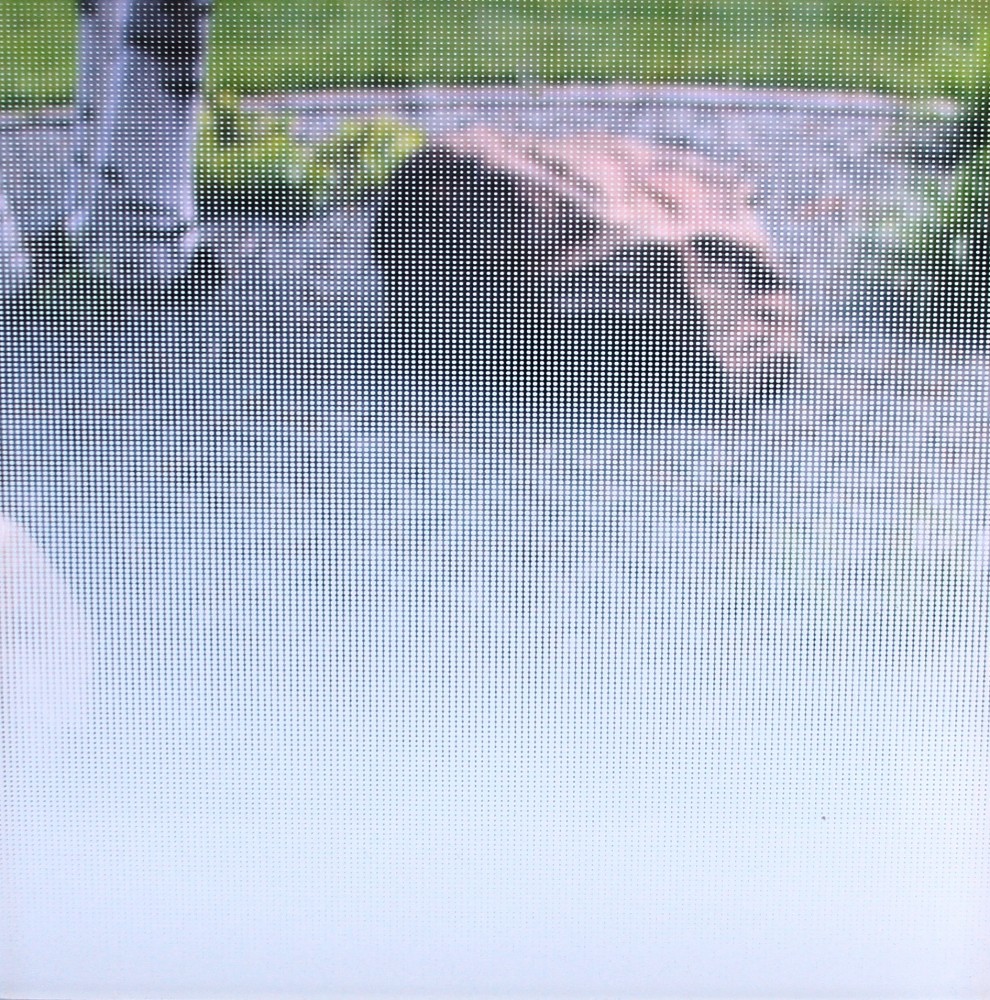
Characteristics of ceramic ink
The inks used in digital printing are similar to the frit used in the silk-screening process. Both are ceramic-based, and perform and behave almost identically. The main difference is inks are produced with smaller particles of glass to allow them to flow through the print head onto the glass substrate. The inks also contain inorganic pigments, which help them to be as color-stable as ceramic frit over the printed image’s life.
The inks used in North America are free of heavy metals like cadmium or lead. Even with that limitation, a wide gamut of colors can be achieved by mixing base ink colors into final printed colors. There are two methods of color mixing—premixing and digital mixing during printing.
The first type is useful when there are only a few colors involved, or when a smooth color appearance is required for a project such as interior signage. Digital mixing is essentially the same concept as an inkjet printer.
With digital mixing, distinct variations in colors are achieved by placing drops of individual colors next to each other. Looking closely at a television screen offers the same effect—the screen is generally made up of blue, green, and red pixels; the three colors appear individually from a close distance, but combine to form the final image when viewed from farther away. This same concept occurs with digital mix. Blue and red drops of ink placed next to each other appear individually when examined up close, but combine to form purple when seen at a distance.
