by Howard Jancy, CSI, CDT
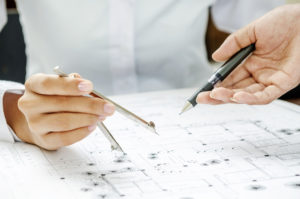
Photo © BigStockPhoto
Timing the office visit, telephone call, or e-mail to an architectural firm according to a project’s development stage is crucial, but providing the most relevant information for the stage and design professional involved is equally important. The schematic design and design development phases generally require the most detailed information from the contractor and its suppliers or manufacturers. While members of the project design team may have overlapping needs and involvement during project delivery, a basic understanding of their roles and responsibilities is critical.
This article, the last in a two-part series, outlines the best approach to an effective discussion with an architectural firm.
Project manager
The project manager is involved at all stages. He or she requires information on general cost estimates and product information, project references of similar scope or difficulty, and scheduling impacts.
Project architect
Project architects take part in the design development and construction documents stages, and require knowledge about refined cost estimates, project references, specific products’ or manufacturers’ information, and scheduling impacts.
Project designer
Involved at the design development and construction documents phases, the project designer requires color charts, a pattern selection guide, cast samples, color chips, and installed costs.
Specifier or independent specification consultant
Specifiers take part at the construction documents stage and sometimes also contribute to design development, requiring product technical data, guide specifications, and installation requirements.
As a project’s development progresses, the informational requirements of the design team members become more differentiated and precise. For example, the project designer tends to need comprehensive aesthetic information, while the specifier often requires more detailed technical information. When meeting with the design team, it is important to ask questions and take notes.
A contractor can:
- offer multiple relevant options by asking what the budget is;
- create solutions and establish realistic expectations for a product’s performance, aesthetics, and maintenance by asking what the design professional and project owner’s requirements, experience, and expectations are; and
- discuss sustainable advantages of product offerings, related installation technologies, and materials by asking whether the project will be certified under the Leadership in Energy and Environmental Design (LEED) program.
The specifier’s influence on product selection
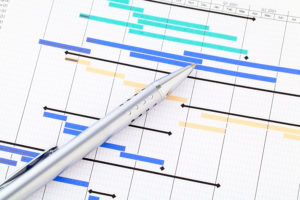
Photo © BigStockPhoto
Conversations with the project designer during design development are about product options and recommendations. Generally, these recommendations are based on experience with a particular manufacturer or system. This is quite typical, and is an acceptable way of incorporating products into a project’s documentation. The specifier will usually draft the construction documents (i.e. specifications) based on the project designer’s selections. However, if she or he does not know the product or manufacturer selected by the project designer, a more-familiar system that has produced successful outcomes on previous projects may be substituted.
This means no matter how well a contractor has educated and impressed other members of the design team, without an understanding of the specification process in an architect’s office or meeting with the specifier before that process begins, his or her earlier efforts may be diminished. This is even more critical if a design firm is using outside or independent specification consultants, who often rely on in-office master specifications to expedite documentation production, since they produce specifications for several projects and clients.