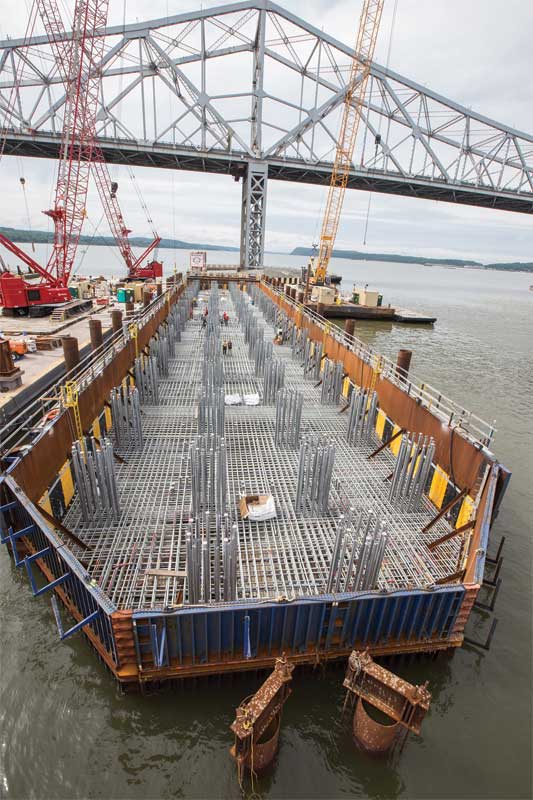
by Laura Hanson
Many different types of concrete construction projects can use reinforcing steel (rebar), including architectural buildings, exposed beams and columns, bridge decks, and various transportation infrastructure projects. The steel embedded within is essential to the performance of these structures. The majority of the funding that is allocated for the more than 600,000 bridges in the United States is spent on maintenance. (This information is derived from Matt Westerfeld’s “Stainless Steel Corrosion Protection in Transportation Infrastructures Technical Paper,” published in June 2014 by a stainless steel conduit provider.) Often, this cost far outweighs the original expense of installation. Rebar corrosion protection is therefore crucial to reducing maintenance costs—but what type of rebar is best?
Concrete is a porous material, meaning water, salts, and other elements may eventually seep through it, penetrating to the steel within. It is therefore essential for weather- and water-exposed concrete to use a corrosion protection system to prolong the life of the embedded steel, ensuring integrity of the surrounding concrete. Concrete is also extremely complex, and the use of its various types has made its chemical, physical, and mechanical properties as well as its relationship to metals topics of ongoing study.
It is important to protect reinforcing steel embedded in concrete to ensure longevity and safety. Visible signs of rebar corrosion include staining, cracking, and spalling. Spalling occurs when corrosion byproducts, which are more voluminous than the metal the corrosion process consumes, accumulate within the concrete, placing increasing stress on the material. Once these stresses are greater than the tensile strength of the concrete, it will crack from within, leading to pieces of concrete separating from the structure.

Photos courtesy American Galvanizers Association
This can be dangerous for overhead structures such as overpasses, as the falling concrete imperils anything beneath or next to the structure. Under some circumstances, maintenance to repair spalling and prevent failure can be performed, but it is expensive. Galvanizing, however, protects rebar from rusting, thereby preventing the concrete from spalling. Zinc corrosion products have much less volume than black (i.e. uncoated) steel, and the corrosion products that form within the concrete migrate outward from the galvanized rebar into the concrete matrix. This prevents pressure from building up at the site of the junction between the concrete and the rebar.
Many types of reinforcing steel can be used in concrete, as can many steel corrosion protection methods. Therefore, it is important to consider the benefits of each when specifying rebar.
Types of reinforcing steel include:
- bare;
- stainless;
- martensitic microcomposite formable steel (MMFX); and
- coated.
Rebar coating types include epoxy-coated and galvanized. With such a variety of options available, choosing which type of corrosion-resistant reinforcing steel to specify can be daunting. The three most common choices are stainless, epoxy-coated, and galvanized.
