FAILURES
By Deborah Slaton, David S. Patterson, AIA, and Mike Ford
At a three-story office building built in the 1980s, interior water leakage routinely occurred on the second floor. Typically observed during wind-driven rain, it resulted in wetting of interior finishes and subsequent mold growth.
The vertical enclosure for the building consisted of natural stone with concrete masonry unit (CMU) backup at the first floor, and cold-formed metal-framed cavity wall construction with brick veneer at floors two and three; a projecting horizontal stucco-clad band at the second floor and roof level created a 0.6-m (2-ft) deep soffit. Fenestration consisted of punched windows at the first floor, and vertical strips of fixed aluminum-framed windows spanning both the second and third floors with alternating insulating vision and spandrel glass infill.
What appeared to the building owner as a single problem actually had multiple causes. In fact, deficiencies in many of the exterior vertical enclosures’ water management systems contributed to the leakage.
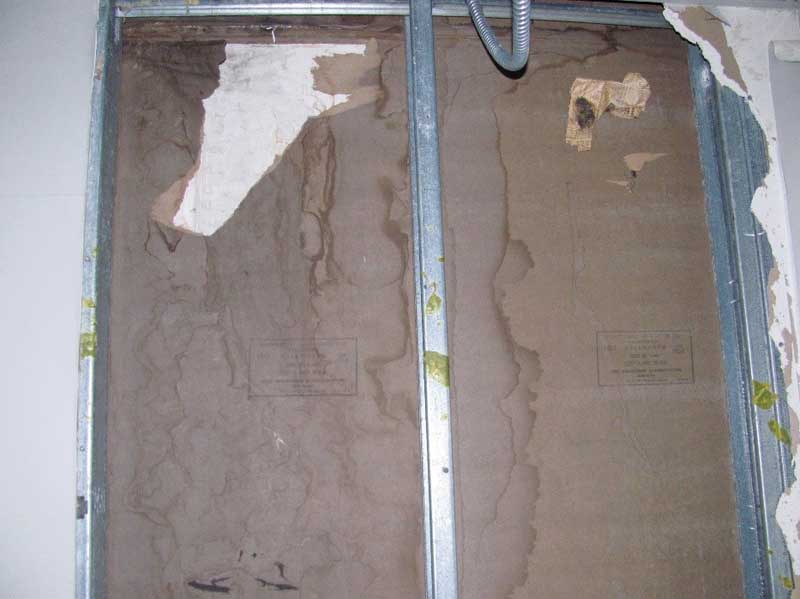
Photo courtesy WJE
For example, original window assemblies incorporated weeps at the sill of each unit to allow water entering window joinery to drain to the exterior. In an apparent attempt to address leakage, sealant had been applied to exterior window joinery to render the window units as barrier systems—this repair was not complete, leaving many open joints and pathways for water to enter these assemblies. As the weeps had been covered with sealant, the water was trapped within the assembly, entering the building through deficiencies in internal seals of the window.
Further, through-wall flashing was only encountered above the second-floor slab; this single line of flashing was required to manage water entering through the brick cladding at both the second and third floors. At inspection openings, there were no end dams (or vertically upturned ends) at interruptions in the through-wall flashing (i.e. windows) to prevent water captured by the flashing from flowing laterally into the wall rather than being directed to the exterior of the wall.
Additionally, breaches in the PVC flashing (including punctures during original construction and openings resulting from deterioration of the flashing or failed lapped seams) allowed water to enter the interstitial wall assembly.
Finally, numerous mortar bridges within the exterior wall cavity of the brick-clad wall provided a bridge along which water flowing down the interior face of the brick could migrate, subsequently flowing down the exterior face of the water-resistive barrier (WRB) protecting the exterior wall sheathing. During spray-testing, water ran down the interior surface of the WRB at an inspection opening where exterior sheathing had been removed, revealing water infiltrating the brick cladding had breached the WRB and consequently bypassed the flashing at the base of the wall.
Like humans, some buildings age more gracefully than others. Apart from the ‘cosmetic’ repair to the windows (and some leakage), the building’s appearance belied internal problems—the extent of which were only revealed by exploratory openings and diagnostic testing. In this case, the treatment was unfortunately costly surgery and replacement of critical water management components.
The opinions expressed in Failures are based on the authors’ experiences and do not necessarily reflect those of The Construction Specifier or CSI.
Deborah Slaton is an architectural conservator and principal with Wiss, Janney, Elstner Associates (WJE) in Northbrook, Illinois, specializing in historic preservation and materials conservation. She can be reached at dslaton@wje.com.
David S. Patterson, AIA, is an architect and senior principal with the Princeton, New Jersey, office of WJE, specializing in investigation and repair of the building envelope. He can be reached at dpatterson@wje.com.
Mike Ford is an architect and senior associate with WJE’s Northbrook office, specializing in historic preservation. He can be reached at mford@wje.com.