The inks are also able to be applied by the printer at varying thicknesses to achieve design results such as solar control or desired color variations. For example, blue ink tends to be more translucent than other colors, so a print with more blue may allow additional light transmission to the building’s interior during the day. A predominantly blue design may also let out more light at night as viewed from the exterior. If the intent is to limit the transfer of light, the various colors can be applied at different thicknesses to balance the amount of light transferred. However, the reverse is also true. If the intent is to create a façade that essentially glows with a stained glass effect from the interior or exterior, the image can be adjusted to achieve the desired effect.
Comparison of ceramic-based inks and organic-based inks
Ceramic-based inks and organic-based inks have advantages and limitations. Ceramic-based inks are durable and remain fused to the glass for a long-lasting print. Colorfast over long periods, they are resistant to scratches and abrasions. However, there are limitations on the achievable colors due to the restrictions on the use of heavy metals in production of ceramic ink. Ceramic ink standards for durability, expansion fit, and gloss falls under ASTM C1048, Standard Specification for Heat-strengthened and Fully Tempered Flat Glass.
On the other hand, organic-based inks tend to have a much wider color palette than ceramic-based, but are not as durable. Organic inks are not very colorfast, which limits their use to mostly interior applications. Organic-based inks cure at a lower temperature (i.e. 170 C [338 F]) than ceramic-based based inks (i.e. 600 to 670 C [1112 to 1238 F]), resulting in a potentially lower use of energy during fabrication.
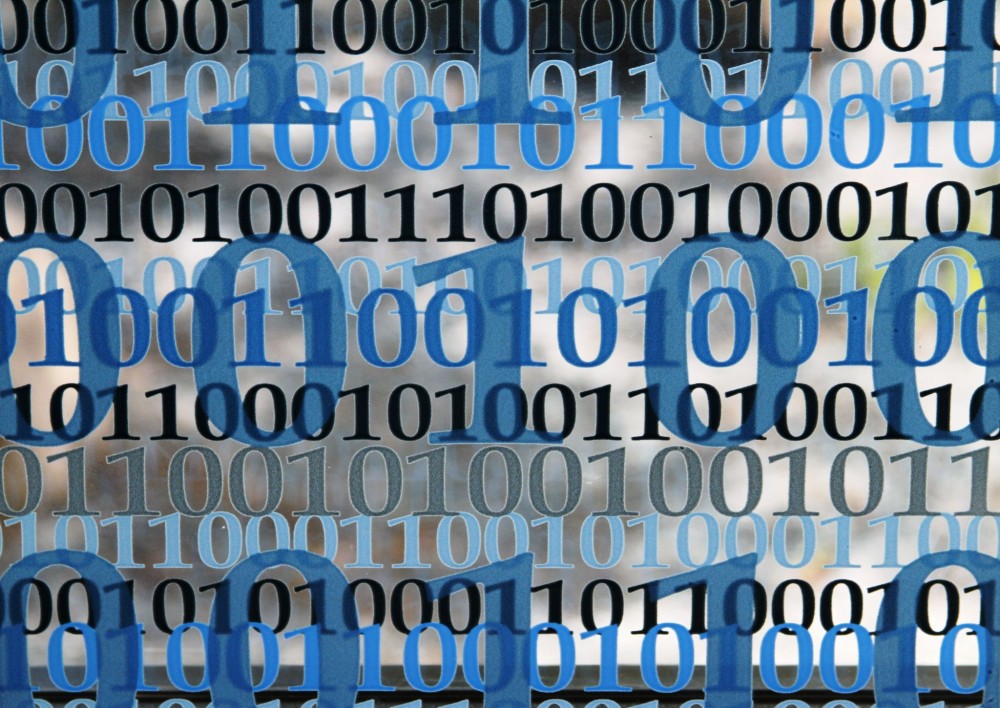
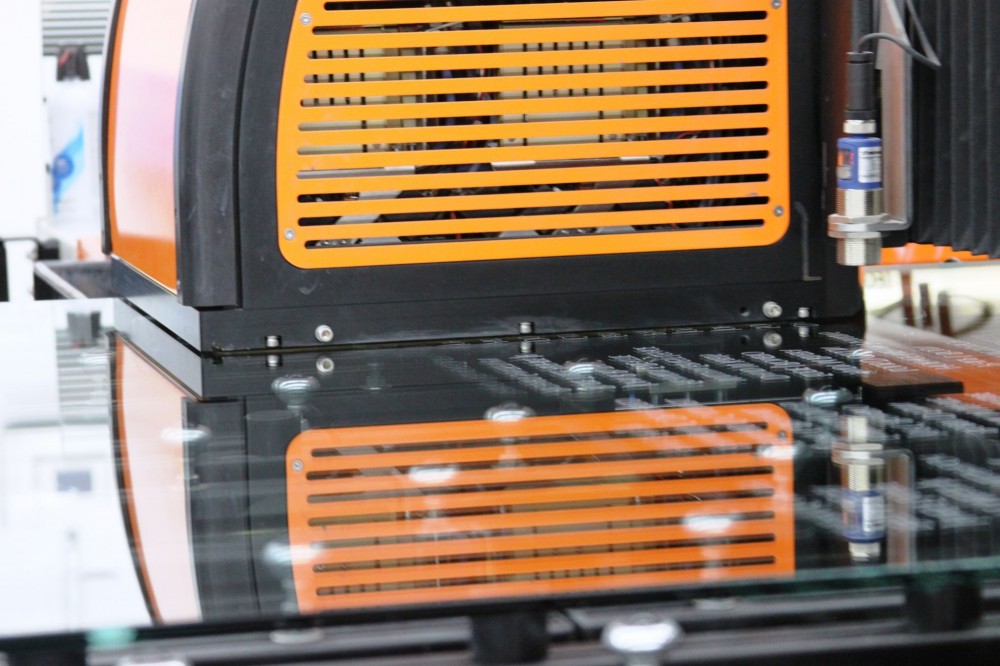
The digital print process
The actual digital printing procedure can be separated into two distinct, but dependent, processes—electronic design file manipulation, and printing the image on the glass substrate.
