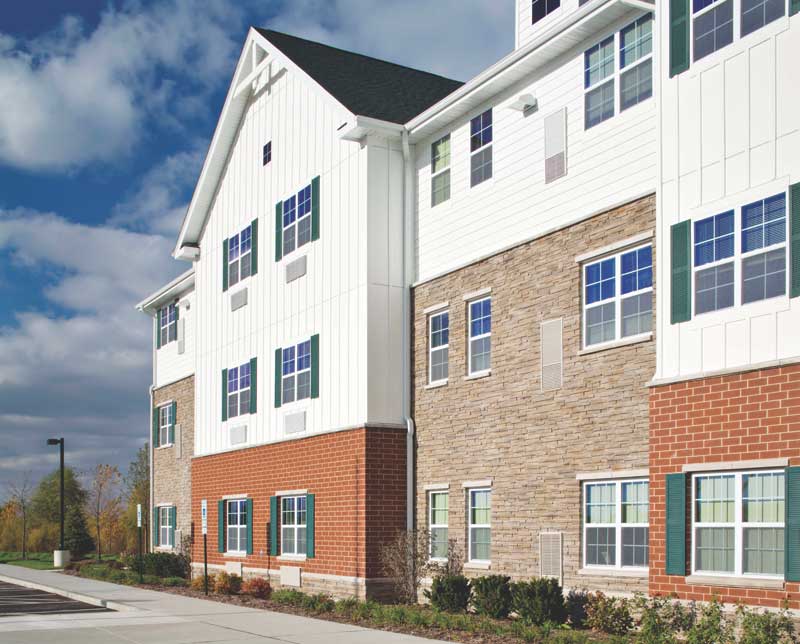
by Jim Cooper
For construction projects ranging from residential homes to light-commercial projects such as healthcare centers, retail buildings, and senior living facilities, manufactured stone veneers offer cost savings, quick installation, and opportunities for eye-grabbing aesthetics.
Rather than having a less appealing painted-block finished exterior, some communities are demanding both remodel projects and new construction blend into local surroundings. Government-approved ordinances are also having a huge impact. This is where stone veneer comes into play—new technology in masonry can help achieve desired outcomes at lower cost and with improved visual performance over some traditional assemblies.
Choices in manufactured stone veneers have expanded, lending both performance and customized aesthetic advantages. At the same time, the manufacturing processes to achieve certain performance characteristics have greatly advanced. What do design professionals need to know?
Technology advances and performance
Traditionally, both lightweight and full-depth stone veneers have been manufactured through a wet-cast process using latex molds for lightweight veneers. In wet casting, natural stones are arranged in a pattern, with latex sprayed on them to create a mold. When it comes time to cast the veneers, the molds are hand-painted with a colorant specified to resemble a particular variety of stone.
The resulting veneers are only colorized on the outermost layer. This means if the veneers are chipped accidentally, or purposely cut during installation, the non-colored aggregate on the interior becomes exposed. Additionally, special corner and trim pieces are needed to obtain finished, ‘real stone’ looks without sacrificing color consistency.
By comparison, a new mold technology known as the dry-cast production method can create products with longer lifespans and better dimensional stability. The proprietary processes are similar to paver technology, beginning by scanning natural stone and turning those scans into patented steel mold forms. A low-moisture mixture of fine aggregates, cement, admixture, and integrated colorant are densely compacted into the molds, then stripped from them and cured in a high-humidity environment. The resulting veneers contain only about six percent moisture, whereas moisture content in wet-cast can be upward of 33 percent. This mixture also contains water repellents and uses 40 percent less water than wet-cast methods. This means dry-cast stone is more resistant to the de-icing salts applied on sidewalks, whereas as wet-cast stone tends to soak them in and, potentially, disintegrate.
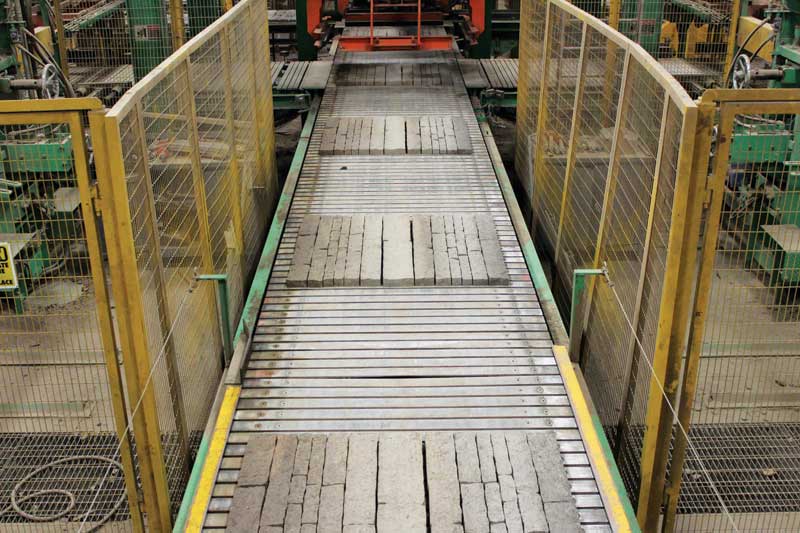
Dry-cast veneers are perfect for ashlar, stacked, and square applications requiring a stacked look, while resisting freeze-thaw stresses, water absorption, and fading at significantly less cost than their wet-cast counterparts. They are well-suited for residential, retail, and light-commercial construction given their speed of installation and versatility.
Additionally, the lightweight and full-depth veneers that are manufactured through dry casting offer a compressive strength two to three times greater than traditional wet-cast veneer. A dry-cast product averages 34,475 kPa (5000 psi), whereas wet-cast only approaches 13,790 kPa (2000 psi).
Although both dry- and wet-cast manufacturing processes face the same outdoor challenges, the former, with its higher compressive strength and water repellents, will absorb less moisture. It will also have a greater resistance to freeze-thaw issues, and be significantly less impacted by de-icing salts.
The dry-cast veneer process can create colors, textures, widths, and profile sizes similar to natural stone, enabling the two materials to be used together. Further, having color integrated throughout the unit (including finished ends) eliminates the need for special corner pieces and reduces waste caused by chipping. The question is, when might one specify a lightweight or thinner profile versus a full-depth one?