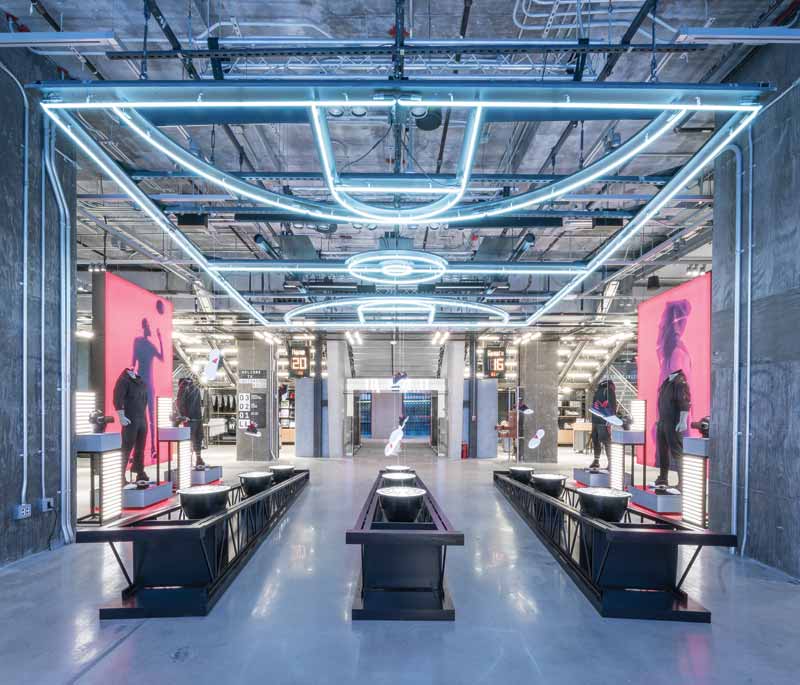
by Chris Bennett, CSI
In the classic 1967 film, The Graduate, the character Mr. McGuire famously tells Benjamin Braddock one word: Plastics. This iconic scene refers to a then-new material affecting all aspects of life. Plastic was everywhere; it wrapped food, replaced wooden toys, swapped out metal in automobiles, and displaced cotton thread in Fifth Avenue fashion.
This cultural change also manifested itself in the construction industry, not least among which was concrete. Acrylics, epoxies, and various ethylene-based materials began to enter the construction landscape in the 1960s. Even the marketing around concrete in construction was modified to encourage “plasticity.” Designers were influenced into employing high-range water reducers that went by the modern and keenly American-sounding name, “superplasticizer.”
At that time, construction methods gained a speed and flexibility with “plastic.” However, it is now apparent replacing cement, rock, and water with plastics has unanticipated negative effects, such as shorter life cycles as a result of deterioration and corrosion, which have affected buildings, bridges, and highways. (For more, click here.) The concrete of The Graduate’s era has not proven to be resilient, as is evidenced by the colossal budgetary allocations governments have requested for infrastructure repair. (For more, click here.) Building professionals compound this problem by adding even more plastic-based materials—epoxy skim coats above, vapor barriers below, and all manner of patch and repair materials in-between—when concrete fails.
In fact, tens of millions of acres of concrete are wrapped in “plastic bags” today, despite obvious negative effects to the environment (from using fossil fuels) and a property owner’s checkbook. Fears of failure and risk responsibility are partly to blame, but there are also those who have taken advantage of this fear to foster the continued use of 50-year-old slab designs that use plastic, now a billion-dollar commodity industry in concrete.
Fortunately, many discoveries have advanced the concrete sector in the last 50 years, with millions of square feet standing as evidence to post-1960s engineering and science. This article will briefly touch on a few technologies making a significant impact in lowering the use of plastic in the field of concrete: reactive copolymerizing solids (RCS), thinner control joints, hydro-demolition, and corrosion inhibitors.
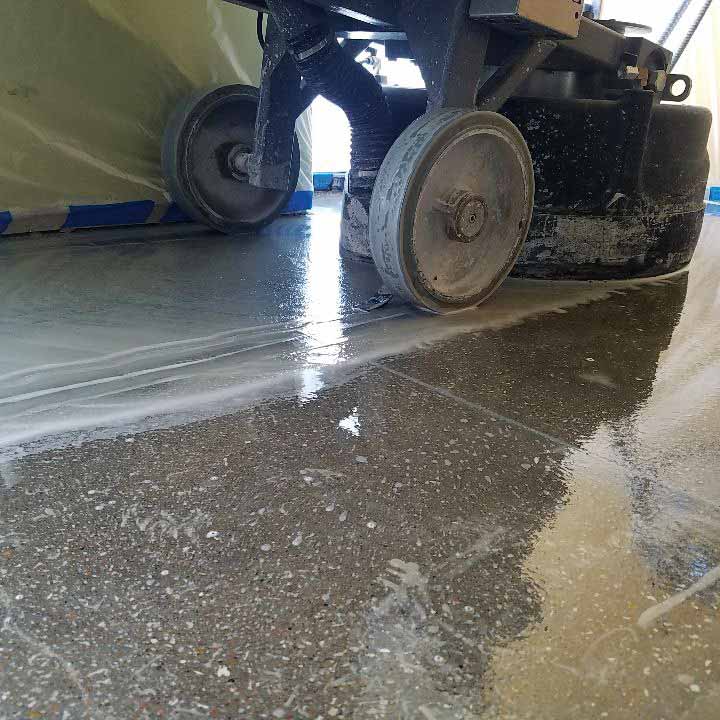
Photo © Chris Bennett
Reactive copolymerizing solids
Concrete’s strength comes from calcium silicate hydrate (C-S-H). It is sometimes referred to as the “glue of the built environment.” Traditional concrete is quite porous, allowing moisture, vapor, and contaminants through the open spaces in the C-S-H, and can necessitate the use of additional materials (e.g. plastic) to make up for this weakness. RCS describes a technology type that reacts with concrete to naturally close those spaces and encourage growth of additional C-S-H throughout the material’s life cycle. It is mostly employed in commercial applications but can be applied topically to any existing concrete surface or as an internal cure in new construction, eliminating the requirement for all additional curing methods and materials by making the concrete itself control water loss.
