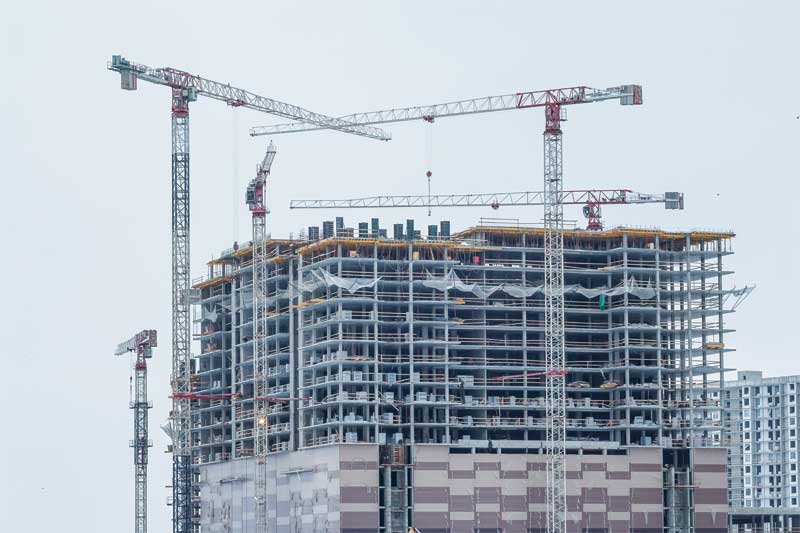
by Larry W. Williams, APR
A building’s framing system performs the essential task of providing strength and stability to the structure, offering a path to transfer loads from gravity, uplift, and seismic forces to the foundation. However, even properly designed and built framing depends not just on the strength of these components, but also on the performance of the connections holding the elements together. These connections are even more critical in coastal and high-seismic zones where structures must resist the movement, stress, and loading from natural events such as earthquakes and high-velocity winds.
Critical connections occur throughout the structure, but the most important are found in four crucial areas for the majority of buildings:
- where the roof system connects to supporting walls;
- at openings and headers in the walls;
- where walls connect to each other at floor levels; and
- where walls connect to the foundation.
Connectors, clips, or framing hardware are used to either make or support cold-formed framing connections, with the most common types being rigid (i.e. fixed) and deflection (i.e. movement) connectors.
Rigid connectors
Rigid connectors and supports are used in various ways to secure cold-formed framing members to each other or to
the building structure. Common types of rigid and fixed connections include:
- joist connections;
- punched openings;
- beam/wall connections and bridging; and
- header and truss connections.
The types of connectors used in these locations include cold-rolled channel (CRC) clips, hangers, pre-punched clips, holdowns, and hurricane ties.
Until recently, it was common practice on cold-formed steel framing projects for installers to fabricate these types of connectors in the field using whatever scrap or stud material available. In the past few years, however, the shift to pre-engineered and premanufactured connectors has been gaining momentum for a number of important reasons.
First, design professionals are increasingly producing high-performance engineering that demands all the elements used in a building perform as expected. Pre-engineered connectors are designed and tested for ultimate and allowable load capacities, which can then be used by the designer to ensure calculations are based on how the connector actually performs.
As a growing number of these pre-engineered, premanufactured connectors gain code listings, building officials increasingly expect to see a third-party verification proving that the connector is manufactured according to the applicable standards. In 2014, the Steel Framing Industry Association (SFIA) rolled out a certification program providing independent third-party verification the associated connectors meet quality guidelines, building codes, and AISI ASTM standards.
Certification includes unannounced audits and onsite inspections of certified companies, along with field and laboratory tests to ensure the certified steel products meet standard tolerances for shape, material thickness, and corrosion protection. Having design tables based on testing is essential to predictable and safe design, but a third-party certification the products have been manufactured or fabricated as designed provides an additional level of certainty.
A third factor fueling the move away from field-fabricated connectors is contractor recognition of the fact making these parts onsite consumes valuable hours that can eat away any perceived cost savings from fabricating a connector out of scrap. Performance may also suffer, as these hand-made connectors lack the pre-punched holes that help installers properly place the fasteners in the locations ensuring the connector achieves the intended design load.
At first blush, a field-fabricated connector would seem to be the clear economic choice because the material used would otherwise be discarded as waste. However, contractors are also recognizing this savings is quickly offset by inefficiencies from having to cut, bend, and fashion custom-made connectors for each location where one is needed. In large projects, this can consume many valuable hours. Performance further suffers, as these hand-made connectors lack the pre-punched holes that help installers properly place the fasteners in the locations ensuring the connector achieves the intended design load. There are some instances where a field fabricator could make sense, but they are almost always for temporary bracing where the element will be replaced with permanent bracing.