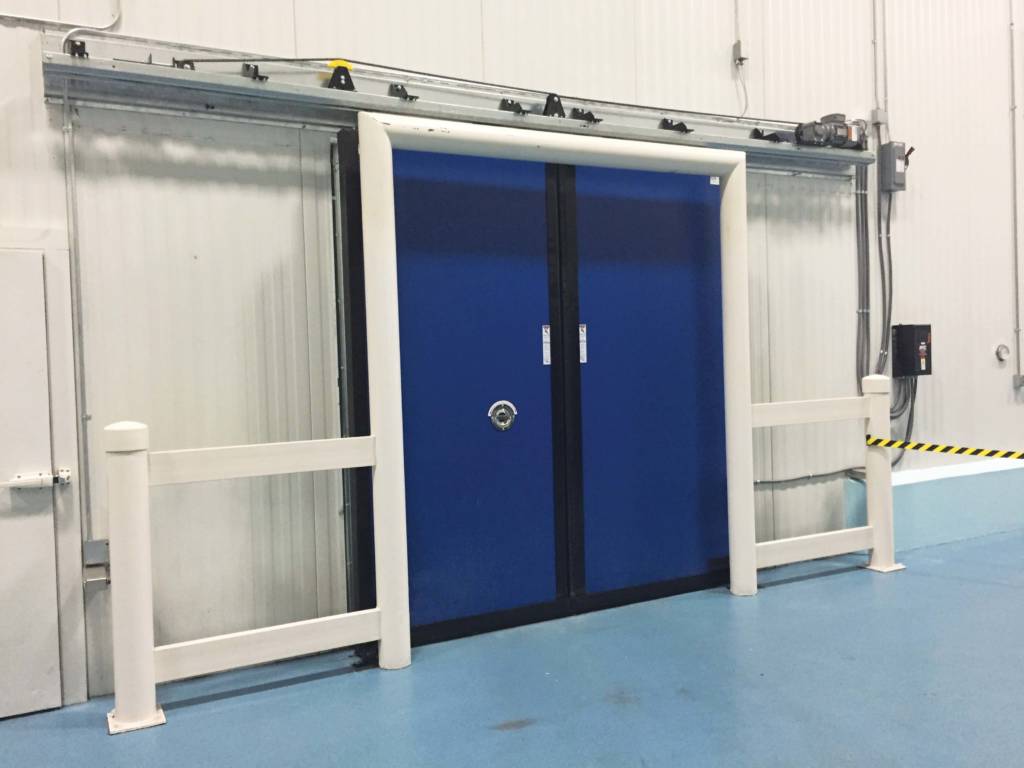
by Michael F. Watkins
The changes taking place in cold-storage operations over the past 20 years have called for new approaches in the traffic doors enabling access to these low-temperature rooms.
Visit any major city that goes back to the turn of the last century and one can spot buildings that used to distribute frozen and chilled food products, but have been converted into condos or offices. Some of these structures now stand as empty hulks in depressed areas of town, while a number of others have been torn down.
Multistory storage facilities were built as cost of land in big cities was high, but these spaces faced operational challenges. Product had to be moved into and removed from the building using freight elevators and involved the laborious handling of individual boxes of chilled food. Clearly, this was not an efficient approach.
This changed when America began expanding into the suburbs. The interstates that took people out to rural areas also enabled cold-storage distribution centers to no longer depend on rail service. These businesses were now able to leave the ‘big city’ and spread out in a single-story suburban building because land—at that time—was far cheaper than at the edge of downtown. These larger-footprint buildings also made it easier and faster to store and retrieve product for shipment. Meanwhile, improvements were made in both material-handling techniques and equipment to meet increasing demand.
One example of these changes was the 10-story Fulton Market Cold Storage Company Building, just west of downtown Chicago in the meatpacking district. As one blogger observed, before the 90-year-old building’s dramatic renovation to office suites in 2013, the building went through an epic refrigerator defrost, which was chronicled in a series of eerie photos. The owners vacated the building not only due to its age, but also because the inefficient process of moving product from floor to floor greatly cut into profits (The company is now serving its customers from a modern, single-story building in the suburb of Lyons.). (For more information, visit www.ediblegeography.com/defrost-prior-to-consumption.)
