FAILURES
Deborah Slaton, David S. Patterson, AIA, and Jeffrey N. Sutterlin, PE
One of the most critical (but often neglected) components in ensuring ‘watertightness,’ the roof assembly is typically installed early to protect the unfinished building from water penetration, enabling interior work to advance. However, this early sequencing requires the installed roof to withstand construction traffic and potential abuse for the remainder of construction while vertical wall assemblies, mechanical equipment, and other systems are being completed. Additionally, because roof surfaces provide convenient storage areas for building materials and equipment, and support for suspended scaffold or other means of access, completed roof assemblies can be vulnerable to damage from such construction-related activities.
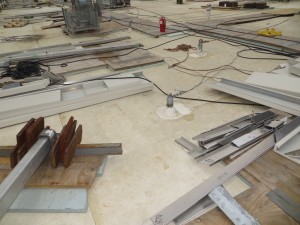
Over the past decades, single-ply membranes have increased in popularity for low-slope applications due to perceived advantages in installation, scheduling, energy efficiency, and pricing. In contrast to multi-layered built-up roofs (BURs), single-ply membranes—typically thermoset or thermoplastic polymer—consist of a relatively thin, single layer of waterproofing protection, resulting in an increased susceptibility to damage during construction. Although many single-ply membranes are reinforced to add strength, puncture resistance, and dimensional stability, when membrane damage does occur, it can result in leakage to the underlying roof assembly and building interior.
While the roofing industry generally acknowledges the importance of properly protecting a completed membrane from construction traffic and unintentional abuse, there are few guidelines regarding temporary protection. Instead, the industry appears to rely on the conventional wisdom of competent field personnel. However, common sense does not always prevail.
Recommended practices to protect single-ply roof membranes include:
1. Storage of material and equipment on completed roof membranes should be avoided. Where unavoidable, caution should be taken not to overload the assembly or underlying structural system and to provide proper membrane protection. Structural plywood sheathing over high-density rigid insulation has been found to provide low-cost, but effective, protection.
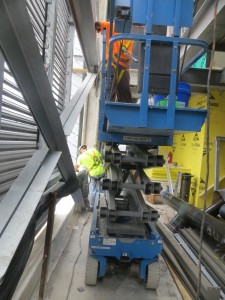
2. If construction traffic is anticipated in certain roof areas or pathways, a temporary walkway or layered protection should be provided.
3. The completed roof membrane should be constantly monitored and cleaned to prevent accumulation of sharp objects and/or debris that could damage the membrane.
4. Materials that may adversely affect the roof membrane should be identified and their proper use (and required membrane protection) understood and closely monitored.
5. On completion of construction activities, the roof should be thoroughly cleaned and inspected, with any damage repaired. Should membrane damage occur, infrared thermography or low/high-voltage scanning equipment can be useful for identifying moisture within the assembly.
6. Specifications and quality control procedures can be strengthened to ensure proper protection of completed roof assemblies.
The opinions expressed in Failures are based on the authors’ experiences and do not necessarily reflect those of the CSI or The Construction Specifier.
Deborah Slaton is an architectural conservator and principal with Wiss, Janney, Elstner Associates (WJE) in Northbrook, Illinois, specializing in historic preservation and materials conservation. She can be reached at dslaton@wje.com.
David S. Patterson, AIA, is an architect and senior principal with the Princeton, New Jersey, office of WJE, specializing in investigation and repair of the building envelope. He can be reached at dpatterson@wje.com.
Jeffrey N. Sutterlin is an architectural engineer and senior associate with the Princeton office of WJE, specializing in investigation and repair of the building envelope. He can be reached at jsutterlin@wje.com.
Protect the Roof was an interesting and thought provoking article where the concerns addressed are often thought of for protecting new concrete flooring in buildings, as equipment and machinery are moved into place. Laird Plastics in Portland Oregon, sells skids of 4 x 8 polypropylene sheets used for this purpose. The cost per sheet is relatively low and can be recycled. After reading your article, I believe this same product would make a good roof protectant; it’s water proof, strong and has been protecting new floors in the construction arena for years.
Cheers!
Leslie Case
Market Sales Specialist
Laird Plastics
Portland Oregon