Microbreweries: Reducing energy costs through high-efficiency fan motors
HORIZONS
By Cheryl Higgins
Annually, breweries in the United States spend more than $200 million on energy, which is equal to three to eight percent of the production costs of beer. Surprisingly, microbreweries can consume as much as twice the energy per barrel of finished product as large breweries. They also have narrow profit margins, which makes energy efficiency measures a particularly effective way to save money and increase turnover.
Energy usage varies among brewpub operations. However, food preparation and HVAC consume the greatest amount. Typically, energy is viewed as a fixed expense—but, it is an easily controllable operating cost. With prudent energy efficiency investments, such as space-saving rooftop HVAC systems with high-efficiency fan motors, breweries are able to lessen energy costs and consumption while reducing their carbon footprint.
High-efficiency chiller systems and craft breweries
Few industries have seen as much growth and evolution in the past 30 years as craft breweries. This growing sector has changed the purchasing and drinking habits of many beer lovers. Energy management has become a major priority for brewery operators. As they have grown from hobbyist scale to more commercial significance, craft brewers have taken a growing interest in sustainability, particularly in terms of energy use. As production has increased in scale, energy efficiency has also become a more important financial consideration. (Click here for additional information on energy costs.)
In general, the brewing process involves:
- mixing (or ‘mashing’) malted barley and other grains with high-temperature water;
- draining the resulting liquid, or wort, off the mashed grains;
- boiling the wort while adding hops and (optionally) other spices;
- cooling the wort; and
- adding yeast and letting the mixture ferment
at a temperature that is best suited to the strain of yeast that is the best employed.
Once the wort has fermented, bottles are cleaned and filled with the resulting beer and packaged for delivery. Depending on the brewery, beer may be cellared or kept in cold storage before distribution. (For more information, click here.)
Refrigeration is a necessity in most breweries. Often, separate refrigeration systems are operating within a single brewery. Refrigeration costs can contribute to more than 30 percent of a brewer’s electrical consumption. (For more information, click here.) With energy prices already high and continuing to rise, paying attention to factors affecting efficiency, such as the chiller system, can pay big dividends. High-efficiency brewery chillers with PMAC fan motors—providing higher torque—can help reduce energy costs.
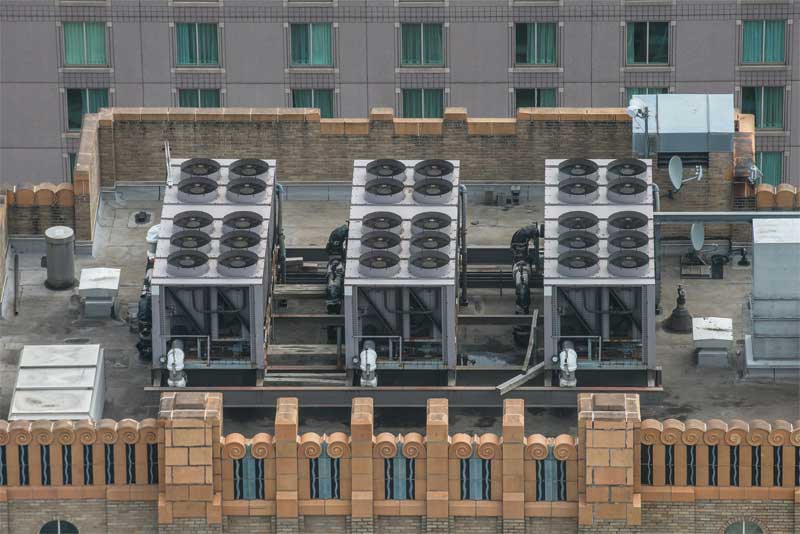
Self-contained HVAC systems
About half of all U.S. commercial space is cooled by self-contained, packaged air-conditioning units—including air-handling fans and sometimes also gas or electric heating equipment—sitting on rooftops.
There are a number of ways to achieve efficiency in the rooftop units, from adding coil surface to applying the latest compressor technologies (e.g. scroll, twin-single, and staging compressors) or equipping them with variable speed advances.
Highly efficient fan motors, the heart of HVAC equipment, are also extremely important to rooftop unit efficiency. Most of a rooftop’s power consumption is from the compressor, followed by the supply and condenser fans. However, because the fans run to provide ventilation even when the compressor is not on, they can account for up to 45 percent of the equipment’s energy use.
Increasing rooftop unit efficiency not only reduces energy use, but also lowers peak usage time (i.e. power used during the hours when the energy grid suffers the greatest strain), which supports better energy management for the facility and lessens environmental impact.
PMAC motors
The permanent magnet alternating current (PMAC) motor is traditionally a more complex construction than the standard induction one. The design has been simplified by using powerful permanent magnets to create a constant flux in the air gap, thereby eliminating the need for the rotor windings and brushes normally used for excitation in synchronous motors. This results in the accurate performance of a synchronous motor, combined with the robust design of a standard induction motor. The equipment is energized directly on the stator by the variable-speed drive.
Benefits for HVAC retrofits
One example of PMAC benefits can be found in commercial HVAC retrofits. In certain centrifugally loaded variable-speed applications (e.g. pumps, fans, and blowers), PMAC motors boost efficiency—and, in many instances, can direct-drive these designs. Fans are unique as they are typically sized by torque, yet direct-driving PMAC motors can eliminate the need for belts, pulleys, and sheaves. With power transmission devices like gear reducers simplified or removed, one can see increased service life of the entire drive system. Reduced maintenance is particularly helpful at buildings where fans are installed on roofs.
Motor-driven components used in HVAC and refrigeration are the highest energy consumers in both the residential and commercial sectors. (Click here for more information.) In the commercial segment, the combined HVAC and refrigeration categories account for 93 percent of motor-driven energy use. Clearly, both refrigeration and HVAC applications offer an excellent opportunity for helping reduce energy consumption.
For almost all equipment types in both the residential and commercial sectors, the market is transitioning to permanent magnet motor technology. This technology is becoming increasingly cost-effective—upgrading to a PMAC motor typically delivers a payback in just 12 to 23 months with a noticeable reduction in monthly utility bills. This motor type also offers other non-energy benefits, such as reduced noise and the ability to reach higher rotational speeds.