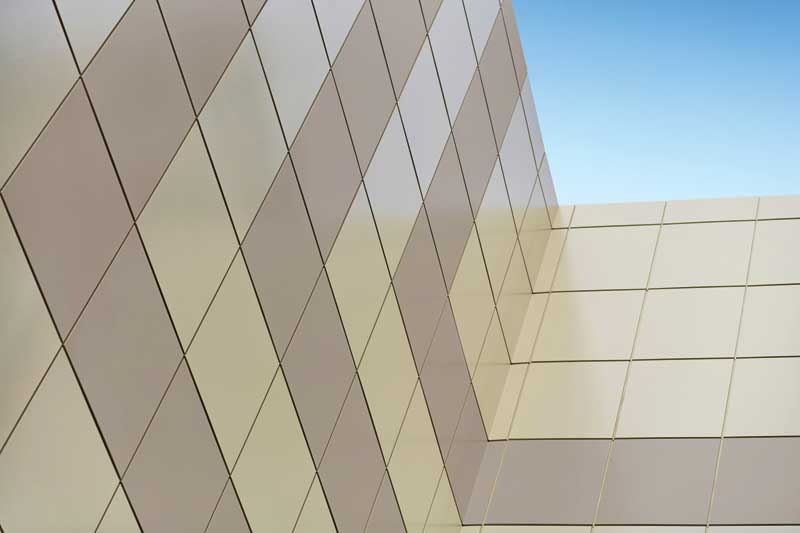
by Mike Couchie and Ron Partridge
As buildings and structures age, their exteriors can garner a lackluster appearance. Time and environmental conditions take a toll, and what was a once-vibrant exterior becomes faded and degraded. In this situation, owners, architects, and specifiers may be tempted to replace façade materials with new, factory-fresh materials—a costly, time-consuming endeavor. Instead, they should consider an exterior restoration using a field-applied coating.
Field-applied exterior coatings can help eliminate the expense and business disruptions associated with removing and replacing structures or façade materials. The right exterior coating could provide the same type of performance associated with its factory-applied counterparts; it can also often be custom color-matched to align a building’s exterior with branded or organizational color identities.
However, an exterior coating project should not be a quick fix. Careful selection of the right coating system and proper surface preparation techniques make the difference between a long-lasting finish and one that fails in several years.
Three questions that need answers before coating selection
To ensure the success of any exterior coating project, it is important for project architects and specifiers to be aware of several important details that affect the job itself as well as the performance and longevity of the coating system. The following questions should be part of the Request for Proposal (RFP) and discussion process with prospective contractors bidding on the job.
1. What are the environmental conditions to which the structure is exposed?
Sunlight, moisture, temperature extremes, wind, salt-laden coastal air, particulate, chemical pollutants, and abrasion can have a literal impact on a building façade’s coating, drastically breaking it down over time. Chemical agents and free radicals in sunlight, water, and atmospheric pollution can react with a coating’s chemistry and pigment particles, attacking the chemical bonds of the coating’s binder resin.
Often, the problem is more than just an aesthetic one—as coatings degrade and erode over time, they can take on a chalky consistency in which the coating comes off at even the lightest touch. Eventually, the coating may completely erode, removing the exterior material’s important protective layer and exposing the substrate. The potential results include rusting, pitting, mold/mildew growth, and other problems leading to structural failure if not remedied.
Therefore, RFPs should include details on:
- climate type;
- humidity;
- average wind speeds and gust extremes; and
- ambient chemical and particulate pollutants in the structure’s environment.
2. What is the substrate material?
In RFPs, architects and specifiers need to be clear about the type of material to be coated. It is important to ensure the coating selected has been specially formulated to work with the surface or surfaces needing refinishing. A formulation developed for stucco or masonry will likely not work on steel or aluminum surfaces, for example.
The condition of the existing coating system indicates whether complete removal or recoating is the best solution. The amount of corrosion or degradation, degree of coating defects on the surface, number of coats, and adhesion between coats are some of the factors that need to be considered before making an overcoat or complete removal decision.
Most coatings manufacturers provide information about substrate/coating compatibility on their product data sheets or in their field coatings application guides—both of which should be consulted by the project specifier, along with the coating’s SectionFormat specification. These documents provide important information about how to prepare the substrate prior to applying the coating system. It is critical to keep in mind some substrates require more preparation than others.
Prior to coating, substrates should be tested using ASTM D3359, Standard Test Method for Measuring Adhesion by Tape Test. Inadequate adhesion will cause the coating to delaminate and fail, eliminating its protective properties.