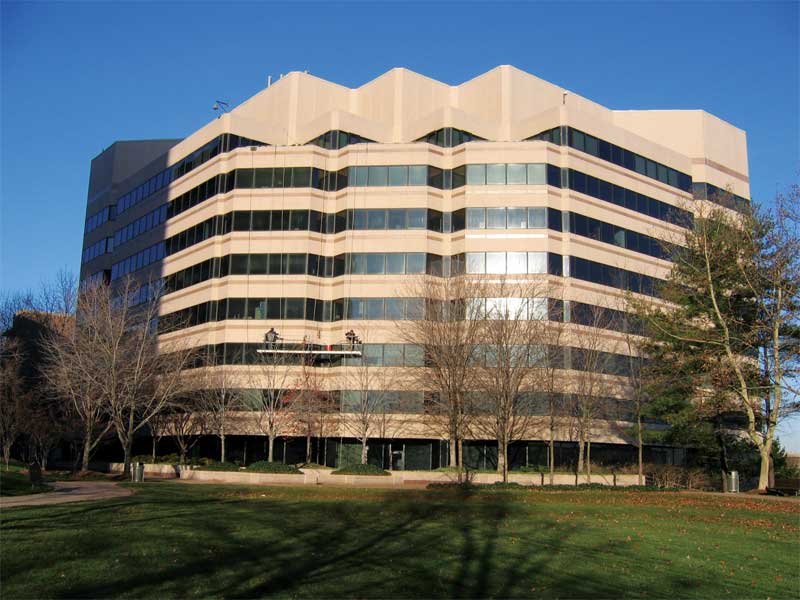
by Arthur L. Sanders, AIA, and Lawrence E. Keenan, AIA, PE
In both new construction and rehabilitation projects, sealant joints are often given short shrift when it comes to time and attention, as well as budget. Sealants often comprise the lowest percentage of a project’s overall cost—this is surprising considering all these products are asked to do.
As modern buildings have moved away from mass walls toward lighter, more pliant construction, designers rely on sealants to buffer those moving parts. With their multiple wythes and drainage channels, mass walls were designed to absorb and shed water before it reached the inner surface of the wall. Curtain walls and lightweight cavity walls depend on sealant joints to not only accommodate movement, but also to help keep the building interior dry. This is a lot to ask of a building element, especially one usually afforded only passing consideration.
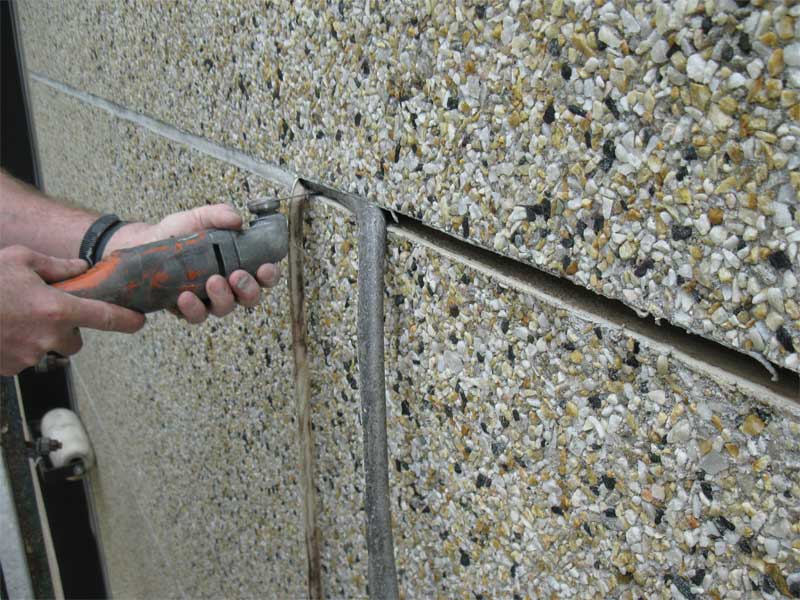
Precast concrete construction relies on sealant more than any other building type. Parking structures, in particular, have miles of sealant joints that must be maintained and periodically replaced. These joints frequently suffer from poor design and/or installation, as well as damage from high-heeled shoes and snowplow blades.
When sealant joint failure occurs, it can wreak havoc on the building envelope. Many joints are difficult to repair, and some concealed joints may be impossible to fix without demolition and reconstruction. Therefore, it is critical to design joints correctly, and to specify and properly apply an appropriate sealant. Before having a handyman attack cracked or missing sealant with a caulk gun, one must consider the substantial costs of rehabilitating water damage should the caulk fail. In the bigger picture, it is worth spending the time and energy on well-designed sealant joints to prevent premature degradation of building materials.
An age-old problem
Although naturally occurring bitumen- and asphalt-based materials have been used as building sealers for centuries, modern polymeric sealants were developed relatively recently. Acrylics and polyurethanes emerged in the 1930s, while water-based epoxies and silyl-terminated polyethers were not developed until the 1980s and 1990s, respectively. New sealant types, including proprietary mixtures, regularly appear on the market, each claiming to surpass the performance of previous generations of sealant products.
Modern sealants are composed of two basic elements: an elastomeric compound for flexibility, and some type of filler. During the mid-20th century, asbestos was a common sealant component, and poly-chlorinated biphenyl (PCB) was often added to impart desirable properties to the sealant. Unfortunately, subsequent research has linked both compounds with cancer, and the resultant cleanup process has led to no end of trouble for building owners and rehabilitation teams alike. (See “PCBs in Sealants.”)
Elastomers do just what their name says: they stretch. Sealants are usually polymers, composed of more than one type of elastic material. These pliable compounds bridge gaps at moving joints, where two building elements that move differentially intersect, as well as at static joints, which are relatively stable. Today’s sealants vary in composition to accommodate different applications, whether a high-movement expansion joint, a structural glazing seal, or a concrete control joint.