The electronic design files can be produced in various formats. Both raster and vector-based images are acceptable in this process. The key attribute is the files must be high-resolution; the larger the actual printed image, the larger the file required. Since each project’s requirements are different, the meaning of ‘high-resolution’ varies. The proper preparation of image files is one of the most critical steps in the process. The printed glass quality can only be as good as the file used to generate the print.
Due to the thinner viscosity of the ceramic inks, a balance must be achieved regarding image resolution. Thinner viscosity allows for higher resolutions than may be possible with other ceramic-based media. However, care must be taken when the ink is applied at thicker opacities, as it may start to run together and blur the printed image.
The files can be individually designed for each unit to be produced, or the entire elevation can be designed as one file, allowing software to then tile the image across a façade. Such computer programs, which are usually proprietary and specific to each printer’s manufacturer, can also adjust the image for the inclusion of items such as mullions and holes for point-supported glass so the image flows seamlessly from one pane to the next. Finally, the software rips the image into color layer files for each of the base ink hues to be printed. For instance, a purple image might be ripped into a blue and red layer. Depending on the images’ complexity, there may be multiple layers of the same color.
These different color layer files are then sent to the printer where the image is interpreted and ink is deposited onto the glass substrate. Once the lite of glass has the image printed on it, the glass is sent through a tack oven to dry the ink. Newer-generation printers are now able to dry the ink as the image is being printed. At this point in the process, the ink has a matte finish and has not permanently adhered to the glass substrate.
The printed image is sent from the tack oven through a heat-treating oven where it is heat-treated, tempered, or even bent, according to the specification. The ink is fired at temperatures of 600 to 670 C (1112 to 1238 F), depending on the oven’s setup. It is only after this step when the image is permanently fired to the glass and the ink takes on a glossy finish. From here, the printed glass can be directed to other processes, including coating application, laminating, and insulating lines. If it is to be used in interior applications, it might even be left in monolithic form.