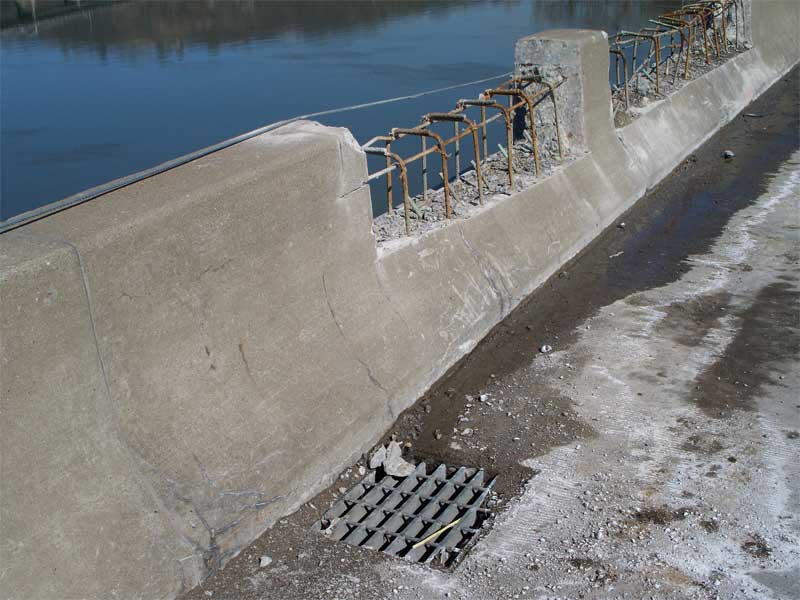
Stainless steel is a newer reinforcing steel application. Therefore, there is less data available regarding its performance. So far, accelerated testing and laboratory studies indicate excellent corrosion protection and estimated long life. Epoxy-coated reinforcing steel, however, has been widely used in bridge decks and other projects since the 1970s, meaning extensive performance research is available—with varying results. Recently, epoxy-coated rebar has come under fire by many state Departments of Transportation (DOTs) for its short design life, lack of bond strength, and special handling requirements. However, its low cost can make it a solid option for less corrosive environments, where low initial cost is a major factor in early materials decisions.
Galvanized reinforcing steel has been used in concrete construction products for decades. It is hard to pinpoint the earliest use of this steel, but there are known North American projects using galvanized rebar dating back to the 1960s and 1970s. It requires no special handling, has proven to work in highly corrosive conditions, and offers a competitive initial cost and estimated long life.
TAPPAN ZEE REPLACEMENT BRIDGE |
Although still under construction, the New New York Bridge Project, which will replace the Tappan Zee bridge, will incorporate thousands of tons of galvanized rebar into the final design. The rebar will reinforce concrete in areas including decking, supports, and columns, and the zinc will ensure the product withstands the rigorous handling it will go through from the galvanizing tank to the pouring of the concrete. |
This article inaccurately states that, “Stainless steel is a newer reinforcing steel application. Therefore, there is less data available regarding its performance.” The world’s longest pier in Progreso Mexico was completed in 1941 using stainless steel reinforcement. Based on this article, that was well before galvanized rebar was introduced.
The statement indicating the studies of stainless steel reinforcement are limited is also false. Stainless steel concrete reinforcement has been extensively studied globally and its’ exceptional performance documented in NACE and other papers. There have been many long term side-by-side bridge deck installations (Americas, Europe, Asia) and comparative evaluations of stainless steel relative to other types of reinforcement.
Furthermore, for steel reinforcement to be identified as “corrosion resistant” in the ASTM standards, there must be a corrosion test and a minimum requirement for certification. The ASTM stainless steel and epoxy coated rebar both have corrosion test requirements – galvanized steel does not and when this has been discussed at past A01.05 meetings the industry has declined to add a corrosion test requirement. A review of the corrosion data available for galvanized rebar shows that it does not perform well in the standard laboratory tests that are used for steel reinforcement and the evaluation of its’ performance in actual installed applications has varied substantially based on the concrete type and actual conditions.
This article is factually problematic in many respects and is clearly attacking a competitive material by providing false information.