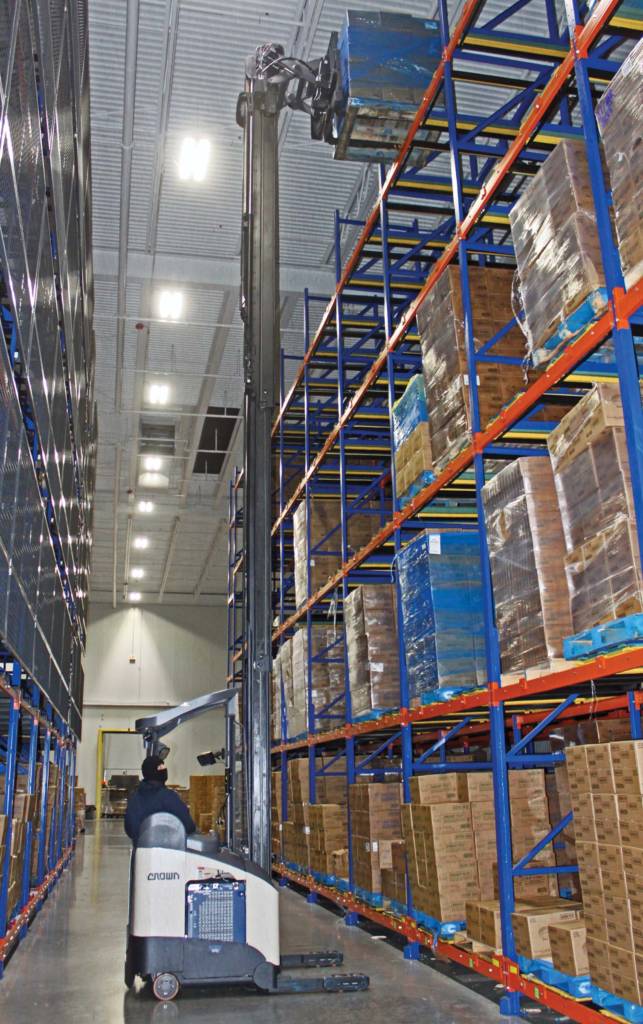
The trend in cold-storage facility height also began to change at the turn of the last century. A growing number of these third-party warehouses and rooms serving food processing plants are now going higher again, but not with multiple floors. Rather, cold storage is being done in one giant-sized room. Taller high-speed doors are enabling these facilities to meet customer and operational demands.
For cold-storage operation management and owners, when considering facility capacity, cubic feet have become more important than square feet. (For more, visit www.anccold.com/blog/cold-storage-construction-cost.) Now, the average height for cold-storage facilities is 11 to 12 m (36 to 40 ft) when compared to the 6-m (20-ft) height in the 1900s.
Raising the roof
These roofs are rising for a variety of reasons.
Decreased real estate costs
Rising land costs have caught up in the suburbs. Higher ceilings mean reduced square footage for a lower investment in real estate.
Increased capacity
Real-estate developer Jones Lang LaSalle cites a finding by HPA Architects that there is an opportunity to increase the pallet capacity of a building footprint by 12 to 25 percent by utilizing an 11-m (36-ft) clear height versus the old 10-m (32-ft) standard. (Visit cscmpaz.org/wp-content/uploads/2015/09/JLL_Industrial_Dist_Facilities-white-paper-April-2013.pdf for more information.) For example, in a 10-m clear height building, the study shows an occupant can stack 1626-mm (64-in.) pallets—these make up approximately 50 percent of the market—five loads high. With an 11-m height, that load number can increase to six high for a 20 percent increase in pallet positions.
Reduced heat loss
Modern Material Handling relates that high-density storage creates not only a smaller area to cool, but also an environment that better minimizes heat loss. (Read the article, “Best practices for managing a cold storage warehouse.”) A smaller footprint, for instance, translates into a smaller roof.
“Since the roof is one of the places in an operation where air can escape, it literally pays to keep the area as small as possible,” says Bill Leber, director of business development for the automation solutions company Swisslog.
Thanks for sharing the information.