![Otherwise-plain façades can be upgraded with relatively lightweight and cost-effective digital printing. [CREDIT] Photo courtesy Dip-Tech Digital Printing Technologies Ltd.](http://www.constructionspecifier.com/wp-content/uploads/2014/05/ZAC-Euralille-France1-1000x750.jpg)
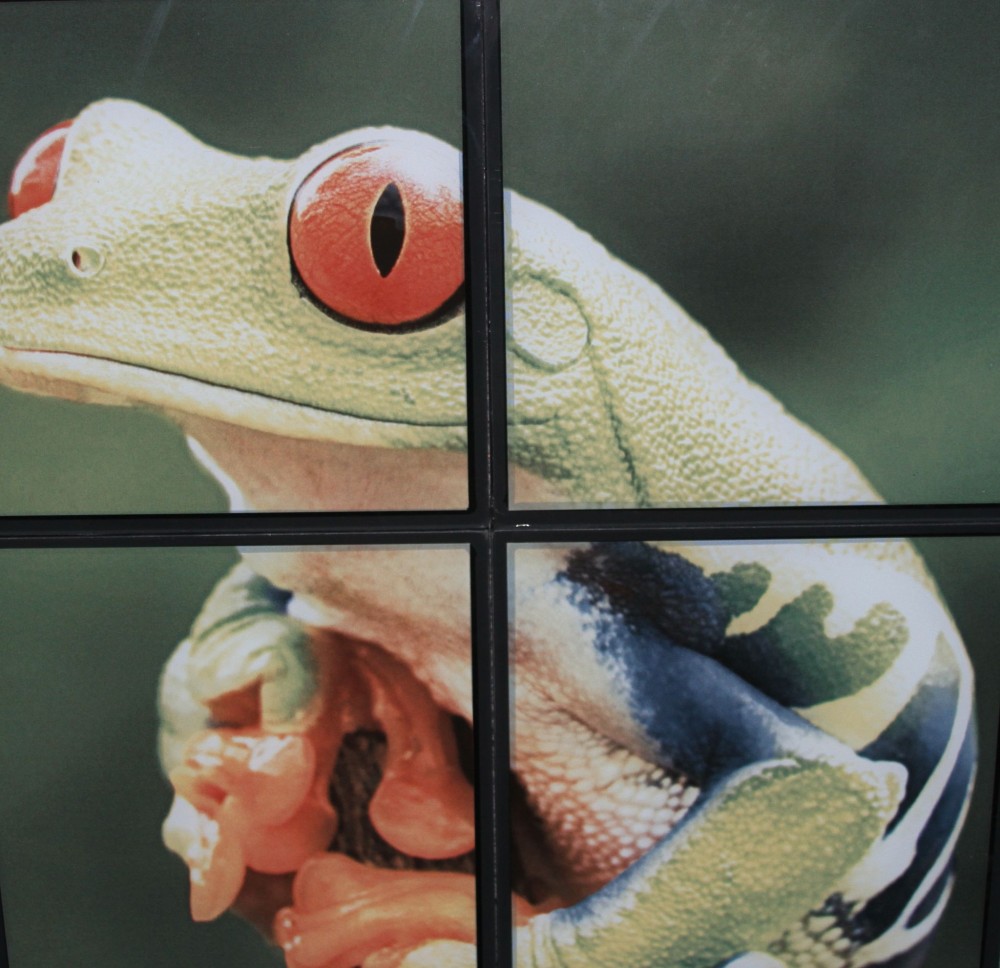
Benefits and limitations
Benefits of the digital printing process include cost savings, design flexibility, and repeatability. The cost savings over silk-screening occur when numerous screens are required relative to the final number of units needed to be produced. There are also no storage costs with digital printing (something associated with screens) because files are kept electronically.
Design flexibility is achieved by allowing for custom images consisting of multiple colors. Micro-lines, micro-dots, and dual images add to the flexibility offered by digital printing. Dual images consist of an image viewed from one side of the glass with a different one seen from the other side—even though both images are printed on the same surface of glass. Finally, stored design files mean replacements and reproductions can be produced years later with dependable results.
There are also limitations to the digital printing process that must be taken into consideration to determine whether digital printing is the appropriate choice. Calculating performance data across the façade can be challenging.
As mentioned, the various colors of ink can transmit light and solar energy at different levels. For example, a large-scale print project involving multiple colors combined with a custom image across a façade allows light and solar energy to enter the building in various levels, even within the same pane of glass. As a result, performance data can be difficult to calculate. However, minimal performance levels can be gauged because performance characteristics, coating applied to the digital print or glass substrate, and other enhancements are already known.
Matching the color of the final printed image to the designer’s vision can also be challenging. The amount of light being transmitted and reflected during a sunny versus cloudy day, or afternoon versus night, affects the way the image is perceived.
Additionally, applying a coating over the print may mute the vibrancy of the colors. The choice of substrate can also cause the colors to appear different than the design. For example, regular clear glass may impart a green hue to the image, while a low-iron glass substrate helps subdue this ‘green-shift’ effect. All these issues must be taken into account when designing an image using digital printing.
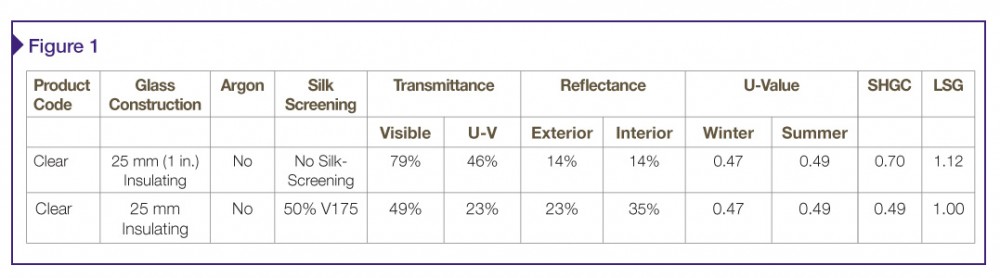
Finally, to control the level of light and solar energy entering the building’s interior, a silk-screened-type pattern can be applied on the glass. For example, a white dot pattern with 50 percent coverage on a 25-mm (1-in.) clear IGU can reduce the light transmission by 38 percent and lower the solar heat gain coefficient (SHGC) by 30 percent (Figure 1).