Builder Meyer Najem (CallisonRTKL and BSA Life Structures) employed integral RCS solutions to eliminate moisture mitigation products at the 11,334-m2 (122,000-sf) Community Cancer Center North in Indianapolis, Indiana. This technology contributed to cost savings during initial construction. Additionally, due to less vapor transmission, early strength gains in the concrete allowed for mobilization of other trades on an accelerated schedule—tile installation began 72 hours after the slab was poured, and complete polished floor sections were finished within seven days. By taking eight weeks off the construction schedule the project team was also able to positively impact the environment by lowering the use of diesel generators for equipment and lighting. The cancer center will also operate with lower maintenance costs because of a stronger concrete matrix.
Brian Harlow, vice-president at Fiat Chrysler Automotive (FCA), decided to move away from epoxy-coated floors for both operational and sustainability considerations. With more than 18-million m2 (200-million sf) of property under his care, this is understandable. By using an RCS technology at the award-winning Kokomo Casting Plant (KCP) in Indiana, FCA put an end to the need to routinely strip, prep, and repour epoxy, as the concrete itself can now be made to prevent hydraulic fluids, oils, and other contaminants from entering the automotive facility’s slabs.
In New York City, constructing Adidas’ flagship location downtown on Fifth Avenue meant contending with build-outs as well as maintaining the original building’s existing finishes to reduce the need for new materials. RCS was applied topically on both new and existing slabs to create a sustainable floor in an aggressive “Big Apple” timeline. Adidas AG and architect Gensler NY received many awards for this project, including the 2017 Retail Week Interiors Awards for best international store. However, a more significant reward was realized by reducing the project’s carbon footprint with a decrease in material usage.
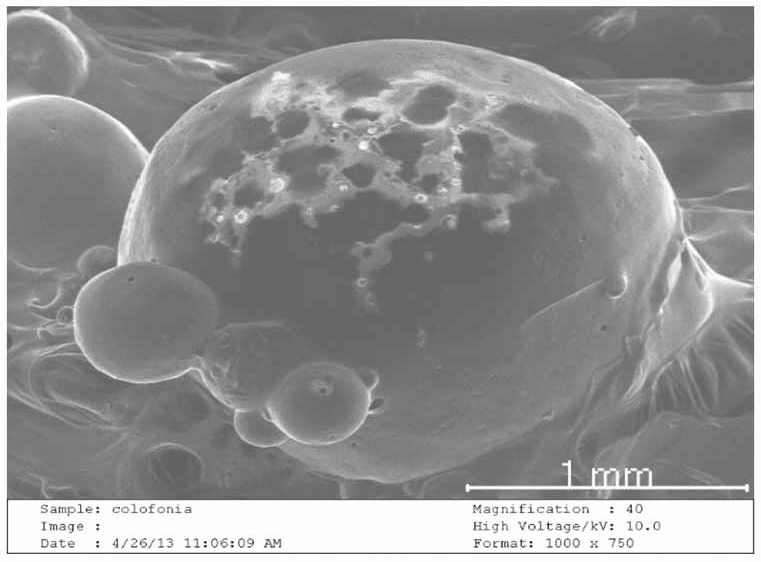
Image courtesy David Bastidas, PhD, University of Akron
Thin joints
Control joints are necessary in concrete slabs to control the cracking that occurs as the new slab moves due to thermal and volume changes while it cures. The 1960s-influenced concrete contracts or shrinks at a rate of nearly 25 mm (1 in.) per 31 m (100 ft) as it cures. While modern curing systems are less susceptible to volume changes, they are still at the mercy of thermal factors. Traditionally, most of the contraction happens in the first 90 days, but concrete continues to expand and contract with changes in temperature and humidity many years after being poured and placed.
Control joints are typically cut as soon as the slab can support the weight of the equipment and the saw operator to help reduce random cracking. However, the control joints raise additional maintenance considerations throughout a facility’s life cycle. With hard-wheeled traffic from pallet jacks, loading carts, and forklifts as well as foot traffic, control joints are subject to abuse, resulting in maintenance costs for owners. This is especially true in industrial and distribution warehouse facilities. It is not uncommon for some property owners to complain that more than 70 percent of their floor maintenance costs come from having to constantly clean and repair joints.
The standard control joint blade for many years was around 3 mm (1⁄8 in.) wide because the technology did not exist to make them thinner, but the late engineer Art McKinney, PE, SE, a fellow at the American Concrete Institute (ACI), pioneered the use of the now more common thinner control joint blade (around 1.6 mm [1⁄16 in.]) in North America. (The author worked with Art McKinney, PE, SE, on a number of large projects where “skinny” or “thin blade” technology was utilized.)
McKinney’s premise is thinner joints in a working facility better distribute the weight of rolling loads, thus reducing the amount of wear and tear on the joint areas. Minimal damage to joints means they last longer, so owners spend less time, materials, and money repairing these areas. Further, thinner joints require less joint filler material. This might not seem like substantial energy and material reduction to the carbon footprint of a facility, but hundreds of millions of acres of concrete slabs are being created. This change could influence millions and millions of lineal feet of joint space. The healthy impact to our environment by using half the “plastic” of current methods in this area of construction—achieved by simply making control joints half as wide as is currently being done—could be very substantial.