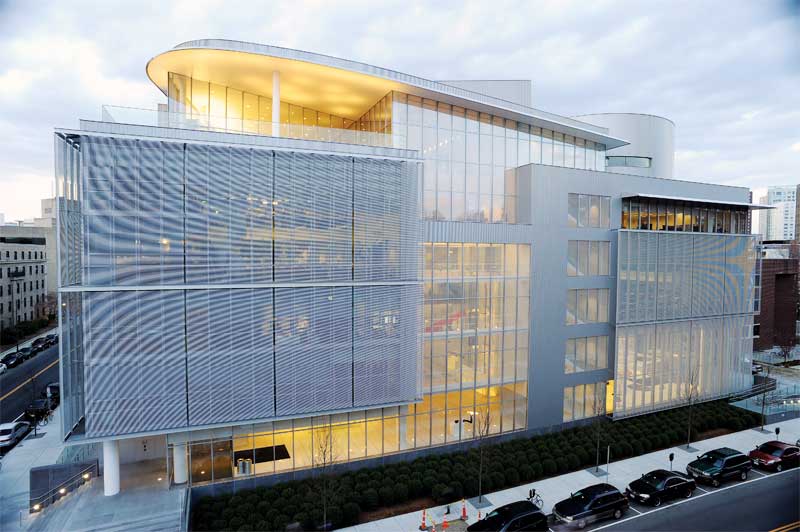
by Ben Mitchell and Gabriel Morales-Sada
Irrespective of the type of coating (e.g. powder or liquid) or the surface of application (e.g. extrusions, louvers, or metal coil), architectural coatings can be formulated with similar chemistries and performance characteristics. Why, then, would considerations such as color selection and matching be dependent
upon which coating application method was specified?
The answer lies in the fact that finish color is dependent upon good coverage as well as good technique on the applicator’s part. Variations in equipment, or even different settings and adjustments on the same equipment, can influence the way a color appears. To ensure multiple architectural elements within a given building envelope have consistent appearances, specifiers should coordinate with the coating supplier to manage pigmentation and color standards across various batches and application methods. Differences in final finish color can be apparent at the time of installation, or they can affect a building’s appearance after a few years of weathering. If variables are controlled during coating production and application, fewer inconsistencies appear as a result of exposure.
Understanding electrostatic coating application
Most extrusion and panel coatings are applied in a factory setting using electrostatic guns or sprayers. These guns are based on a familiar principle of physics—like forces repel and unlike forces attract. Coating particles (in the case of liquids, atomized droplets) are given a charge within the gun. A
high-voltage power supply provides a controlled level of electrons (negative charge) in the form of DC current. These electrons charge the coating through direct contact with conductive components in the atomizer or ionization field. When they leave the gun, the charged coating particles are attracted by the grounded metal substrate. Optimal grounding is provided by a rod driven directly into the ground and connected to the part, or to the part’s holding fixture, with a heavy gauge wire (Figure 1).
An ionization field takes the shortest path between the source of the charge and the grounded part. This attraction is strong enough to overcome the force of gravity, as well as any velocity a slight overspray may impart to the coating. Therefore, most of the sprayed coating ends up on the intended surface, making the system very efficient.
Achieving high transfer efficiency—defined as the ratio between the amount of coating adhering to a part and the amount of coating sprayed—results in consistent point coverage with little waste or recycle volumes. It also increases facility throughput. However, many factors affect the performance of this basic system. They must be understood and addressed during the coating application process.
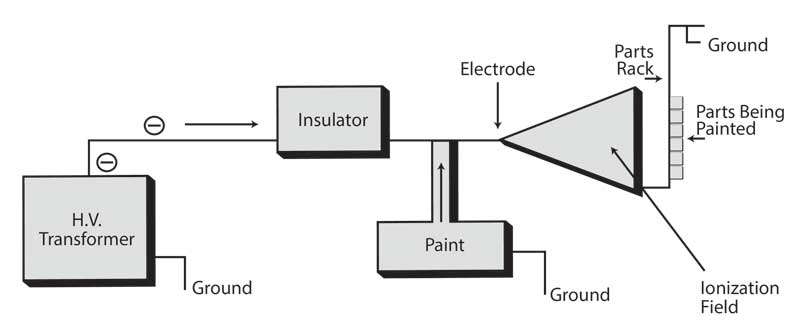