This reduction occurs by blocking the light and solar energy from entering the building at the outboard lite of glass. At the same time, designers may add more of an aesthetic element to the façade than the single color of dots or lines that silk-screening usually provides.
Digital printing expands on the ability to incorporate solar, light, and privacy control to an electronic design file before printing an image. One of the methods involves applying a computer-aided design (CAD) file, normally used to produce an actual screen for the silk-screening process, to the image to be printed. For example, a CAD file with 40 percent coverage of holes that might have previously been printed in white ceramic frit can now be applied to an electronic design file and printed in multiple colors and without the need to purchase screens.
Some additional methods include converting the image to patterns of dots in halftone processes known as amplitude modulation (AM) screening and frequency modulation (FM) screening. AM screening converts the image to dots that are the same distance from center-of-dot to center-of-dot, but the individual dot size can vary.
FM screening, also known as ‘stochastic screening,’ is characterized by the size of the printed dots remaining constant. However, the distance between the dots is visually random to create the various densities of the image within the print.
![When combined with a low-emissivity (low-e) coating, digital printing can add an attractive and functional element to a façade. [CREDIT] Photo courtesy Brian R. Savage](http://www.constructionspecifier.com/wp-content/uploads/2013/08/Digital-Print-Window-From-Exterior-1000x666.jpg)
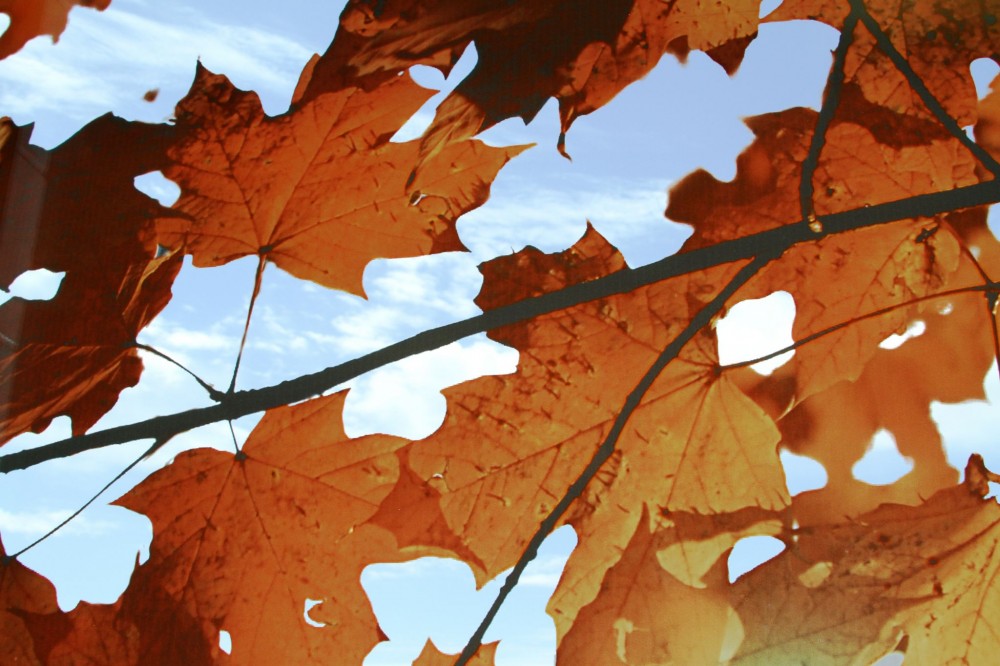
Conclusion
There is a constant demand for new and diverse ways for designers to leave their mark on a building’s façade. Digital printing has emerged as a versatile and colorful addition to the supply of products helping define this vision. Not only can multiple colors and design concepts be added with relative ease, but many performance aspects within the façade design of solar control and privacy can also be fine-tuned through both hardware and software features available to digital printing.
Digital printing is versatile enough to be used in interior and exterior applications, can be specified in combination with other glass products, and has the durability of ceramic frit applications used for years in architectural design.
Brian R. Savage, CPA, is a product manager at Viracon Inc. He has worked in the construction industry for 10 years and has led the launch of numerous new products at Viracon. Savage can be contacted by e-mail at bsavage@viracon.com.