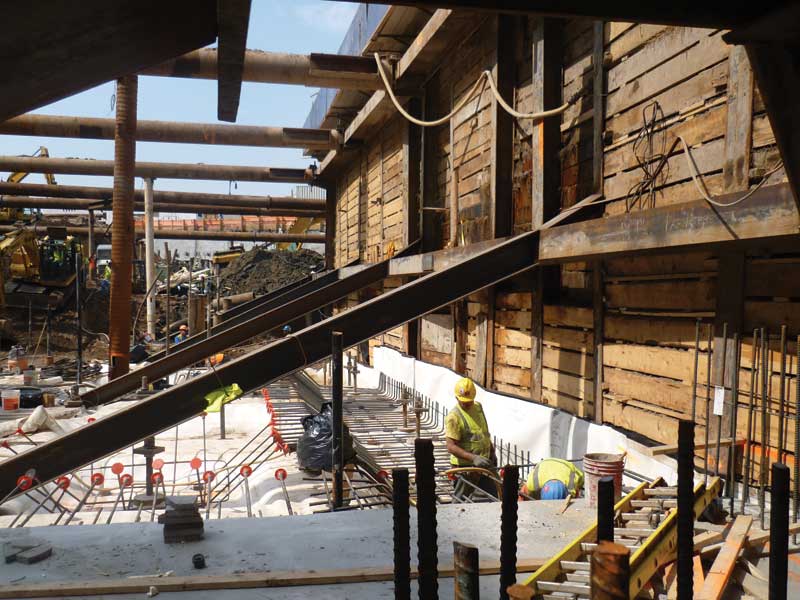
by Justin Henshell, FAIA, FASTM
Auditoriums and computer rooms that do not require daylight now occupy basements that formerly housed mechanical plants and vehicle parking. These sensitive occupancies require the spaces be waterproofed to prevent water from migrating through the basement walls and slab in contact with the wet, adjoining soil. (This article has been extrapolated from the second edition of the author’s The Manual of Below-Grade Waterproofing [Routledge, 2016].)
Basements are defined as habitable spaces constructed below the existing grade or a grade that will be increased in height to cover it. (Some building codes define a ‘cellar’ as a habitable space entirely below grade and a ‘basement’ as a habitable space partly below grade.) They must be designed to resist soil pressure, as well as hydrostatic forces occurring from the accumulation of stormwater or from a water table varying in depth above the lowest level of the basement or perched above it on a watertight strata.
Where adjoining construction or buildings do not encroach on the footprint of the building, the basement may be constructed above ground, and the walls buried with backfilled material or in an excavation.
Building a better basement
Excavated basements are built differently than the above-grade components of buildings. Generally, they can be constructed by one of two methods:
Bottom-up construction
The most common form of construction, the bottom-up method consists of first excavating the earth that will be enclosed by the foundation wall. Then, a soil retention system is installed and the concrete or masonry foundation walls are cast and braced against the soil pressure. The mat slab or pressure slab is then cast on grade at the bottom of the basement, followed by the foundation walls and interior columns.
Top-down construction
Few people would suggest building the roof first and then working down, yet, for some basements, this is an approved sequence of construction. In this method, the enclosing foundation walls are installed first, followed by the ground floor slab that is cast on the finished grade between them. The soil below the slab is then excavated and the subsequent lower basement floors are cast sequentially, finishing with the pressure slab at the bottom of the basement. Columns are inserted into drilled holes.
Generally, as the excavation progresses, the foundation walls are braced with cross-lot blocking or rakers and wales (or walers)—described later in this article—as the earth is excavated below the slab, exposing the foundation wall. Intermediate upper cellar floor slabs are cast as the earth is excavated to brace the foundation walls and columns. The pressure slab is cast after the excavation reaches the basement level (Figure 1).
Excavations and excavation supports
Where space is unlimited, a basement can be formed by simply excavating the soil, erecting foundation walls, casting the pressure (mat) slab on grade, and backfilling between the soil and the walls (Figure 2).
When space is limited to a few feet beyond a basement’s footprint, the basement can be formed by excavating and installing soil retention systems. A system consists of a network of braces and tiebacks called support of excavation (SOE). The American Society of Civil Engineers’ ASCE Guidelines of Engineering Practice for Braced and Tied-back Excavations explains the purpose of SOE. (Created by the Committee on Earth-retaining Structures of the Geo-Institute of ASCE, the 1997 resource is also known as Geotechnical Special Publication [GSP] 74.) An excavation into soil or rock causes a stress imbalance as lateral support is removed; deeper and steeper cuts create greater imbalance and risk. When the slope of the cut area is not flat enough to retain natural support, a SOE must be constructed to provide this (Figure 3).
If the width of an excavation is limited to the lot lines, the SOE is erected on them. The waterproofing is pre-applied to the SOE and the foundation wall cast against it. The earth-retaining systems can be used solely to retain the earth and act as deep water cutoff walls, or they may be designed to also serve as structural foundation walls to support the building above. (Excavating basements must be conducted in a relatively dry environment; this requires removal of groundwater and runoff from stormwater. Control of this water is accomplished by pumping called ‘dewatering.’ Site dewatering methods are thoroughly discussed by Daniel G. Gibbons, PE, and Payal R. Volra in their August 2016 article in The Construction Specifier, “Construction Dewatering.”)
The data in Figure 4 shows most soil-retaining systems are not suitable substitutions for a separate waterproofing system. Some shotcrete system manufacturers claim their systems combine the functions of soil retention, a structural foundation wall, and a waterproofing barrier. These one-size-fits-all systems have not proved to be a complete success despite attempts by (primarily) West Coast builders.
Soil-retaining systems must be restrained to resist soil and water pressure. The walls can be tied back to the earth on the outboard side or they must be braced internally where tiebacks cannot be installed outside the building footprint. As mentioned, bracing methods include cross-lot blocking, and a system of wales
(i.e. horizontal members connected to the inner face of the walls) and rakers (i.e. inclined struts connected at the top to the walers and braced at the bottom with heel or foot blocks). This is depicted in Figure 5.